From ‘Second Baku’ to the present: history of Tatarstan oil refining
No oil production — no oil refining, no oil refining — no petrochemistry: when, why and how did the efficient chain started to be built in the republic?
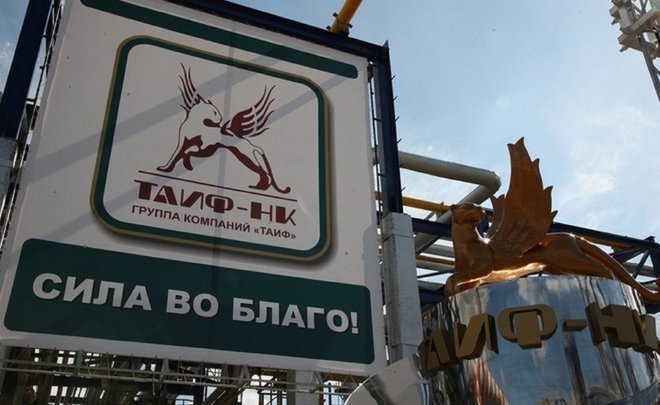
Oil in itself isn’t a bad commodity. It isn’t called black gold accidentally. But the well-being of the republic doesn’t rest only on oil. And Tatarstan President Rustam Minnikhanov has repeatedly stressed that the economic potential of the region is in high mineral conversion rate. But this is today. While less than half a century ago, the republic was just a source of raw hydrocarbon. How has everything changed? Realnoe Vremya starts a series of articles about the history of creation and development stages of oil refining in Tatarstan. The first part is dedicated to the heart of TAIF-NK JSC — the oil refinery.
300-years-old Tatarstan oil
The confidence in the presence of oil on the territory of modern-day Tatarstan comes from the middle of the 17th century.
There survived records of the Artillery Chancery as of 1637 about the discovery of oil seepages. Vedomosti newspaper wrote about the discovery of oil near Kazan in the first edition in the early 18th century, there were mentions later as well.
However, oil production obtained a large scale only in the 1940s. The first oil wells were drilled during the Great Patriotic War, and the era of “Second Baku” started, its scale and production capacity outperformed the first one soon.
But producing up to a hundred and over millions of tonnes a year (the republic reached this level in the mid-1970s), Tatarstan remained just rich and seemingly inexhaustible feedstock source for a long time.
Setting up some oil refining started to be voiced only by the late 1970s when the primary oil refining plant (ELOU AVT-7) was launched at the Nizhnekamsk Petrochemical Plant (today’s Nizhnekamskneftekhim PJSC). The supply of straight-run gasoline was the main task of the new plant. It was necessary for key NKNK plants as feedstock. Was this enough not only for Tatarstan but also the country in general? No, it wasn’t. But the republic had to wait for almost another 20 years until the next step was taken to have its own oil refinery.
During the toughest times
TAIF was the founder of today’s oil refining giant that is in the country’s top 10 leading enterprises of the sector. The investment company, which recently grew from Kazan Research and Production Association, started to recover and develop Tatarstan’s petrochemical complex according to the republican administration’s instructions. The creation of its own large-scale oil refining was to be one of the first and crucial steps on this road.
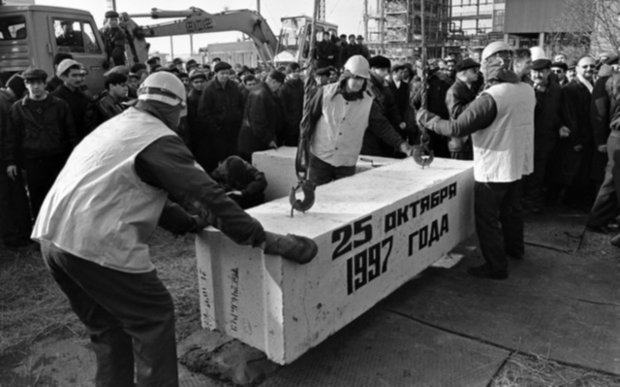
The ELOU-AVT-7 unit TAIF rented from NKNK in 1997 by creating a new legal entity TAIF-NK became the foundation and the heart of the future complex, so to speak. The unit that could process about 6 million tonnes of oil a year, was worn out by 1999. Also, it hardly operated at a half capacity: the load was about 2,5 million tonnes of feedstock a year. One would feel awkward to talk about the conversion rate today: the production of light oil products didn’t exceed 35%.
The new company began to upgrade the equipment almost immediately. And this happened despite the extremely complicated economic situation in the country, amid a global crisis that took Brent down to $16-20 per barrel. In 1998, TAIF-NK reached the installed capacity.
Different from others
Having different formats is one of the key difference of TAIF-NK from a variety of other oil refineries both in Russia and around the world. If others focus only on feedstock for petrochemistry or on motor fuel exclusively, TAIF-NK successfully realises its potential in both areas, while the general range of products includes more than 50 names today. But we will tell you about what is produced now and its amount in one of the next articles.
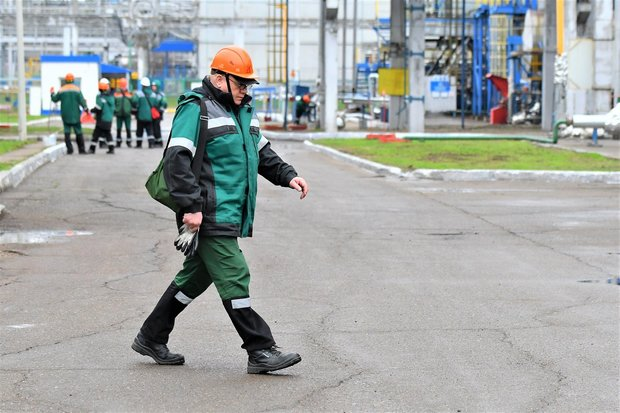
The feedstock used in production is the second difference.
“Few enterprises refine heavy high-sulphur oil not only in Russia but also in Europe. It is both difficult and costly to refine such oil — with 1,8% sulphur content of the general weight, with higher density and considerable content of heavy components, including metals. The load on the equipment is much higher than in the conversion of light oil brands,” Director General of TAIF-NK JSC Maxim Novikov explained to Realnoe Vremya’s journalist.
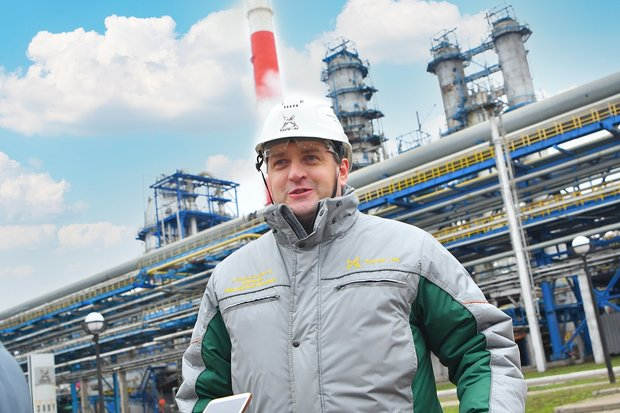
The company started to develop and expand its own capabilities from the first day. At first, everything was built to provide feedstock Ethylene 450 Plant (later Ethylene 600) with straight-run gasoline. Mazut is the residual product that was used as fuel for the heat power plant. The management decided to create a full-cycle oil refinery. Engineers had to work hard so that the unit had a complex of new plants: middle distillate hydrotreatment, tar visbreaking unit, a bitumen unit was built at the same time, commodity and feedstock tanks expanded. A huge job was done to make a huge factory with the current assortment from one shop.
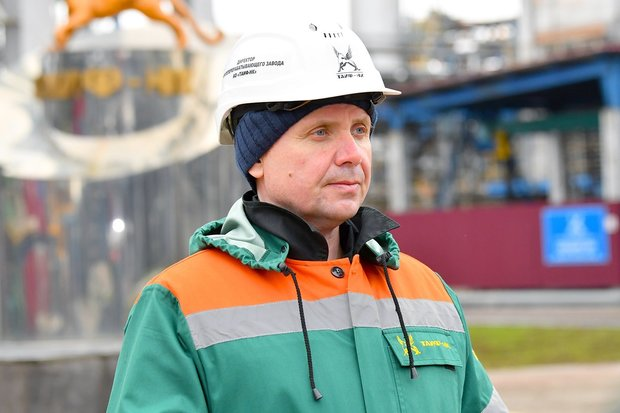
Maxim Novikov also believes that the aspiration for the best result is almost an endless process.
“As far as I remember, we have been building something all our life, we have been achieving some results: we have either increased the productivity or expanded the range of products. Of course, the product assortment has always been high-quality. There have been a lot of stages, but we have always kept up with the times, like now,” he shared.
Not to stop moving
This is one of the key slogans of TAIF Group of Companies, all the huge staff of TAIF-NK and its heart — the oil refinery.
In 20005 (by this time, the oil conversion rate already reached 63% against 35% in the 1990s), TAIF compensated NKNK and Tatneft for their share of costs during the construction of the complex of medium distillates, the visbreaking unit, non-oxidised road bitumen unit, jet fuel preparation and storage unit and sulphur recovery unit and its storage room. The total independence from its previous partners cost the oil refinery $400 million.
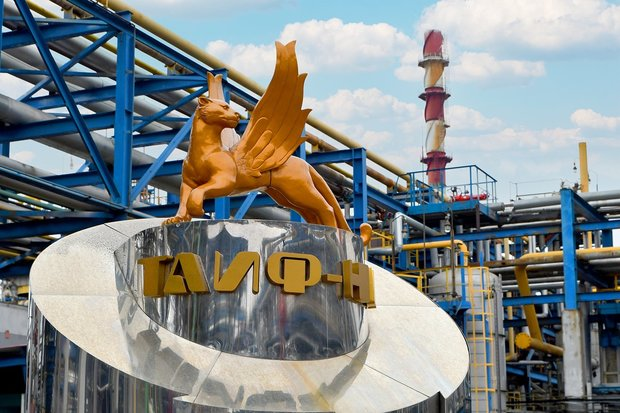
A huge sum, which is the equivalent of the construction of a new modern factory, fell on the company’s shoulders but didn’t stop and even didn’t interrupt its development. Petrol Plant and the world’s only catalytic cracking unit built according to a Russian technology were put into operation in 2005. In 2006, a gas condensate refining unit, which was scheduled in 2003, reached the installed capacity. This is another million tonnes of refined feedstock a year. In 2010, the medium distillate hydrotreatment unit was modernised and expanded its capacity by a third compared to the installed capacity. By 2015, the total feedstock refining capacity of TAIF-NK totalled 8,4 million tonnes a year, moreover, over 7 million tonnes was the load of the oil refinery with Tatarstan’s heavy high-sulphur oil.
TAIF-NK oil refinery today is a real city with quarters and microdistricts linked with one network and goal. The oil refinery is the first historical production shop that is based on the same but seriously upgraded and modernised unit ELOU AVT-7. Nowadays its capacity isn’t 6 but 7,344 million tonnes of crude oil.
Shop No. 2 is designed for tar cracking, which comes from the ELOU. 1,8 million tonnes of feedstock is received and refined here annually. Bitumen is the target product of the next plant. We will tell you about it in one of the next reports, but it is worthy of mentioning that not only Tatarstan but also almost any part of the country is familiar with it: road, construction, roofing bitumen, it modestly and invisibly makes everybody’s life more comfortable and better. Polymer-bitumen binders are prepared here too — they are irreplaceable in road and highway construction.
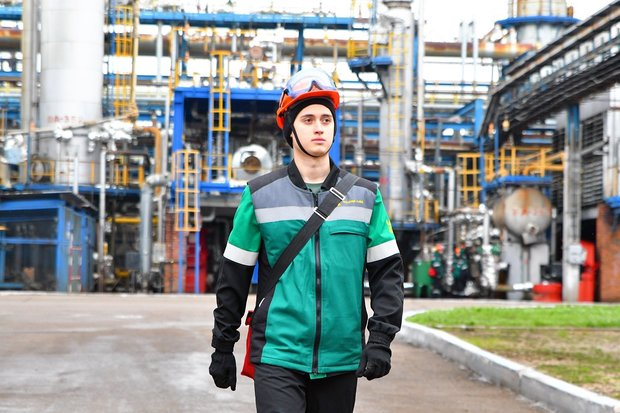
The medium distillate hydrotreatment complex is the second plant. Diesel and jet fuels are made here. The main capacities were put into operation as early as 2002, but they have been repeatedly reconstructed and modernised to stay up-to-date. Euro 5 diesel fuel TAIF-NK oil refinery was first to mass produce in Russia is direct evidence of this. The paradox is that diesel with the lowest possible sulphur content is made of oil in which sulphur content is above all the norms. By the way, the oil refinery’s Shop No. 5 recovers sulphur and turns it into a valuable product that is in very high demand from agriculturists.
Finally, the third plant. Storage, packaging and shipping to consumers takes place here. And the local industrial sewage treatment shop refers to this plant too. TAIF-NK became one of the first in the sector to create a completely closed water circuit.
“It is noteworthy that our treatment facilities have treated about 10 million cubic metres of water and returned it to the processes in the last six years. In other words, we don’t take water from the Kama River anymore but use the existing in a closed cycle,” Maxim Novikov stressed with pride.
Economy and environment
As Maxim Novikov –TAIF-NK director general — highlights: nowadays it is impossible to divide and separately consider the measures taken to enhance the efficacy of processes, increase production volumes and boost the economic effect. All these are links of one chain. The relatively recent improvement on the tar hydrocracking site is one of the bright examples of this.
“A lot of hydrogen-rich gases are emitted in one of the processes. Not to lose the valuable feedstock and reduce the environmental impact, the company purchased and assembled a small unit with carefully picked molecular sieves. It allows recovering hydrogen from process gases and returning them to the cycle. The productivity of such a unit is about 12,600 tonnes of hydrogen a year, which is comparable with the current hydrogen unit in the oil refinery. Moreover, the process doesn’t require any costs on either electrical energy or natural gas, emissions into the atmosphere have notable reduced too,” said Maxim Novikov.
The new life for phenol containing sewage is another example. It is generated during vacuum gasoil catalytic cracking.
“They used to be sent to the common treatment facilities, now, according to a recommendation of a design institute, we return it for to wash salt out in primary oil refining. Consequently, all phenol remains in the cycle and goes with hydrocarbons,” said the director general of the company.
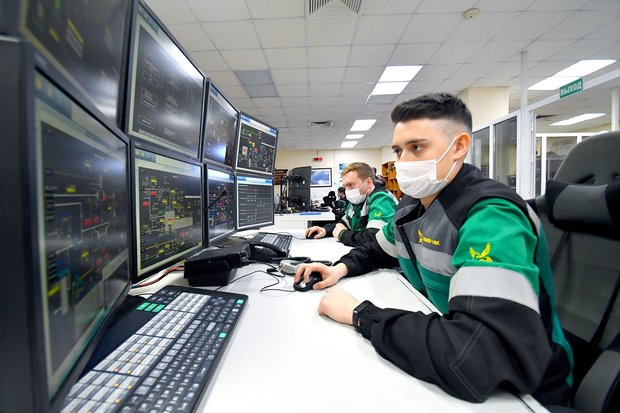
A lot of improvements of this kind have been made in the company’s activity over the years. And the launch of a heavy residues high conversion complex became one of such bright moments. What used to be considered a by product, in fact unprofitable and hardly main production residues, became a valuable feedstock to make high-quality products. The production of light oil products, according to the technology, will exceed 95% and take the crude oil conversion rate to unseen heights. And what is more important, Russia, Tatarstan, TAIF-NK became the first to do this proving sceptics that the impossible is possible if there is a goal, a clear plan and have the world’s most valuable resource — creative, skilful staff that truly loves the job. But we will tell you who these people are, how they prepare substitution for them, what heights they have achieved, what goals they set for the near and remote future in the next parts of our cycle.
Подписывайтесь на телеграм-канал, группу «ВКонтакте» и страницу в «Одноклассниках» «Реального времени». Ежедневные видео на Rutube и «Дзене».