Maxim Novikov on tar residue production: ‘We tested many options, but...’
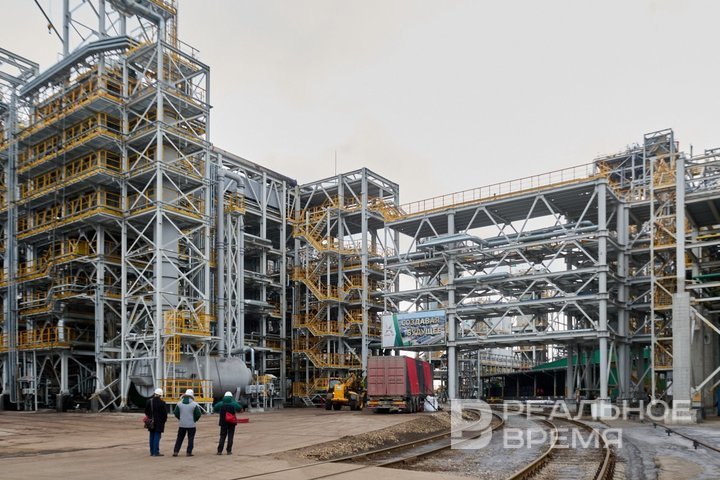
The director general and specialists of TAIF-NK JSC explained how they came up with the idea to produce a special product for metallurgists instead of road bitumen, about how it turned out that the necessary technology was not available in the global industry and they had to take scientific and applied research into their own hands and also about whether there is a limit to perfection and the depth of oil refining. Read more about it in the report of Realnoe Vremya from the new production of one of the most innovative oil refining complexes in the country.
“Creating the future”
Realnoe Vremya and Novy Vek TV channel journalists were greeted by a poster with the inscription “Creating the Future” against the background of a photo of the oil refining company's pride, the Heavy Oil Residues High Conversion Complex (HRHCC) on the supporting structures of a tar hydrocracking concentrated residue production unit. And here we were met by the company's CEO Maxim Novikov.
“Indeed, the HRHCC is the future. The future of all deep oil refining. Today, thanks to the new production facilities of TAIF-NK JSC, we have already achieved the selection of light oil products from each ton of raw materials — over 90%, and in some periods even 95% (editor's note: with this indicator, TAIF-NK JSC is the leader in Russia). But even after processing at the HRHCC, there is a small residue (most oil refineries have much more). This is an unprofitable, little-demanded, low-priced product, the so-called unconverted residue. We were faced with the task of turning this residue into a high-quality final product that is in demand by the market,” Maxim Novikov introduced the background of the issue.
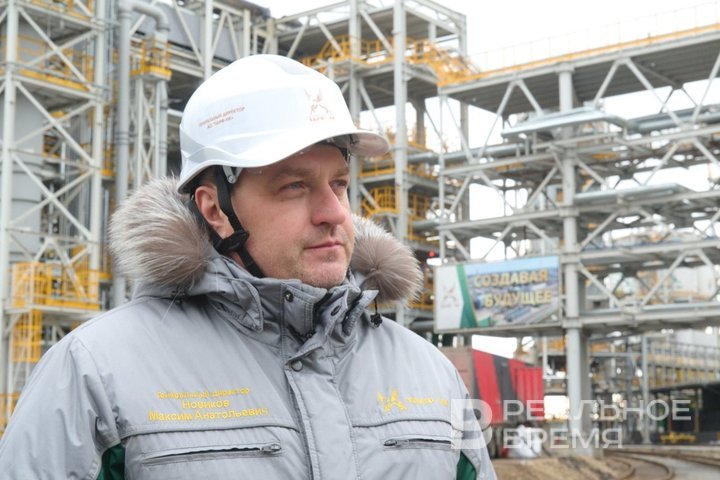
The complexity of the task was determined by the characteristics of this residue itself — a dark oil product, from which, during all stages of distillation — first in classic units, and then with the help of the HRCC, the maximum amount of light components were extracted and at the output was a quickly cooling and pasty mass — a mixture of asphaltenes with mechanical impurities and a small amount of high-molecular resins.
And here a problem arose, which Tatarstan oil refiners had to solve: the viscous substance tended to clog the pipelines, interfering with pumping, and stood in the tanks as a dense mass. Potential buyers were not in a hurry to buy it, and the prices were several times lower than the cost of the crude oil itself, plus transportation costs... This did not suit either the shareholders — TAIF Group of Companies, or TAIF-NK JSC itself.
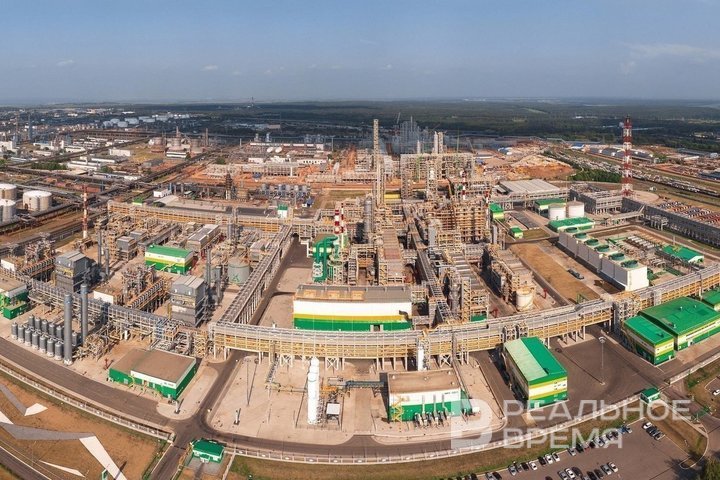
It could have been utilized, but... the issue of increasing the burden on the environment was acute, which the company, firmly on the path to improving environmental performance indicators, could not afford. In addition, this went against the policy of the most efficient use of raw materials — albeit quite heavy and high-sulphur Tatarstan oil. The task of increasing the depth of processing to 99%, and the extraction of light oil — up to 95% is considered quite realistic at the enterprise. Moreover, from the very beginning, the oil refining residues after the HRHCC were assigned the role of raw materials for the next stage of processing. The plans simply had to be slightly changed. To more efficient and profitable ones.
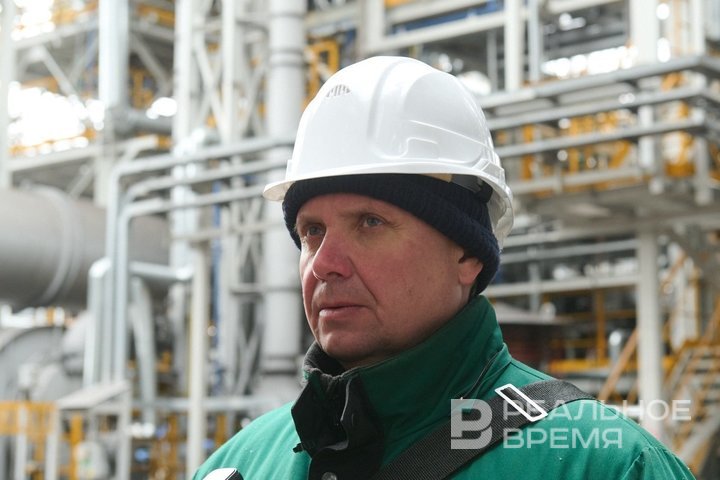
“In fact, even when planning the construction of the HRHCC, according to calculations, about 30 tons of residual products should have remained per hour. According to the HRHCC project, it was planned to produce bitumen from them. But life made adjustments: after the launch of the HRHCC and the complete debugging of the processes, it turned out that the residual product was not very suitable for the production of bitumen,” Director of the Oil Refinery Vladimir Lakhomov explained to journalists.
But properties were discovered that allow this residue to be processed into high-margin products that are much more in demand on the market. It remains to decide on the technology.
“Nobody could offer something that would suit us...”
The selection of the technology took quite a long time. At first, a working group of specialists from TAIF JSC and TAIF-NK JSC got acquainted with the available ready-made solutions.
“We tested many options. We went on business trips ourselves, brought here representatives of the Russian machine-building business, and delegates from foreign companies who wanted to present their potential. But, unfortunately, nobody could offer us something that would suit us. We had to take the processes into our own hands and rely only on ourselves,” said Maxim Novikov.
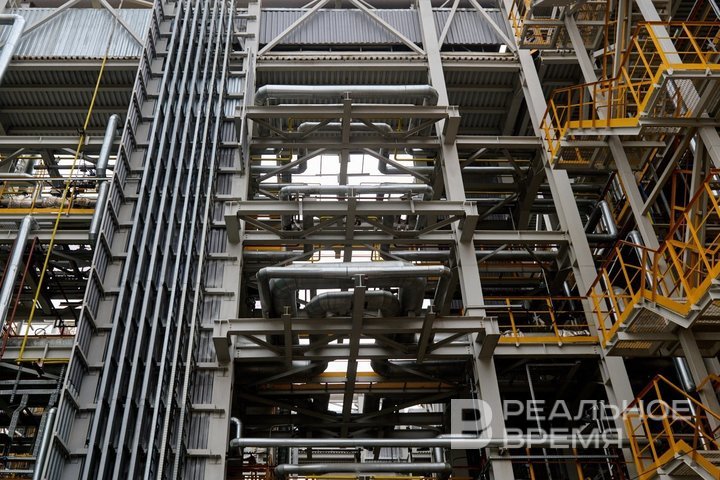
Having gone through all possible theoretical options and worked out possible solutions in the form of projects, TAIF-NK specialists began physical implementation. Not everything worked out on the first try.
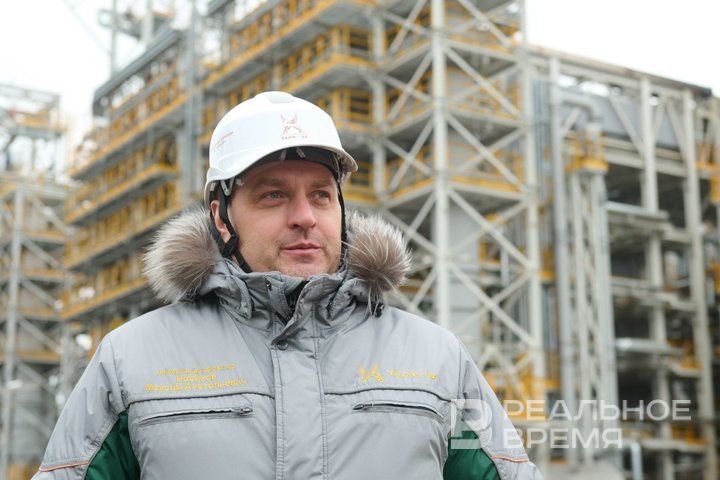
“We created our own project for deepening the processing of oil residue — the residual product of tar hydrocracking. We had to select the necessary processes empirically. It was not easy,” admits the director general of TAIF-NK JSC. “Many pilot units were installed for different processes: there were centrifuges, filtration, decanting... but there was no success. Our partners — Technokhim engineering centre and Aliter-Axi manufacturing enterprise — helped us curb the processes and implement the project.”
Go-ahead from the public
At the end of March 2023, public hearings on the implementation of a new oil refining project were launched in Nizhnekamsk. This is a mandatory requirement before the construction of an industrial facility.
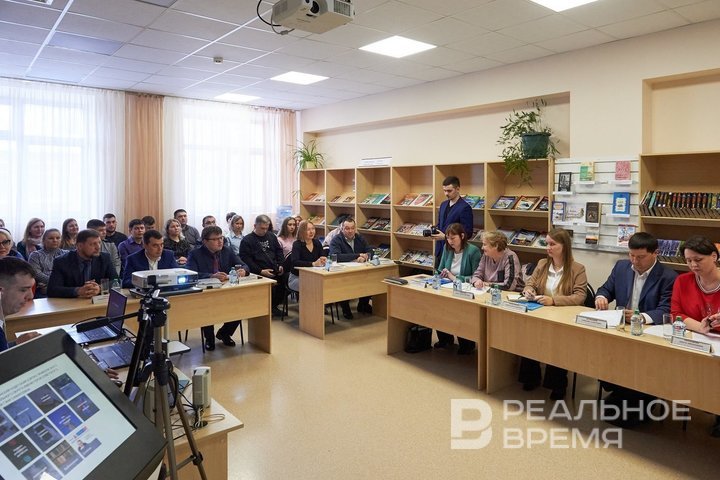
Three weeks before the final face-to-face discussion, with prior notice, materials on the results of the state environmental impact assessment of the facility on the environment were made publicly available on the websites of the municipal district, Russia’s environmental watchdog and the Ministry of Ecology and Natural Resources of the Republic of Tatarstan. On the day of the live discussion, more than 200 Nizhnekamsk residents applied for the public hearings online and offline.
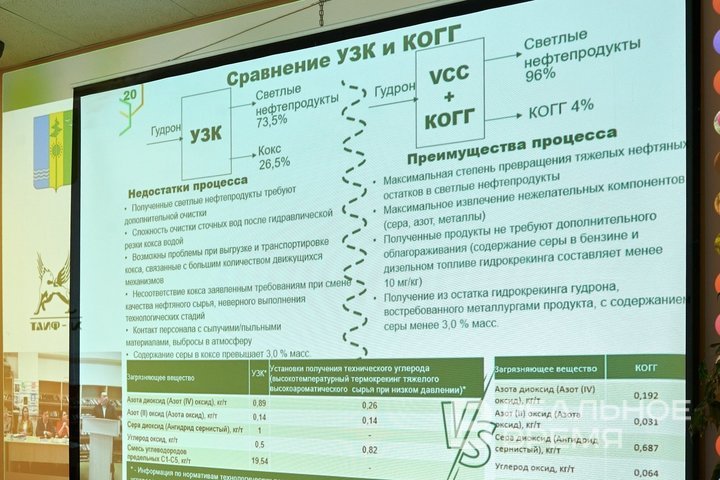
The information that the waste from the HRHCC, which without further deepening of processing, at best could become boiler fuel (fuel oil) — far from the most environmentally friendly, and at worst — would be subject to disposal, which would also not bring any benefit to nature, can be turned into useful and in-demand products was received favourably by those gathered. The participants received the report of deputy head of the Ecology Department of Pozhinzhenering Galina Kuznetsova who spoke about the results of the assessment of the impact of the project on the environment, even more favourably.
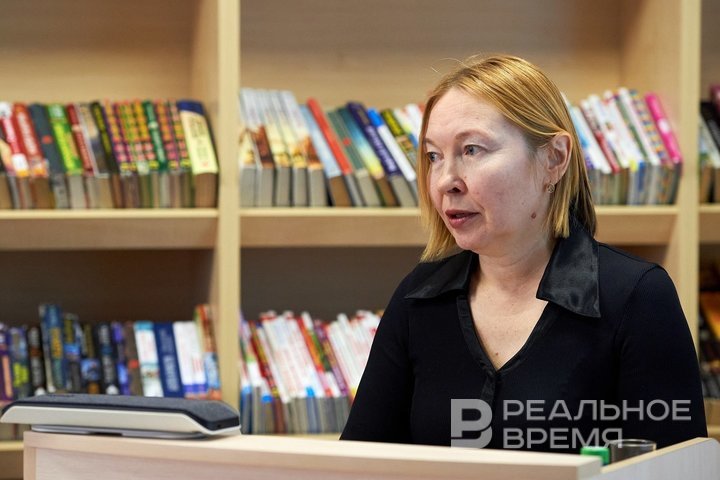
Considering that the efforts made by TAIF-NK JSC to improve the environmental friendliness of production had already significantly reduced the volume of environmental impact (which was already significantly below the upper limit of the MPC), the results of the EIA gave the green light to the project. The participants in the hearings confirmed the decision by unanimously supporting the construction.
“Just two years passed from the idea to receiving the EIA”
Already in September 2023 when a Realnoe Vremya journalist first found himself at the construction site of the new facility, it was clear that TAIF-NK was not wasting time: metal structures were reaching towards the sky, the facility was gradually being filled with production equipment.
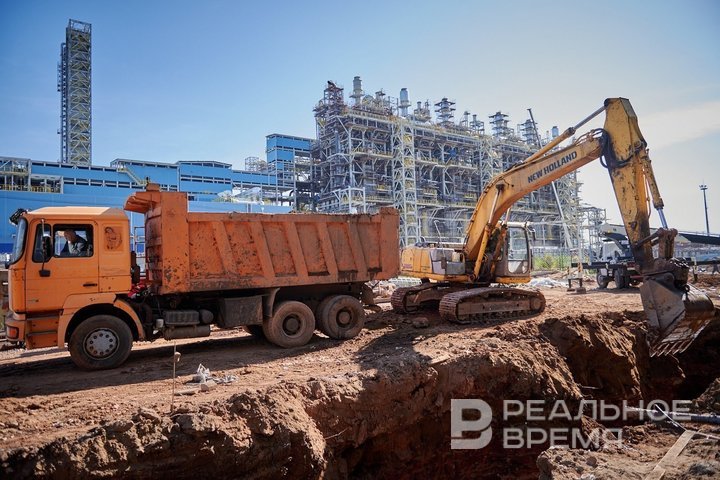
“About 95% of all technological equipment is domestically produced. The contractors are also local,” explained head of the Technical Re-equipment and Prospective Development Department of TAIF-NK JSC Niyaz Khamidullin at the site.
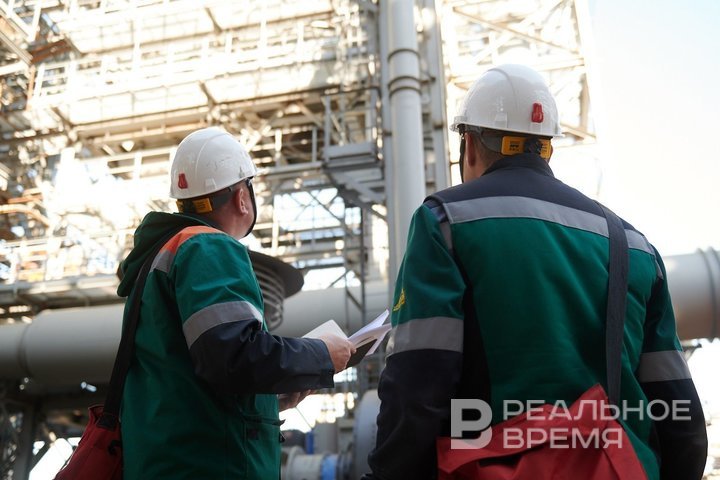
“It was decided to use a unique method of thin-film evaporation in a mechanical high-temperature vacuum reactor. Its distinctive properties are that the distillation of raw materials is carried out in a thin film, which is created by the rotation of a special rotor inside the reactor. Due to the use of vacuum, the temperature in the device is relatively low, which eliminates the process of coking of the raw materials inside the reactor. Such devices with such hardware design exist in the world, but they are designed to process more stable raw materials and have never been used anywhere before in this configuration on a plant scale. Moreover, given the specifics of the oil residue after processing at the HRHCC, our unit was significantly modified by TAIF-NK specialists. In other words, our unit is unique for the oil refining industry not only in the Russian Federation, but also in the world,” explained Niyaz Khamidullin.

“Considering that processing at TAIF-NK amounts to millions of tonnes of crude oil, the productivity of this unit may seem insignificant. But with the delivery of this unit, the last problem associated with the phase instability of the unconverted residue of tar hydrocracking will be solved. That is, this will be the final step that will lead to the stable operation of the entire enterprise as a whole,” chief technologist of TAIF-NK JSC Alexey Taimanov emphasized in an interview with Realnoe Vremya then, in March 2023.
Already in the second half of 2024, in the commissioning mode, the unit produced its first products — vacuum gas oil and concentrated residue of tar hydrocracking. The construction of the facility was completed even ahead of schedule.
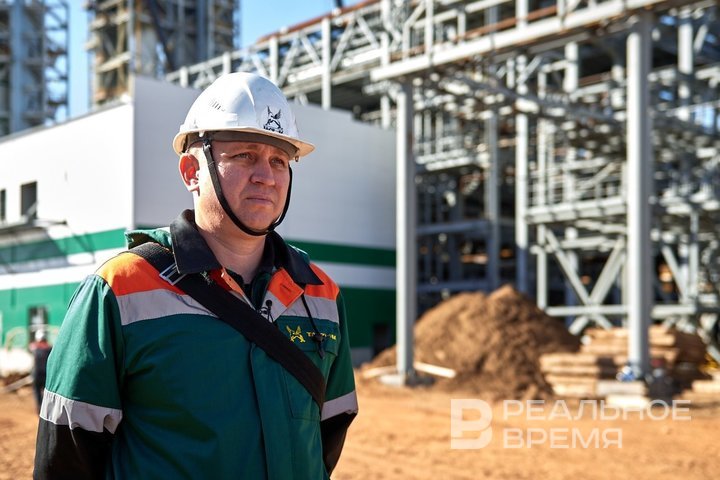
“The team worked very harmoniously in conjunction with our shareholder — TAIF JSC. All the dots were correctly placed, the designer and supplier of the main equipment were selected. Everyone worked smoothly. From the idea to receiving the certificate of conformity, only two years passed. No comments. Everything works,” Maxim Novikov emphasized during this meeting in March 2025.
“It turns out that we got two birds with one stone”
Compared to the main production facilities of the oil refining company, the size of the new unit is modest. But the effect from it both for the company and for the industry as a whole is impressive.
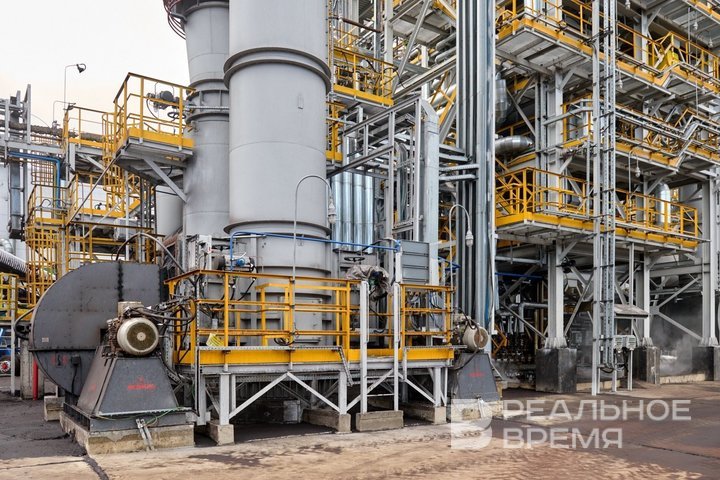
“The unit is not very large. The design feedstock load is 240,000 tonnes a year. The output is from 100 to 120,000 tonnes of hydrocracked tar concentrated residue, and the rest is vacuum gas oil. According to the technology: everything that evaporates in a vacuum environment is vacuum gas oil. Due to the vacuum, it rises up, condenses and is sent through pipelines to tanks for processing into motor gasoline. And the denser substance in liquid form is lowered onto the pumps and fed to the conveyor belt, where it cools down to 50 degrees with the help of water cooling, becomes dense and is crushed by a crusher into a commercial fraction of residue,” Vladimir Lakhomov explained to journalists. The oil refinery is the new unit is part of its production.
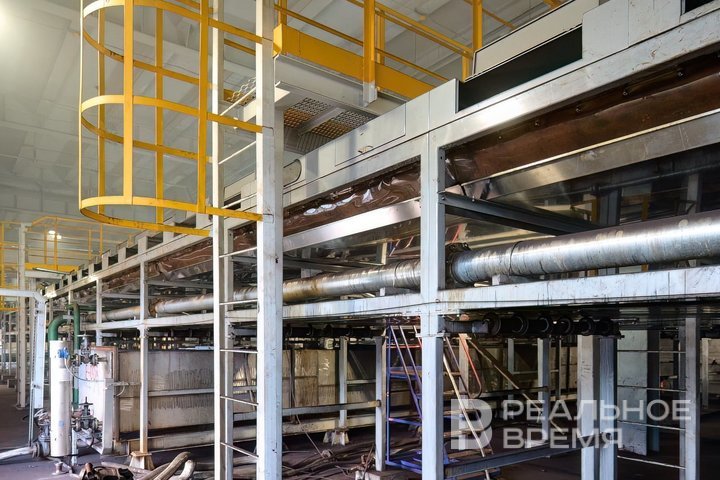
In total, the unit consists of three reactors. They receive and process 30 tons of raw materials per hour. The residue is literally loaded from the belt into freight transport and sent to form railway trains, which metallurgists are eagerly awaiting. Part of the residue is shipped in liquid form into special railway tanks. For this purpose, a special loading rack was built at TAIF-NK.
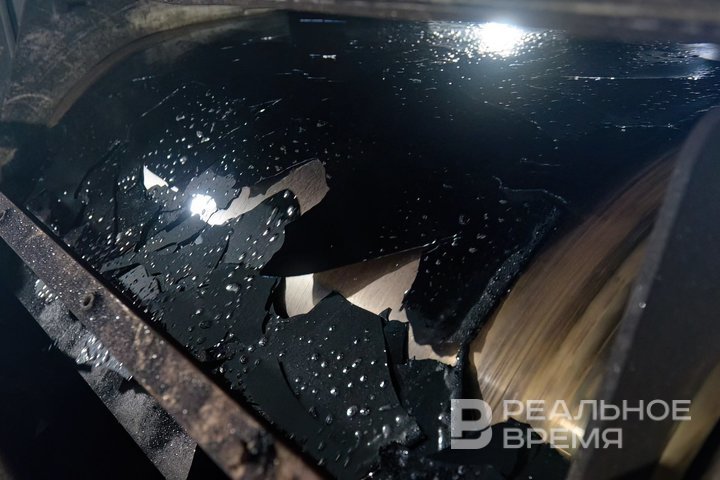
“Metallurgists are intensively searching for a replacement for coal tar pitch, which is obtained in coke-chemical and metallurgical industries. Due to the fact that many industries are aimed at increasing efficiency, the consumption of coal has begun to decrease, which is why the production of coal tar pitch is falling. In addition, this coal tar pitch is rich in benzopyrene, which has a negative impact on the environment. Thus, our residue production unit allowed itself to catch two birds with one stone, both for TAIF-NK and for metallurgical companies that use pitch as a binder for the production of anode and pin anode masses,” the director of the Oil Refinery explained with a smile during a tour for media representatives.
There is another important effect — environmental
During the public hearings, it was said that the new production will not greatly increase the burden on the environment. In the end, the result even exceeded expectations. This was told to journalists by the chief specialist, head of the Environmental Protection Department of TAIF-NK JSC Ruslan Valiyev.
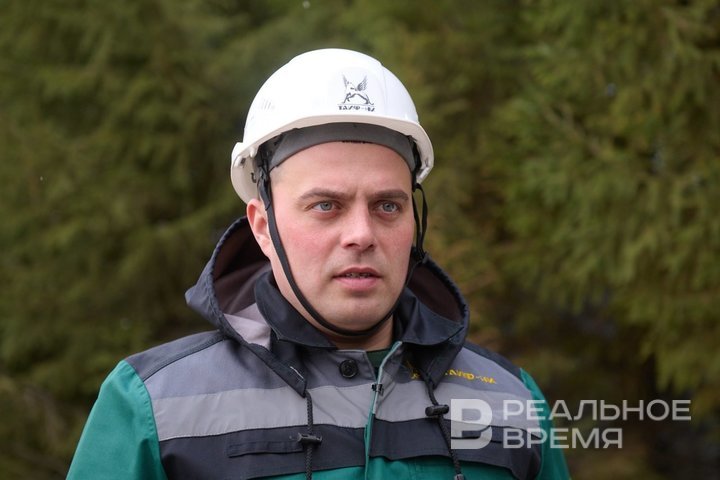
“From the environmental point of view, we can probably talk about this project for hours. In addition to the fact that with the launch of the residue production unit, the total volume of waste generation is reduced by more than 75%, our unit meets all the best technologies available today. We compared it with a classic delayed coking unit for the production of technical carbon: compared to these processes, the residue production unit is an order of magnitude more efficient. We have achieved very high indicators for the depth of processing of crude oil and, more importantly, the extraction of light oil products. The volume of dark oil products has been reduced to minimum values. And it is precisely such products that harm the environment. I am sure that from an environmental point of view, this is a real breakthrough,” the expert said, not hiding his emotions.
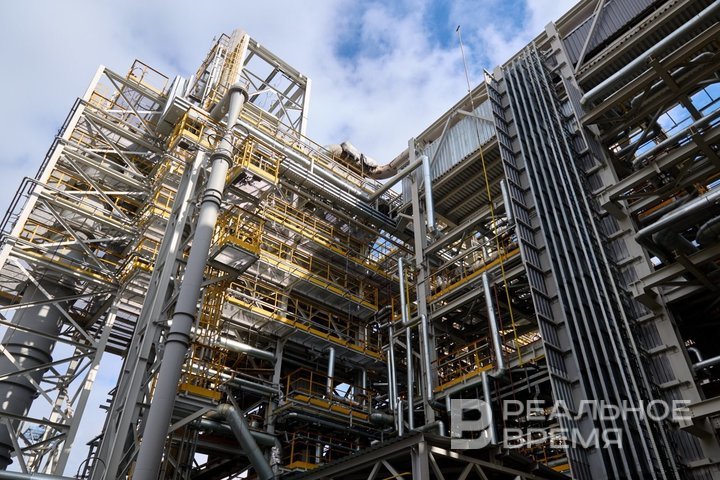
But this is not the whole effect.
“Here we squeeze out the lightest oil products and we get a very environmentally friendly product for metallurgists. If we compare our residue production unit with coal tar pitch: when using residue as a binder for the anode mass in aluminium production, benzopyrene emissions are ten or more times lower. And this is a strong carcinogen. In other words, in the regions where metallurgical facilities are located that use residue instead of conventional pitch, emissions of harmful substances will be several times lower,” Ruslan Valiyev continued to talk about the achievements of the new production from an environmental point of view.
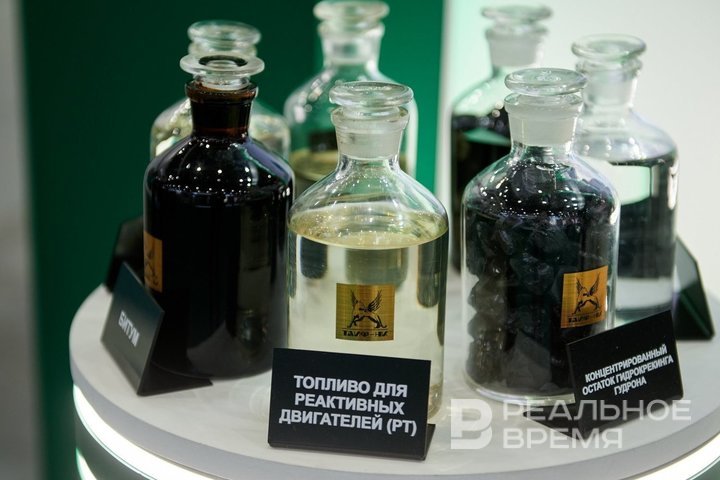
“In addition, due to the fact that after the processes at the HRHCC, most of the sulphur has already been extracted, the content of this substance at the input to the raw material is several times less than in other products with similar tasks. Here the sulphur content is 2.5-2.8%, which is much less than in alternative products. These are very important environmental issues,” Maxim Novikov added to his subordinate.
Plus the economy
Business must be profitable — this is the law of economics. More profit — higher wages for employees, more tax deductions, more opportunities to improve the standard and quality of life of the population, as well as to further improve production.
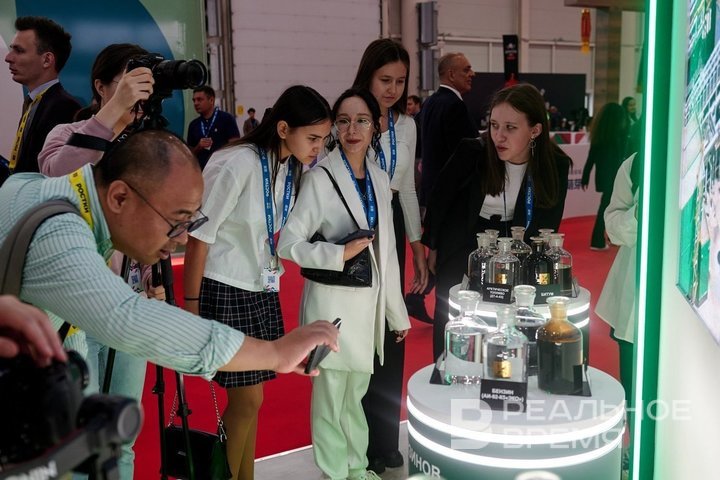
TAIF-NK has learned to process a low-margin product into valuable raw materials and a sought-after product that has already received high praise from metallurgists and does not linger in production. Shipments are ongoing. And this is profit.
But that's not all. Unique technological developments are the product of the intellectual activity of specialists from the Tatarstan oil refinery.
“We have filed an application with Rospatent for the product itself — residue, and, of course, for the equipment on which it is produced, and for the technology as a whole. All necessary examinations have already been passed, and at present we have received patents,” the director general of TAIF-NK JSC noted in an interview with journalists.
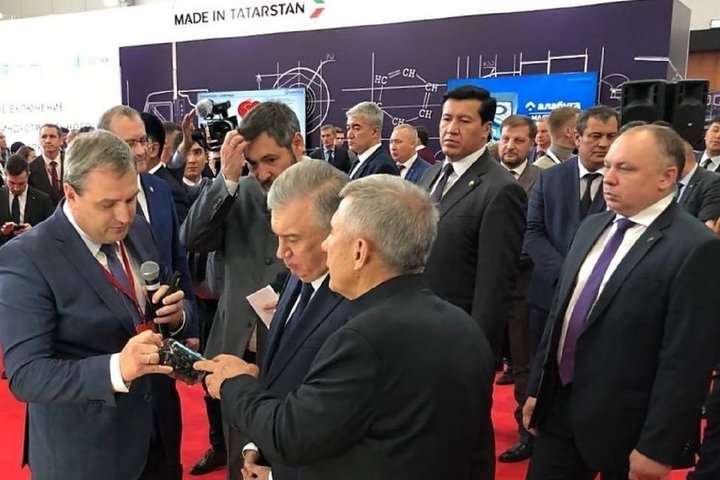
Such effective solutions should not lie idle — the company is confident. Here we are ready to share our developments.
“TAIF Group of Companies and TAIF-NK are always open to dialogue for joint development and improvement of the quality characteristics of petroleum products. Why not? But on the terms of mutually beneficial cooperation. We have announced our technology at the Russian level as well — at specialized forums, we tell you openly what we have achieved, we also show our results abroad. Naturally, companies are showing increased interest, they come to us, get acquainted with the production. Representatives of many companies have already been here. Negotiations are underway. Everyone is weighing the pros and cons. Naturally, many are accustomed to working according to processes that have been debugged since the last century, and they look at our successes with some caution. But it’s okay — this is a temporary phenomenon,” Maxim Novikov is sure.
“Is there a limit to perfection? Of course not!”
It would seem that the upper limit has been practically reached and there is nowhere else to develop in modern oil refining. But not in the TAIF Group of Companies. This was confirmed by the director general of TAIF-NK JSC.
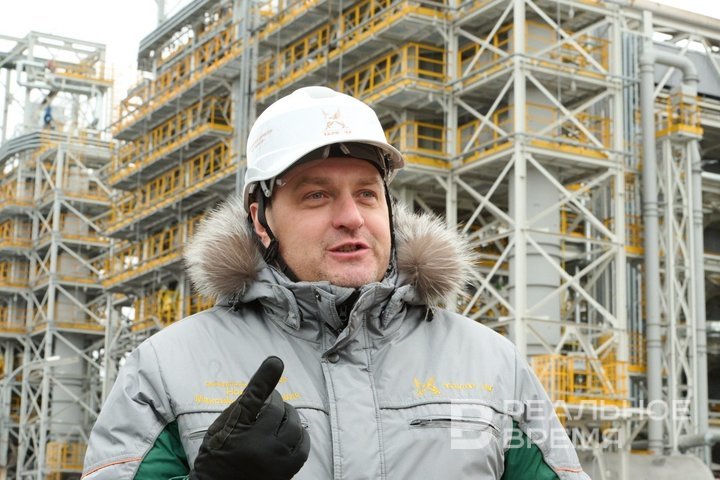
“There is another product that can be obtained. And with even greater added value. Moreover, even a pilot plant is ready and samples have been received. Now we are considering the possibilities of implementing the technology on an industrial scale,” Maxim Novikov admitted in response to the question, “Has the company already achieved all the peaks of modern oil refining?” And he added: “Is there a limit to perfection? Of course not! The more you immerse yourself in production processes, you learn what the world needs, especially when there are people with ideas on the team, there will always be forward movement.”
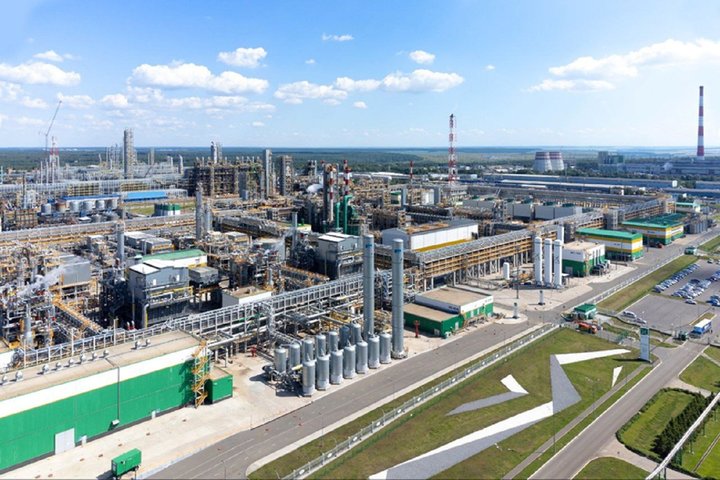
When asked to lift the veil of secrecy over the new direction in which work is currently in full swing, he answered as follows:
«All I can say now is that we are talking about the spent coal additive used in the processes at the HRHCC. Until recently, it was considered a kind of illiquid product. Based on it, we have received a new product that promises to be in great demand on the market and have greater profitability for us. But... While the project is being developed, we will refrain from laying all the cards on the table. Let the concrete results speak for us, as always.
Now TAIF-NK JSC is preparing to worthily present its successes and developments at the Tatarstan Energy Forum. Which will take place in early April at the Kazan Expo International Exhibition Centre. The products of the new plant will also be presented there.”
Подписывайтесь на телеграм-канал, группу «ВКонтакте» и страницу в «Одноклассниках» «Реального времени». Ежедневные видео на Rutube, «Дзене» и Youtube.