TAIF-NK: occupational safety and industrial safety are two sides of the same coin
Without accidents, injuries and occupational diseases: the oil refining company has summed up the results of ensuring the safety of the team and production facilities for the first quarter of 2023
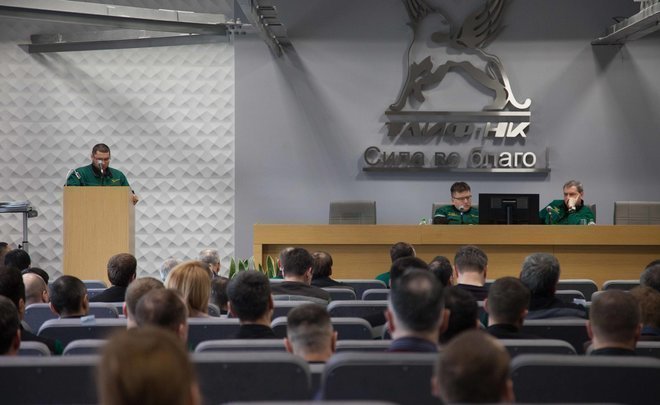
Work without risks and threats to life and health: increased attention is paid to ensuring occupational safety and industrial safety at TAIF-NK JSC. The issue is under constant control of the company's management, and the most responsible specialists can be marked and even get a serious boost for career growth. A journalist of Realnoe Vremya visited the meeting on occupational safety and industrial safety of TAIF-NK based on the results of the company's work in the first quarter of 2023.
“There are no trifles in matters of human security”
The fact that there are no trifles in labour protection and industrial safety issues was reminded from the rostrum to all participants of the meeting (about 300 managers and specialists of the company gathered in the audience) by the director general of TAIF-NK JSC, Maksim Novikov:
“The direct responsibility of managers at all levels is to organise safe working conditions and monitor compliance with all requirements," he stressed and added, “You have to work with the staff every day. We need to pay attention to each of our employees, up to what their mood is.
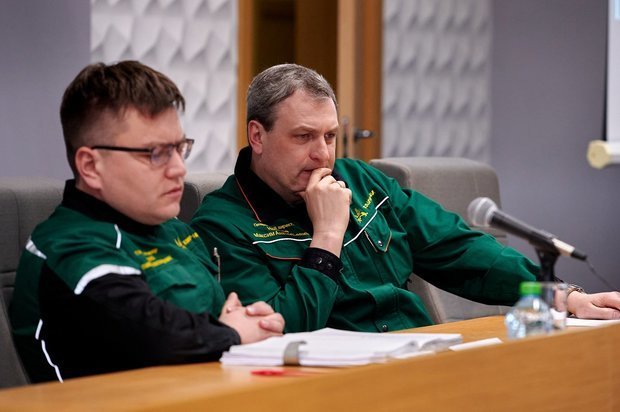
And this is not a metaphor or a beautiful figure of speech.
“In fact, I can't even understand what 'little things' are in labour protection. There are actions that an employee either has to do, or that he must not do in any case. And if there is an inaccuracy, an error, then this can lead to a problem. Perhaps not immediately, but such a situation can be compared to a glass in which water drips. One drop is not much, but gradually the glass will overflow and the water will splash out. Only water is harmless, it can always be wiped off, and here the price of a mistake is a person's health or life," said Rinat Kurmanov, the head of labour protection service of TAIF-NK JSC.

Besides, there are working conditions where there are also no trifles — neither in the use of personal protective equipment, nor in the quality and effectiveness of workwear and safety shoes, nor in noise levels, humidity, air cleanliness, etc., up to the well-being and mental state of each specialist in the workplace.
“We have never had and there is no goal to catch and punish someone. Our work is aimed at preventing violations and accidents. It is common for a person to make mistakes, they may look through tired eyes, perception may be dulled, something may be forgotten. There are moments that depend even on a person's condition, including their mood: they come in a bad mood, the whole world is not nice, and they may forget something. It is important to recognise such moments, to see, to instruct, to explain the danger of such behaviour and that a situation is possible when he poses a danger not only to himself, but also to those who are nearby, can let the team down," the head of the labour protection service of TAIF-NK JSC shared with the journalist of Realnoe Vremya.

In this work, the company's management and specialists of the labour protection service seriously count on the help of the team itself. In particular, labour protection commissioners:
“They are in every team, in every department, in every shift. Moreover, the commissioners are chosen by the collectives themselves by universal vote in the division on Day of Labour Protection. The main task is to ensure that our employees themselves think about the consequences of each of their actions, think about safety in the process of work. To form a zero percent tolerance in the collectives for any violations, no matter who commit them. We talk about this with the commissioners. And it is important for us not only to stop the violation itself, but also to understand the reasons that led to it in order to solve the problem itself, and not to fight its consequences," the head of the labour protection service of TAIF-NK JSC emphasised in an interview with Realnoe Vremya.
The applicant is convinced of how it is responsibly at TAIF-NK, as at any other enterprise of the fuel and energy complex (and oil refining is directly related to the industry), even at the stage of employment.
“First of all, each employee must correspond to the nature of the work performed for health reasons. Accordingly, to get a job at TAIF-NK, he undergoes a preliminary medical examination, psychological and narcological examination. This is practically the same procedure and in the same specialised psychiatric and narcological dispensaries as when obtaining a driver's license," Rinat Kurmanov shared in a conversation with the journalist of Realnoe Vremya.
State medical institutions with a staff of specialists, as well as maintaining their own database, are called upon to answer such serious questions as whether the applicant has drug or alcohol addiction, mental disorders, and whether he is susceptible to other factors that can influence decision-making.

Next, the applicant gets acquainted with the future place of work itself: the company as a whole, its production facilities, main hazards and risks, during the introductory briefing they are sent for training in occupational safety, after which they pass an internship directly in the shop.
“After completing the internship, since we have a high-risk enterprise, we check our employees for knowledge of our local instructions. A person who has not confirmed his knowledge will not be allowed to work," Rinat Kurmanov emphasises.
But at the same time, he notes that a person should understand why and for what this is done. It is primarily about the employee's own safety. And not everything is as difficult as it may seem: the responsible approach of the applicant to the process is already half the success.

With a certain frequency, workers of working professions, managers and specialists are trained in the basics of labour protection. Training programmes for specialists in various fields of activity are different. And everyone has the common goal: preventing injuries.
Healthy team — the well-being of the company
The health of each employee is one of the key priorities of TAIF-NK:
“This is very important for the company as an employer. Among other things, it is also the confidence that the employee will not let you down. This is especially important for a continuous cycle enterprise operating 24/7 all year round," Kurmanov noted.
Besides, work on the prevention of occupational diseases is ongoing.

“Prevention of occupational diseases is divided into two large and interrelated areas of our activity. The first is production control over compliance with sanitary rules and the implementation of sanitary and anti-epidemic measures by carrying out control measurements at the workplace at the enterprise for various harmful production factors — lighting, noise, vibration, temperature, humidity, air flow velocity... The results are compared with the standards, and if a discrepancy is detected, measures are immediately taken to bring the indicators back to normal," Rinat Kurmanov notes.
Moreover, the results of each such inspection are brought not only to the management of production facilities, workshops and sites, but also directly to employees. Every employee should know that everything is in order at his workplace.

“The second direction is a periodic medical examination. The most important task is to ensure that the person who comes to our company healthy remain healthy. If medical specialists have doubts during the medical examination, then each of our employees has the opportunity to undergo a follow-up examination, get recommendations for treatment. In addition, within the framework of voluntary medical insurance, each TAIF-NK employee is charged a certain amount annually — as a bonus from the company. Moreover, it is a very good bonus that can be used in medical and preventive institutions of the republic and beyond," the head of the labour protection service of the company believes.

To accurately comply with the terms of training, knowledge testing and medical examinations, so that there are no duplications or, on the contrary, there are no “forgotten” and not covered by training and attention of medical staff, digital accounting tools are being actively introduced in TAIF-NK, which are based on the special assessment of working conditions.
In digital form, there is a record of the issuance of special clothing, shoes and PPE. Moreover, the company also approaches the issue of choosing everything that is designed to protect employees with maximum responsibility.

“We do a lot of work: firstly, we draw up technical specifications to ensure that we are supplied with exactly the workwear and personal protective equipment that meet the characteristics of the production factors that are available at our enterprise. At the same time, a mandatory requirement is the availability of certificates of conformity. Samples of PPE undergo technical analysis, and employees of our production facilities themselves can take part in making the final decision, who will check workwear and PPE in real conditions. Then, comparing with the already used protective clothing, safety shoes and PPE, we make a decision: to purchase these samples or to use those that we already have in service. It often happens that there are simply no analogues that exceed the quality and requirements," Rinat Kurmanov said in an interview.
Occupational safety and industrial safety always go in tandem
“Certainly, in the process of working at a dangerous technological facility, in the process of performing technological operations and when working during emergency situations, it is always necessary to comply with the requirements of both labour protection and industrial safety. These concepts always go inseparably from each other," said Anton Vakhotin, the head of the Industrial Safety Control Department of TAIF-NK JSC.

“In this regard, many thanks to the management of the company. The work at TAIF-NK is structured in such a way that common goals and objectives unite teams. Besides, there is an opportunity to get to know each other better not only in a working environment, but also in a situation close, let's say, to combat: honing special skills of teamwork when solving problems in an emergency situation, we have, for example, during competitions among members of the NASF (emergency rescue formations) or competitions in the fire relay," Anton Vakhotin, the head of Industrial Safety Control Department of TAIF-NK JSC, supplemented his colleague.

Once a week, large-scale exercises to work out possible emergency situations are held at one of the production facilities under the leadership of Aleksey Khramov, the chief engineer at TAIF-NK JSC. Topics for classes in which employees of the selected site or workshop, and the NASF (emergency rescue formations), representatives of the Ministry of Emergency Situations and the gas rescue squad take part, are either suggested by the company's management, or are prompted by incidents at related industries somewhere in Russia or even abroad.

“During such exercises, there is an opportunity to practice the skill of joint action of both technological personnel directly at the production site and members of the NASF, who, if an emergency situation threatens, will be moved to the site for examination, first actions to rescue victims, cutting off the emergency area. And then, as part of the emergency services, they will begin work on localisation and liquidation of the accident. The course of the exercises is monitored not only by the production control service for ensuring safety, but also by the chief engineer's service. At the end, a general analysis is carried out: what comments are identified, what adjustments are needed. Moreover, comments are issued not only to the employees of the enterprise directly involved in the exercises, but also to third-party services involved in the exercises. This is necessary in order to better coordinate their actions in case of emergency situations and solve the problem as quickly and safely as possible," Anton Vakhotin believes.

There are a lot of production facilities at TAIF-NK, and such exercises happen once or twice during the year, in fact, in each of the divisions. But these are just such large-scale ones. In fact, work on honing the skills of personnel actions in the event of incidents of various kinds is held continuously.
“Training is conducted with each employee directly involved in the conduct of a technological operation in production. Once a week, the deputy head of the workshop personally devotes an hour of time to conduct this kind of training. This is mostly theoretical training, and specifically training sessions are conducted in practice. They also come in different levels: under the supervision of a shift supervisor, a shop supervisor. What's this for? There is a very simple example: in a real situation, often every minute and even second counts. It's about lives. And if these actions are not honed on a regular basis, then over time skills are lost — both speed, coordination of actions, and the pace of decision-making. There is such a thing as “training” in sports. In order to prevent this, regularity is needed, as a result of which everyone's actions are honed to automatism," the head of the Industrial Safety Control Department of TAIF-NK JSC is sure. He also added: “The interest of our management in the processes of ensuring industrial safety is in the first place because production facilities should work not only efficiently, profitably, they should also work safely and without accidents. This is very important.
It is important for people to have the opportunity to express themselves
Speaking about the results of 2022 and the first quarter of 2023, Rinat Kurmanov stressed:
“The most important indicator for us is the absence of injuries. According to the previous year and the first three months of 2023, there were no injuries, accidents, or occupational diseases at the TAIF-NK production facilities.

The entire multi-thousand-strong team of TAIF-NK JSC is involved in the processes to ensure safe and trouble-free operation. Moreover, the company holds competitions between teams for efficiency, accuracy and consistency in compliance with the requirements of labour protection, industrial, fire and environmental safety.
“Contests stimulate employees and help to identify the best people to look up to and strive for," emphasises Rinat Kurmanov. He also adds: “The very fact of the need for labour protection and compliance with labour protection requirements is beyond doubt. It's a duty. But, in addition, it is important to realise that you, while performing your duties, are doing it so well that you can also take a prize. And the prize-winning place opens up some great prospects in the future, including for career growth. You have declared yourself as a responsible specialist. A reward for a person is also an important incentive. He understands that he is going in the right direction. He understands the importance of his work, and understands that he can do more. This also affects professional development. Plus, it's also a monetary incentive.

Moreover, there is an opportunity to prove themselves not only on the scale of the native enterprise, but also at the municipal level, at the republican level, competing with employees of other companies and industries. The evidence that the TAIF-NK employees have seriously succeeded in this matter is the numerous certificates, diplomas and cups that adorn the walls and shelves in the department.
It has not been without encouragement this time. Both production, auxiliary social and household workshops (each in its own group) and the best labour protection commissioners received well-deserved awards for prizes.

Rustem Fatkhutdinov, the operator of technological units of the 6th category of the HRCC shop No. 02, has been working in oil refining for more than 10 years, and has been an authorised representative in his team for the last three years. And the third prize for him is the first such award.
“It seems to me that the control of industrial safety and compliance with labour protection requirements directly at the workplace, within the team is very important. To study and prevent violations from the inside, to prevent them," he shared with the journalist of Realnoe Vremya. He also added that this award belongs to the entire team that he represents. And a high rating is a reason to make even more efforts to improve safety and work efficiency.
The second personal place went to Ruslan Gismatullin, a commodity operator of the 6th category of shop No. 07 of the Gasoline Plant.

“I feel proud, of course. It is not an easy task to win the first place. And this is the result of our joint work. It is not enough to detect disorder. But when the shift eliminates the remark, this is the effect. We all in the team understand each other perfectly. There is a sense of shoulder and understanding of each other," said Yury Chetyrkin, the owner of the first place in the competition for the title of “The Best Commissioner for Labour Protection in 2022", operator of technological units of the 6th category of shop No. 04 of the Gasoline Plant. His experience at the company has been 16 years, of which 14 he is the commissioner. For him, this is also the first victory in the competition, which only emphasises the significance and importance of the award.

As for the effectiveness of the work of the TAIF-NK JSC team, including in matters of improving safety, the winner stressed:
“A lot has changed over 16 years. The production itself is improving, the production culture itself is improving. We're going forward, not backward.”
Подписывайтесь на телеграм-канал, группу «ВКонтакте» и страницу в «Одноклассниках» «Реального времени». Ежедневные видео на Rutube и «Дзене».