Maxim Novikov: ‘We make products of the highest quality, demanded by the market’
Product range of TAIF-NK JSC has more than 40 items. In 2023, it is planned to add at least two more
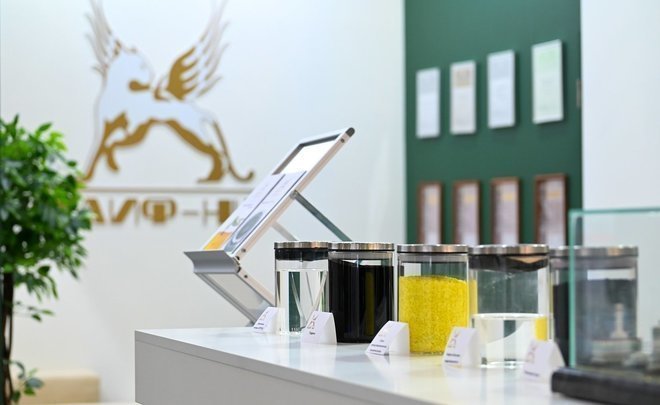
The year 2023 will be an anniversary year for one of the most modern and innovative oil refining companies in Russia: TAIF-NK JSC plans to celebrate its 25th anniversary. Over this time, the production of a wide range of products has been established. It will be discussed in our material.
Oil refining products around us
It is not an allegory at all. It is enough just to look around and understand how much “combustible liquid, which is a complex mixture of hydrocarbons," and the companies, capable of refining oil into products and intermediates going for further conversion to petrochemical production, mean in the life of every person on our huge planet.
Construction materials, roads on which millions of cars pass every day, a significant part of the elements of equipment itself, including paint coatings and tyres, fuel for cars, rail, air transport and ships, the most complex scientific equipment and the equipment of spacecraft, packaging for food, gum, fabrics, shoes and clothing, sports equipment, medicines, medical equipment and dental and orthopedic prostheses, cosmetics, solar panels and battery cells, children's non-staining crayons and strollers, outdoor furniture and home furniture…
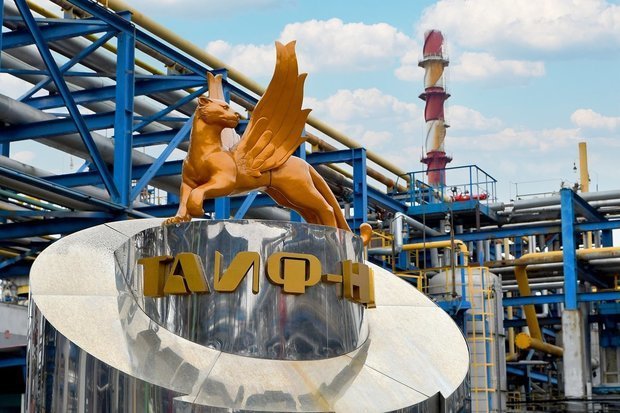
In fact, if you look closely, then, probably, there is a piece of the work of oil refiners in absolutely everything. Tens of thousands of products and components are created with the help of additional processing and combination of raw materials obtained from oil. Including those products that are obtained from millions of tonnes processed annually at three production facilities of TAIF-NK JSC: Oil Refinery, Gasoline Plant, and Heavy Residue Convertion Complex.
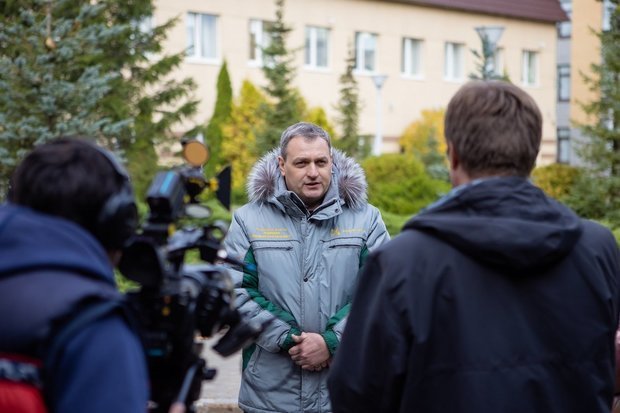
“The products we make, including fuel, are of high quality and in demand by the market. Logistics chains will change — maybe the price situation will change somewhat, but the demand has always been and will be," Maxim Novikov, the director of TAIF-NK JSC, emphasises.
The journalist of Realnoe Vremya visited TAIF-NK, got acquainted with the capacities of the enterprises and found out what the company already produces, what it has abandoned and what else the company plans to start producing in the foreseeable future.
A quarter of a century ago
1997. The country is emerging from a protracted economic crisis caused by state restructuring. TAIF JSC is engaged in the modernisation, but in fact, the revival of the petrochemical industries of the republic. The issue of capacity utilisation is acute, and Tatarstan does not actually have its own oil refining.
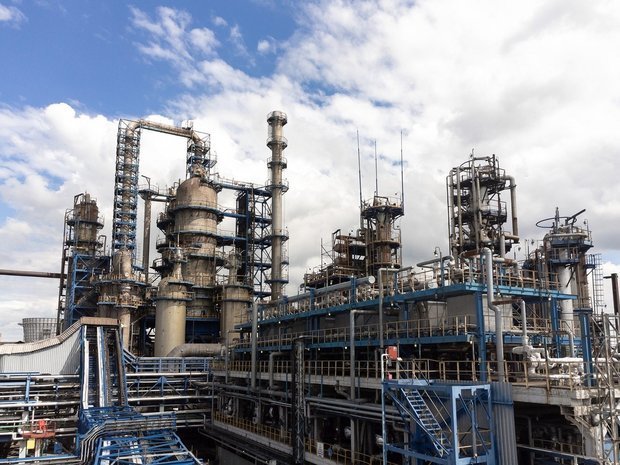
At that time, there was the primary oil refining plant — ELOU AVT-7, built as part of Nizhnekamskneftekhim back in 1979, with a design capacity of 6 million tonnes a year in raw materials. But the unit was underloaded by that time and needed serious modernisation. TAIF JSC leased ELOU AVT-7 from petrochemists, forming the oil refining company in Nizhnekamsk in 1998 — TAIF-NK CJSC.
First two products
Modernisation of the equipment of the newly created company began almost immediately. In 1998, the unit was already fully loaded. True, the conversion rate was far from the current one, and the assortment was not striking in its richness.
“The product line was minimal then. Initially, everything was built to provide raw materials — straight-run gasoline of the Ethylene 450 Plant (later Ethylene 600). The residual product was mazut, which was used as fuel for thermal power plants," Vladimir Lakhomov, the director of the TAIF-NK Oil Refinery, recalls about those times. He has been working at the company since 2000, and many processes for the modernisation of production and the development of new products took place before his eyes and with his direct participation.
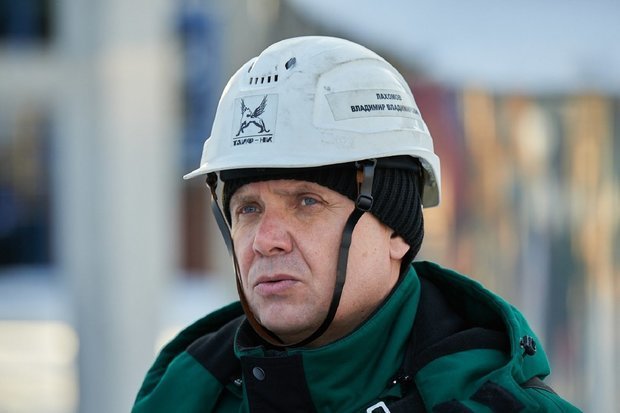
For the production of ethylene, straight-run gasoline is, of course, not the only possible raw material. Liquefied petroleum gases (LPG), NGLs, and ethane are also suitable for this. We have already written about this not so long ago. But naphtha in many countries of the world (and Russia is no exception) is the most popular raw material for the petrochemical industry, where ethylene, propylene, butadiene, butylene, isobutylene, acetylene, benzene, divinyl are obtained from it…
“Today, all straight-run gasoline produced by ELOU, plus the flows of the HRCC and the Gasoline Plant have now been added to it, goes into the reservoirs of Nizhnekamskneftekhim in mixed flows. There, its pyrolysis takes place with the production of ethylene and a number of other products that are valuable raw materials of petrochemistry," explained Vladimir Lakhomov.
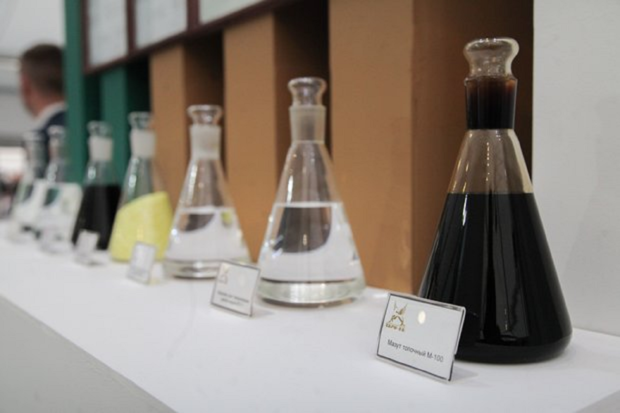
It is naphtha, and only it, can provide high-value raw materials for further processing in sufficient volumes. The product line of Nizhnekamskneftekhim, the main consumer of straight-run gasoline from TAIF-NK, today exceeds 120 items: an almost complete line of synthetic rubbers, glycols, plastics, polyesters, monomers, and surfactants. One of the goals of the domestic petrochemistry is the development of polyurethane systems (so far there are no own productions of this polymer in Russia). At the same Nizhnekamskneftekhim, where TAIF-NK supplies straight-run gasoline, there is almost everything necessary for the production of methylene diphenyl diisocyanates (MDI) and toluene diisocyanates (TDI) — key components for polyurethanes. There is only no license for the technology.
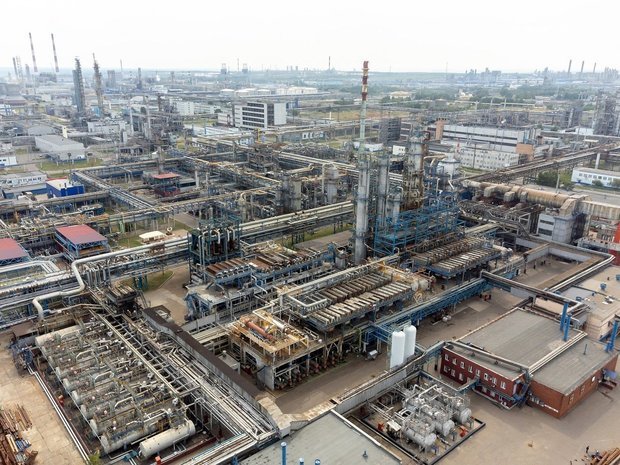
But as for mazut, today it has practically lost its position as a marketable product. But it has become a valuable raw material — it is sent for further processing with the extraction of light, high-quality and high-margin petroleum products.
From shop to factory
In fact, to date, a huge production complex has grown out of the only unit of ELOU AVT-7 for a quarter of a century, with which there is little that can compare in the territory of Russia, and beyond, in terms of the totality of implemented innovations and unique technologies. The heart of the company remains the Refinery, in which today it is unlikely that the creators of that first unit themselves will be able to recognise familiar features.
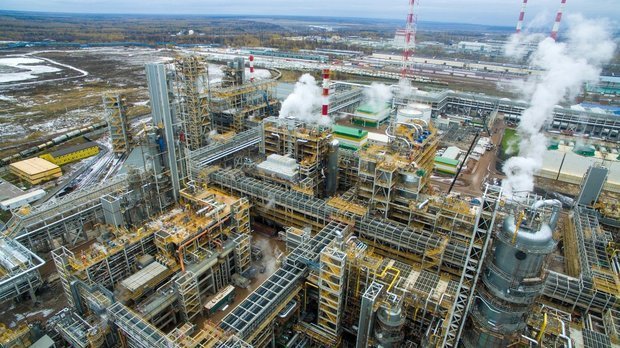
“The designers had to do their best to make the unit overgrown with the complex of hydrotreating of medium distillates, visbreaking unit. In parallel, the Bitumen Plant was built, commodity storages were expanded. A huge work was done — one workshop was turned into a huge plant with an existing assortment of manufactured petroleum products," says the director of the TAIF-NK Refinery JSC.
Striving for the best result is one of the characteristic features of TAIF-NK JSC. As the company's CEO, Maksim Novikov, is one hundred percent sure, this process is endless:
“As far as I can remember, all our life we have been building something, achieving some results: either an increase in productivity, or the expansion of product range. Naturally, the whole range of products has always been and remains high-quality. There were many stages, but we always kept up with the times. As it is now," he stressed in an interview with Realnoe Vremya.
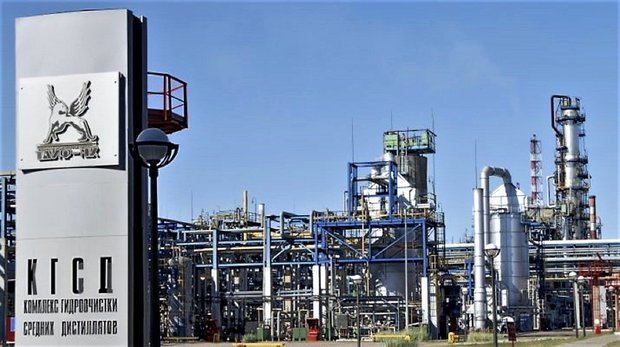
Hydrotreating processes are impossible without significant amounts of hydrogen. The project with a capacity of 16,2 thousand tonnes a year at TAIF-NK Refinery was put into operation in 2002. And in 2013, during the following modernisation, the plant's capacity was increased to more than 19 thousand tonnes a year.
Sulphur extracted during hydrotreating from straight-run kerosene and diesel fractions, cracked distillate fractions is another valuable product of production. The sulphur extraction plant with a granulation unit was put into operation in 2003. Then its design capacity was 35,14 thousand tonnes a year.
“I remember how we got the first sulphur. They made a medal — pressed liquid sulphur and established the day — Sulphur Day. Every year they gathered on this day. In autumn, in September. On a picnic in nature. We played football, volleyball," recalls Ramil Valeev, one of the veterans of the production, shift supervisor of the refinery shop No. 03.
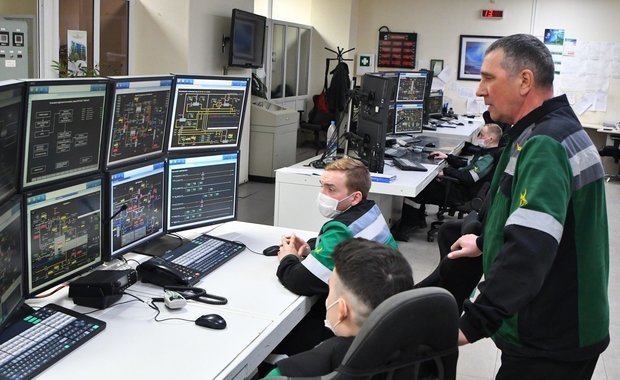
In 2014, for the growing production volumes, the plant underwent a deep modernisation and increased its capacity by more than 1,5 times: up to 55,113 thousand tonnes of granular sulphur a year. Sulphur is a product in demand by the market. One of the key areas of application is the agro-industrial sector of the economy: the creation of highly effective fertilisers.
The resulting vacuum gas oil, along with tar, is a raw material for further, in-depth processing at the HRCC. And the hydrotreated kerosene fraction is the basis for the production of diesel fuel.

In 2012, TAIF-NK was the first in Russia to switch to the production of Euro 5 class diesel fuel. The total volume of production of all types (summer, off-season, winter — ed.) of diesel fuel at the company's facilities is almost 3 million tonnes. Such figures were announced by the company's management based on the results of financial and economic activity in 2022.
Following the results of the republican and All-Russian quality competitions, Euro 5 winter diesel fuel became the winner of both.
By the way, TAIF-NK has been an active participant in both the regional and All-Russian stages of quality competitions for many years. According to the results of 2022, five types of the company's products were awarded high awards at once. Euro winter diesel fuel and AI-95-K5 gasoline were recognised as laureates, three more products were recognised as diploma holders: naphtha — hydrocracking gasoline, PG70-34 bitumen binder, and RT jet engine fuel. And the company as a whole was awarded the highest award of the All—Russian competition "100 Best Products” — the Quality Leader prize.
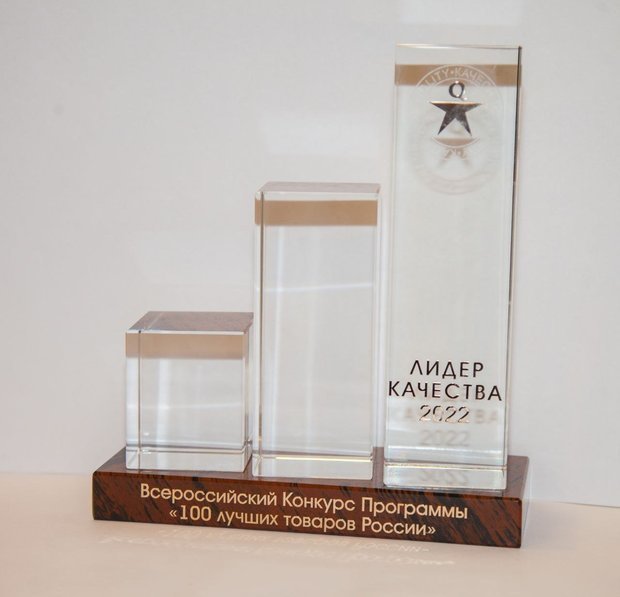
“There is nothing unusual in that our diesel fuel became the winner in the quality competition. At TAIF-NK, Euro winter diesel fuel and all other types from a wide range of our products are produced in strict accordance with all requirements of GOST, technologies, etc. That is, we can produce goods of better quality than it is prescribed in the requirements, but not worse. And this is the main trump card of companies that value their reputation: at any branded filling station (both ours and competitors'), fuel produced only according to GOST is sold. Therefore, if you want quality, welcome to the filling stations of large manufacturers that guarantee quality, including ours," the director of TAIF-NK oil refinery, Vladimir Lakhomov, is sure.
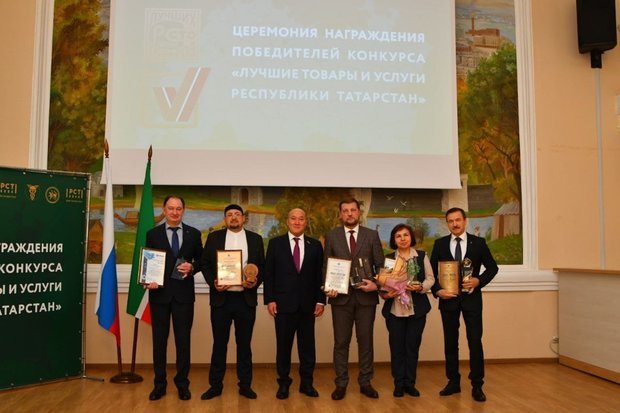
“Diesel winter fuel is not just in great demand. It is sold literally “just-in-time”. At the government level, there are not even recommendations, but requirements: not to reduce the production of winter fuel and, at the same time, to sell it as much as possible on the domestic market without exporting it," the director general of TAIF-NK JSC, Maksim Novikov, said in an interview with Realnoe Vremya journalist.
“The fuel that we produce, requires indicators, according to GOST, such as cloud point temperature of 22°C below zero (we have 24-25°C below zero) and maximum filterability temperature — the main indicator of low-temperature fuel according to GOST 32°C below zero, and TAIF-NK fuel on average has maximum filterability temperature of 44-46°C monus zero. That is, if you potentially have a desire to drive your car on fuel from TAIF-NK to the Arctic, then our fuel will allow you to do it," Aleksey Khramov, the chief engineer of TAIF-NK JSC, added.
It would seem that what else can be improved in what is already almost perfect? And how can the diesel fuel line itself be expanded if summer, off-season and winter already cover operating conditions in all weather conditions? It turns out it can!
The Arctic diesel mixed fuel with a package of special additives. It is capable of operating in even harsher conditions.
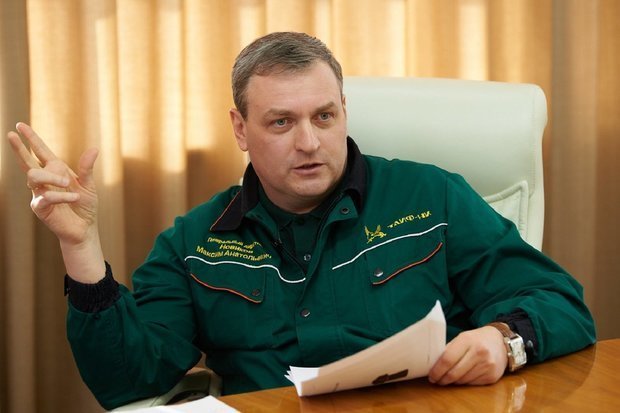
“We are not talking about obtaining a product by laboratory means, but a real experimental batch that will be implemented, and we will understand whether we should put this product at the industrial level. At the moment, the price of Arctic fuel does not differ much from the cost of winter diesel fuel. But, of course, Arctic fuel will need its own chain of production equipment, which will either have to be withdrawn from existing schemes, or a new one will be built. The specifics of the product are such that interest in it is not constant. If there is demand and a good price, then, of course, we will do it," said Maxim Novikov, the director general of TAIF-NK JSC.
But this is not all. It turned out that it is still possible to improve working and environmental performance.
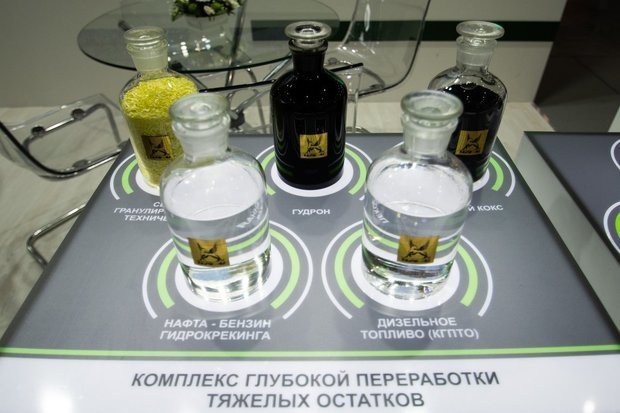
“We have issued our own technical specifications based on the current GOST, but with stricter requirements for the sulphur content in the fuel, it was reduced by half — from 10 ppm to 5 (for information: ppm — in Latin: pro pro mille, or one millionth of a fraction, that is, 1 ppm is 1 mg/kg of sulphur in the product — ed.). In terms of moisture content — a decrease from 200 ppm to 100. Indicators such as the content of polycyclic aromatics, oxidative stability, and flash point were also improved. All this together allowed TAIF-NK to obtain fuel that is more environmentally friendly, more operationally high-quality, reliable for an internal combustion engine, significantly exceeding the requirements of the current GOST," Aleksey Khramov told about what the new diesel fuel is.
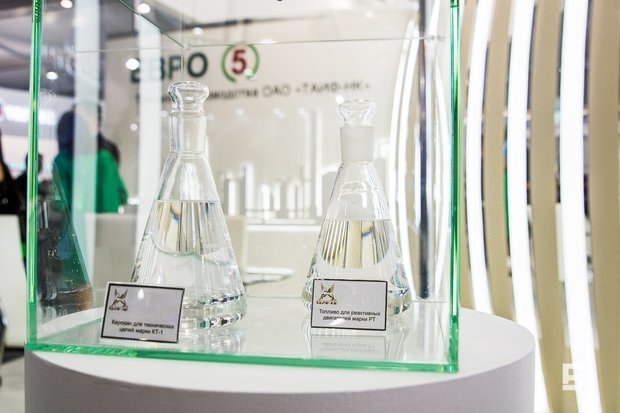
According to him, while the product created at the HRCC is a little ahead of its time, but this is a signal to consumers: the company is ready to ensure production and delivery as soon as the product is in demand by the market. By the way, the new product did not go unnoticed at the federal level. TAIF-NK Euro 6 diesel fuel, off-season, grade E, ecological class K5 by the end of 2021 became the winner of one of the most prestigious quality competitions in the country — "100 Best Goods of Russia”.
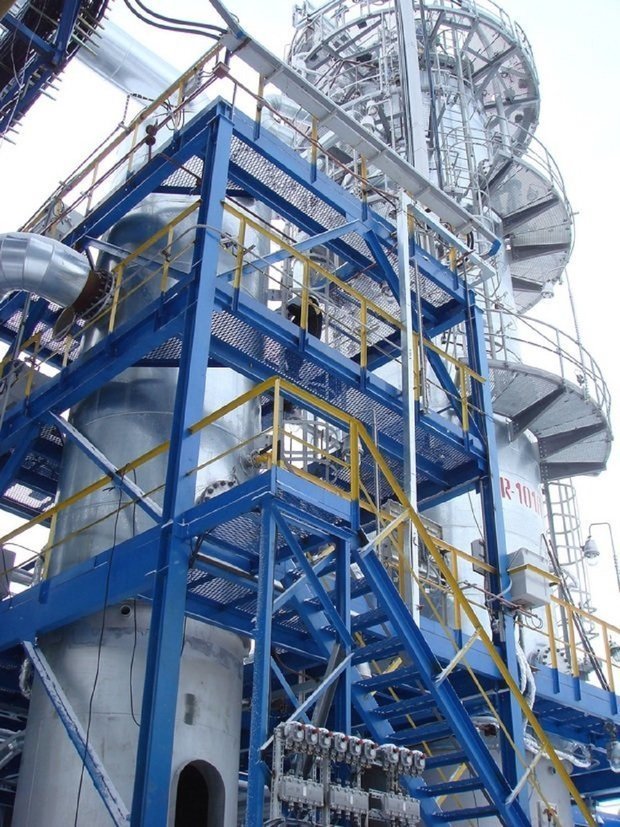
Speaking of bitumen. The unit, built in 2007, is capable of producing almost 140 thousand tonnes of oxidised road, roofing, and construction bitumen a year. Despite that this product is not the most cost-effective, and tar could well turn into naphtha, kerosene, gasoline, jet fuel and other high-margin products at the HRCC, TAIF-NK produced it, produces it, and will continue to produce it.
Why? The answer is simple and lies on the surface: the actively growing economy of Tatarstan cannot do without high-quality construction and roofing materials, without logistics arteries — numerous roads and highways. This means that the republic needs tens of thousands of tonnes of various bitumen. Moreover, the company is ready to create new mixes for specific, often unique tasks. There are prospects for this.
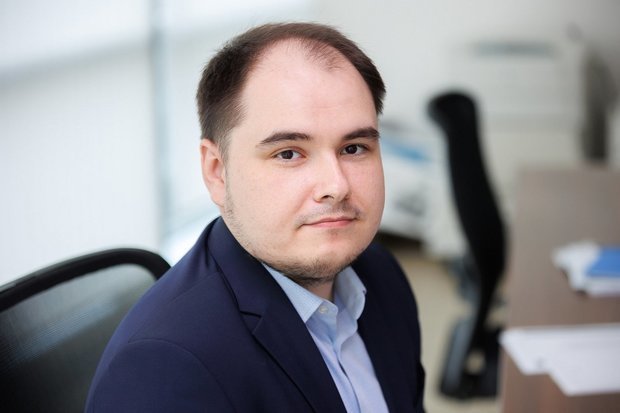
“We always expand the range of our bitumen products in accordance with the requirements of new GOST, taking into account the requirements of our consumers, so we can say that the initiators of the development of new bitumen brands are our consumers. There are cases when consumers, and there are both domestic and foreign, need bitumen with specific physical and chemical properties that differ from the standard requirements of GOST. Based on the experience that we already have, we conduct laboratory tests on the basis of the central factory laboratory of TAIF-NK Refinery and then, when we are convinced of the stability of the modes that laboratory tests show, we transfer production to the industrial unit," the deputy head of the petrochemistry and oil refining department of TAIF JSC, Marat Idrisov, explained in an interview with the journalist of Realnoe Vremya. The candidate of technical sciences specialises in the topic of bitumen materials, he has applied experience and knowledge to most of the formulations of those brands that are produced by the plant today. And more than a dozen of them are produced in industrial volumes.
The secret of product quality and the acquisition by each brand of its own special properties required for certain operating conditions lies in the details: the composition of tar, mixing proportions, oxidation period, pressure and temperature, as well as the residence time of mixture in special conditions for each brand of bitumen.
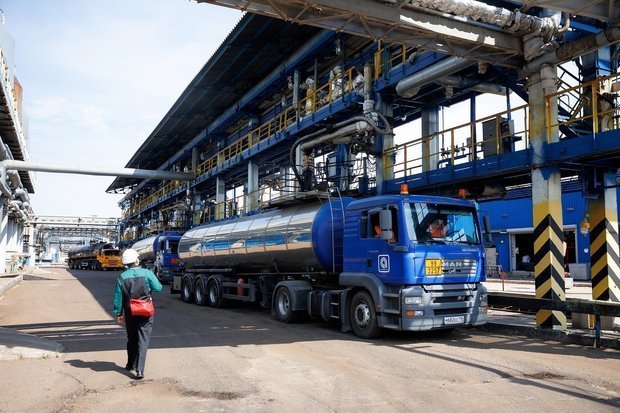
The finished product is not delayed on the territory of the enterprise: the shipment of bitumen is carried out through a loading rack to road and rail transport.
“Almost the entire volume of sales of bitumen produced by us today is carried out on the domestic market. And the main sales market is the Republic of Tatarstan. Our key buyer companies are Alekseevskdorstroy and Tatavtodor. However, we sell our products not only to end-users. Any company can participate in organised auctions. This is either ONLINECONTRACT electronic platform, or SPB MTSB JSC — St. Petersburg International Commodity Exchange. In fact, our products are available to all customers," explained Askar Sulteev, the head of the Department for Commerce of TAIF-NK JSC.
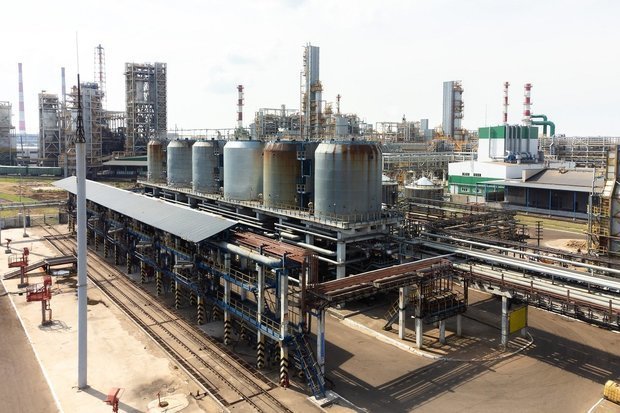
In 2015, another technology was introduced at the bitumen production of TAIF-NK Refinery: the production of PBB — polymer-bitumen binders — bitumen, in which a certain proportion of special polymers is introduced at certain temperatures, pressure, mixing. The mass brought to a homogeneous state acquires unique characteristics, primarily elastic deformation, that is, the ability to regain its original shape. What does it mean? The road itself gets rid of the formation of a track, successfully resists the cycles of transition through the "0", reduces the risk of cracks.
By the way, this product, as well as almost every one produced at TAIF-NK, is the winner of the quality competition.
Since 2007, the refinery has also produced fuel for RT jet engines and fuel for Jet A-1 gas turbine aircraft engines. In 2015, the refinery obtained all necessary permits for the start of commercial production of the new brand of fuel for jet aircraft engines TS-1, intended for civil aircraft.
Tatarstan gasoline: counting since 2005
Incredibly, but a fact: the very concept of “Tatarstan gasoline” appeared only in 2005 thanks to TAIF-NK and TAIF. Up to that moment, the republic, which has the richest reserves of oil raw materials and almost unlimited industrial capabilities, bought automobile fuel in other regions.
The market economy is not a bed of roses. It might seem the petrol production technology has been known for a long time. Moreover, there are many. However, when Group’s specialists started to learn the world’s best practices, licensors demanded such sums that not one but two or three enterprises could be erected with this money. In the end, it was decided to task Russian engineers to design a catalytic cracking petrol hydrotreatment unit as well as formulas and Normal 80, Regular 92, Premium 95 petrol brands, a reactor, reaction product fractionation and production condensate treatment technologies. The project started in 2003, the plant produced its first product in 2005.
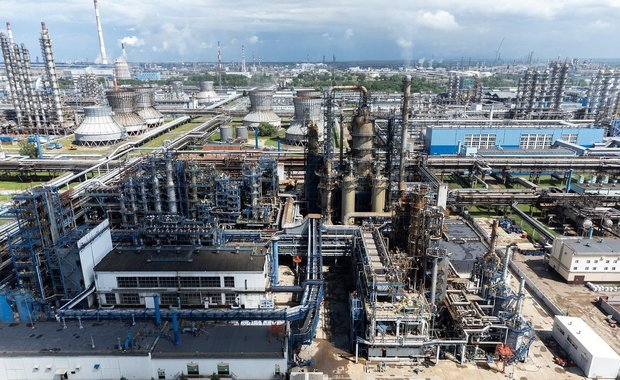
“It is unique production. Firstly, it is the only catalytic cracking unit built according to a Russian technology from a Russian designer in Russia and consequently in the world — the Russian Oil Refining Research and Development Institute. It was built in 2005, successfully launched and nowadays it operates to the full capacity producing petrol, liquefied gases, a wide range of motor fuel components, feedstock for diesel fuel production in the oil refinery,” notes chief engineer of TAIF-NK JSC Alexey Khramov.
The construction of the second Petrol Plant began in May 2005 almost without a pause — a unit refining gas condensate with a capacity of a million tonnes of feedstock. And the technology is also Russian. This plant manufactured the first product a bit more than a year later.
This was followed by a series of modernisation aimed to improve the quality of products that were made. In 2006, the factory produced Euro 2 petrol, the whole production line of Euro 4 was made in 2007, TAIF-NK’s Petrol Plant completely switched to the production of Euro 5 motor fuel in late 2015 ahead of time defined by federal requirements. Today over half a million tonnes of 92 and 95 petrol brands is produced.
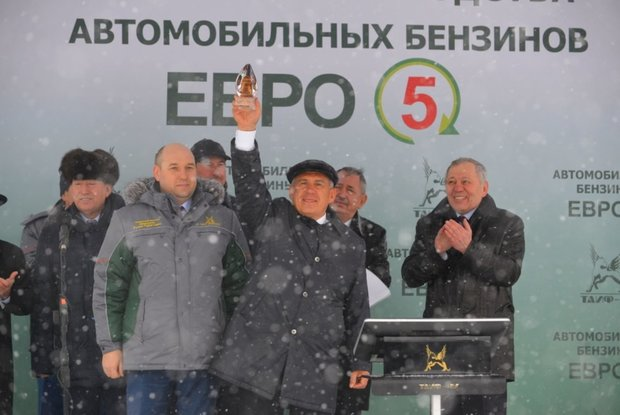
In January 2009, a milestone took place in the first plant of Petrol Plant. TAIF-NK set up its own production of high-octane petrol blending agents — up to 24,800 tonnes of methyl tert-butyl ether from isobutylene and up to 152,800 tonnes of tert-amyl methyl ether from isoamylene allowing enhancing operational characteristics of motor fuels.
Products of Petrol Plant of TAIF-NK JSC has been repeatedly recognised the best. Numerous diplomas of republican and federal quality contests are evidence of this. The largest-scale product — motor fuels — have received a considerable part of the awards. The staff and management of TAIF-NK are rightly proud of the accomplishments, and the whole gallery of awards is available on the company’s website.
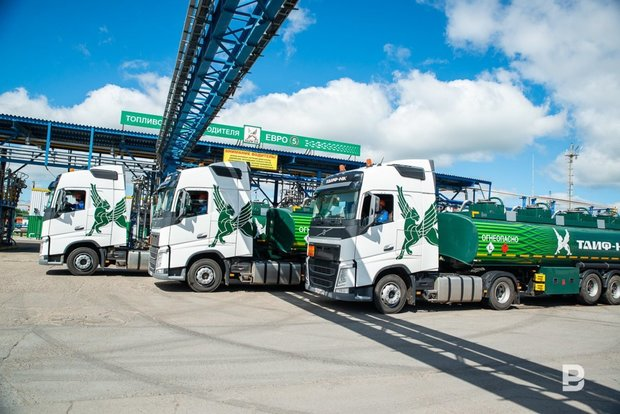
As Director of Petrol Plant Ilsur Samigullin admitted in one of his interviews with Realnoe Vremya, he himself is a fan of their products. And as an experienced driver has his own reasons for this:
“Perhaps, many car owners paid attention to inscriptions on 92 and 95 petrol filling stations at other producers’ petrol stations: “the fuel contains additives to remove coke in the engine.” Our petrol doesn’t need this to be done because it doesn’t develop coke. This is the benefit: a long-term use of TAIF-NK’s petrol expands the lifespan of the car in general. A car using other petrol for 5-10 years will anyway need expensive maintenance. Our petrol doesn’t require it. I use our petrol myself. It is always necessary to look several steps ahead.”
Summer diesel fraction, straight-run petrol, propane propylene fraction, butane butylenes fraction, dry gas, jet kerosene, mazut are among other products that are already manufactured in Petrol Plant. The company shared its plans for the foreseeable future too. Particularly, about the start of mass production of branded motor fuels.
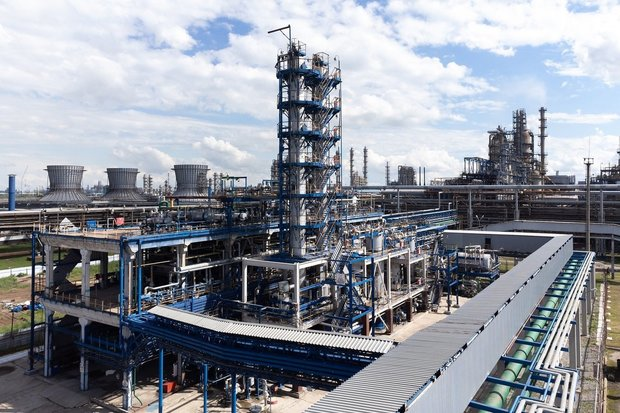
“We considered several options of branded additives and did research in the R&D Centre on the impact of these additives to motor fuel. The additive that we chose significantly improves characteristics of our petrol — fuel consumption decreases by some 7%, engine KPI improves, exhaust smoking goes down, in other words, eco-friendly characteristics get better. We expect the product to be in demand,” chief technologist of TAIF-NK JSC Alexey Taymanov told Realnoe Vremya in an interview.
Made in HRCCF
The launch of the Heavy Residues High Conversion Facility (3.6 million tonnes of tar and vacuum gas oil a year) according to VVC technologies expanded the company’s possibilities.
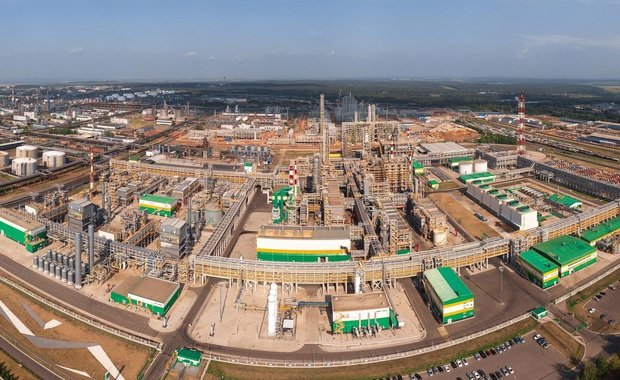
“The process of combined thermal and hydro tar cracking (VVC, or Veba Combi Cracking) at the HRCCF is the summit of technological development of the highest oil refining processes in the world,” chief engineer of TAIF-NK JSC Alexey Khramov is convinced. “This process combines all technical solutions existing in oil processing nowadays: primary processing, thermal cracking and slow cocking, catalytic cracking in fluidised bed, hydrocracking. At the first stage, tar is processed in slurry reactors at a temperature of over 450°C and up to 200 atmosphere of hydrogen pressure. A specialised additive — activated lignite — is used for the absorption of metals and coking feedstock components, while the process itself takes place in a slurry, constantly moving environment. Tar conversion into light, quality and finished oil production is over 90%, and it is a unique result. Then products of slurry reactors are separated from coal additive that absorbed metals and predecessors of coke, which are catalytic poisons, in licensed separators. Products of the reactions are mixed with heated vacuum gas oil and go to the second stage of classic hydrocracking with its fixed-bed catalysts. As a result, we get over 95% conversion,” Alexey Khramov told the journalist.
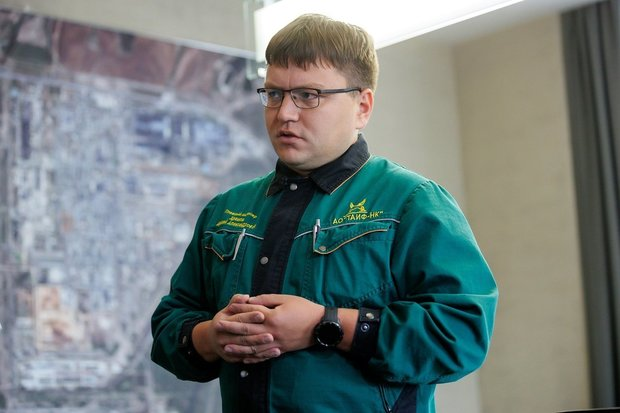
Another unique fact is that not only diesel fuel, naphtha and jet fuel but also products with special operational features are made from unprofitable highly sulphurous products such as tar and vacuum gas oil. This permitted the company to master the production of Euro 6 diesel fuel. Naphtha has its own peculiarities too, notes Alexey Khramov.
“The naphtha we produce in the facility is a bit different, and I think it is for the good, because of the quality of straight-run petrol. Firstly, it is highly hydrotreated naphtha, its sulphur contest is 5ppm, and it has interesting moments precisely regarding the composition of hydrocarbons and as soon as we increase the conversion of tar, we see that the group composition of the facility’s naphtha changes in favour of those components, those groups of hydrocarbons chemists consider more sought-after.”
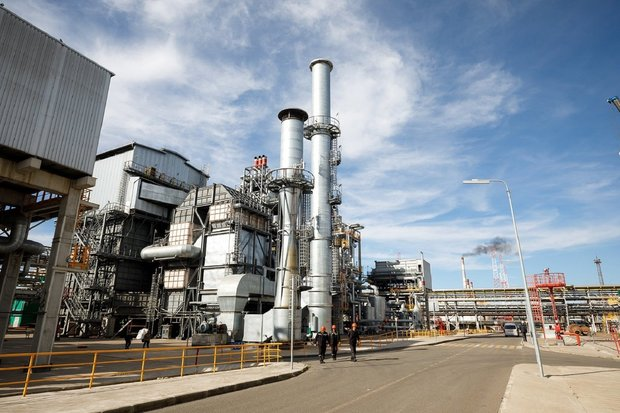
It is planned to set up the production of heavy residues of heavy residues, that’s to say, what is left after the feedstock goes through the HRCCF, in fact, with full recovery of light petrochemicals. It is the start of production of two new products each of which has already interested Russian metallurgists. We will tell you about what exactly, when and how much is going to be produced in one of our next reports.
Подписывайтесь на телеграм-канал, группу «ВКонтакте» и страницу в «Одноклассниках» «Реального времени». Ежедневные видео на Rutube и «Дзене».