Shutdown maintenance at TAIF-NK nearing completion
In 2023, the number of contractors involved and the scale of work within the framework of major repairs has exceeded last year's scope
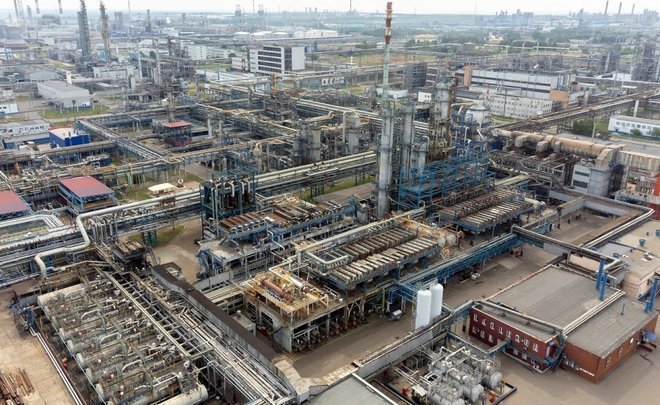
Three weeks for everything: from the complete shutdown of all production facilities of one of the largest oil refining complexes in Russia to the completion of almost all planned repairs, replacement and modernisation of systems and equipment. A few days ago, the overhaul is to be completed at two of the three production facilities of TAIF-NK JSC (scheduled shutdown maintenance is planned to be completed at the HRCC by October 15) and the complex is to start producing products in demand by the market again. Realnoe Vremya got acquainted with how the work is going.
Overhaul is on schedule
Those who have visited the production sites of the oil refining complex more than once are struck by the silence. No, of course, there is no question of a complete absence of sounds: crane drives are buzzing and welding machines are pouring sparks — there is enough noise, but there is no usual hum of technological equipment that turns oil into naphtha, gasoline, diesel fuel, and four dozen more types of products produced by three plants of the complex — Refinery, Gasoline Plant, and HRCC.
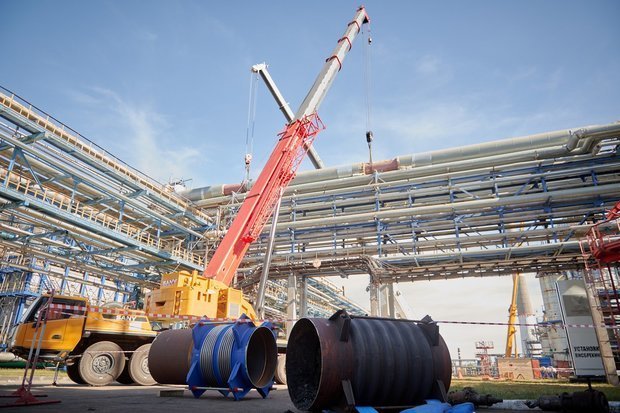
“This year, as in previous years, it is planned to open and clean almost all devices, pipelines, instrumentation, and electrical equipment, without exception. The shutdown was carried out at all production facilities, with the exception of sewage treatment plants, which have operated without a complete shutdown since they were launched in 2015," Alexey Khramov, chief engineer of TAIF-NK JSC, explained to the journalist of Realnoe Vremya.
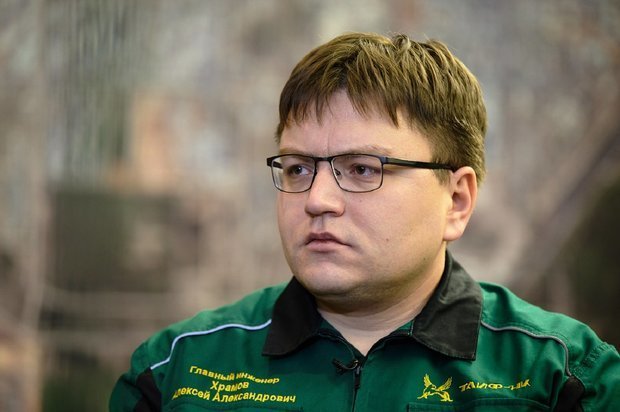
“The overhaul started on September 4. In general, the works are on schedule. The launch of ELOU-AVT-7 at the refinery is scheduled for September 27, and further along the chain all other units. Within 3 days, almost all production facilities will be launched, except for the Heavy Residue Conversion Complex. In the HRCC, the duration of repair is much higher. The approximate launch date there is October 15," said Ilnur Asadullin, the head of the production department of TAIF-NK JSC. He couldn't resist and added: “We are lucky with the weather — dry warm autumn. Nothing interferes with the works.
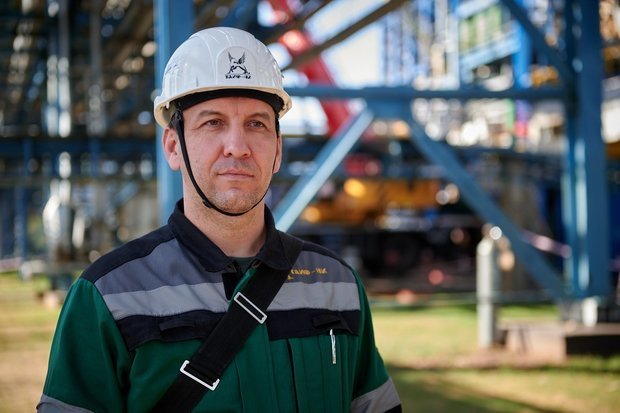
Rains and cold weather, of course, would not be able to completely stop the work, but they would add difficulties. Therefore, the enterprises of the complex appreciate and try to make the most of every fine day. Specialists of TAIF-NK itself and contractors are working at the facilities. This year, over 700 specialists have been attracted from outside.
“There are really a lot of contracting companies involved. And not only from our region: from Perm Region, from Moscow, from St. Petersburg — different specialists from different regions. As for the choice — we have the trading platform ONLINECONTRACT. In the format of open bidding — contractors are selected there, for the most part. In addition, in the format of direct communication with other organisations, enterprises, we find specialised specialists for certain types of work: for example, repair of compressor equipment, pumping equipment, various special devices," said Rustam Bagaviev, the chief mechanic of TAIF-NK JSC.
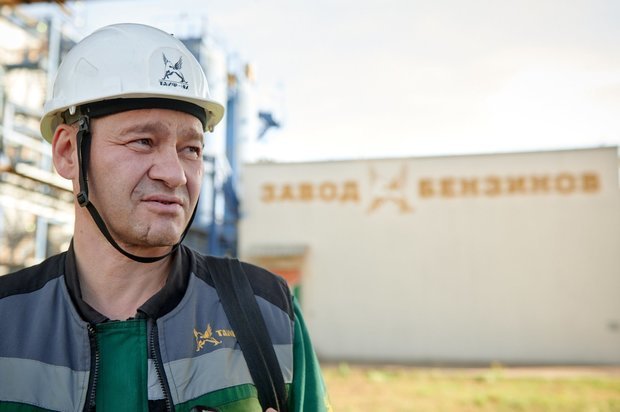
However, one still needs to try to get a contract for the execution of the order. Desire alone is not enough. The requirements for applicants for the execution of works for an enterprise belonging to the fuel and energy industry, which is strategically important for the country, are quite high.
“The tender commission studies all the documentation for the organisations that participate — the availability of SRO permits, the availability of qualified personnel in the organisation's staff, the availability of tools and equipment for carrying out work," explained Anton Nikolaev, the deputy chief engineer for PB, OOS, and OT from TAIF-NK JSC.
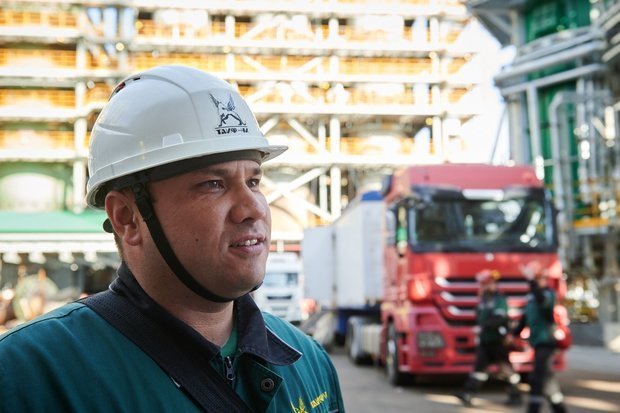
Plus, the willingness to strictly follow the requirements of norms and rules of industrial and industrial safety and the guarantee of high quality of order execution. High-risk roductions do not forgive mistakes or negligence Therefore, at all sites of any of the enterprises of the complex, there is increased control over each stage of work on a daily basis. Contractors treat this approach with understanding.
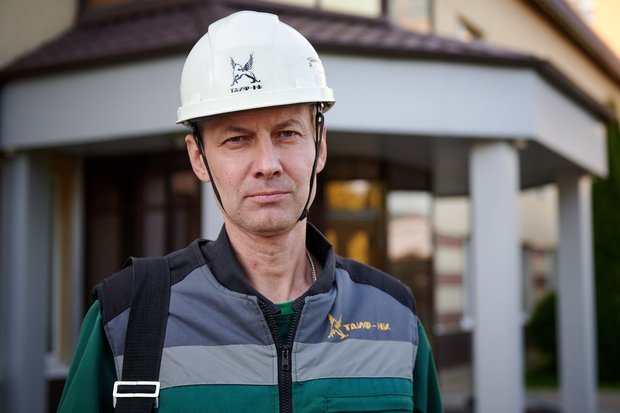
Part of the work has been taken outside the production area," Sergey Dolganov, the chief metrologist of TAIF-NK JSC, said in a conversation with the journalist of Realnoe Vremya. And he explained: “We are carrying out a large amount of work on the verification of devices during the overhaul. For this purpose, contracts have been concluded with both Tatarstan and companies from other regions, which, although not present at the sites, are actively involved in the processes: the devices are taken to them, there, using special equipment, they are checked and then the devices, with the appropriate accompanying documents, are returned to us. Two main requirements: to do everything efficiently and on time.
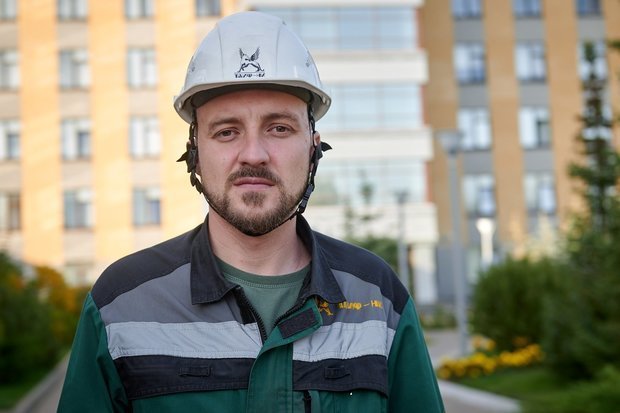
“More than 20 contracting organisations are involved in the direction of the OGE (office of the chief power engineer — ed.) — this is more than 200 contractors, plus more than 300 people of their own staff. In a short period of time, it is necessary to perform an audit, maintenance and repair of the equipment of the entire energy sector, starting from the external power supply system, ending with the power supply inside buildings. Only this approach gives the opportunity to maintain a reliable power supply scheme for the coming year. It is important to understand that when operating technological units, most of the power equipment is not available for maintenance, and therefore, the occurrence of a malfunction in the power supply system immediately affects the stability of the technological process of production. It is the high professionalism of our team of power engineers, the precise organisation of work during the overhaul period that creates confidence in the uninterrupted power supply of the enterprise for the coming year," Vasily Vasilkov, the chief power engineer of TAIF-NK JSC, stressed in an interview.
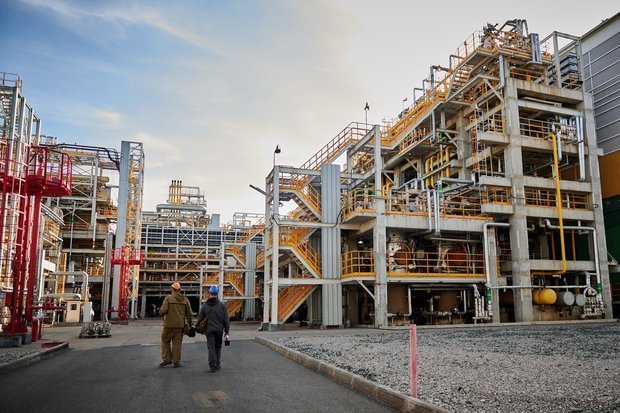
In parallel with the contractors involved directly in the repair and modernisation of equipment, experts are working at all sites. Their task is to assess the condition of the equipment and make a map of the overhaul for the next year — 2024:
“In order to diagnose the condition of the equipment, we constantly carry out thickness measurement of pipelines and apparatuses by specialists of the technical supervision department and hired experts. Without waiting for the rejection values to approach, the company performs timely scheduled repairs and replacement of critical areas. This work is especially relevant for the Heavy Residue Conversion Complex, the equipment of which, due to the peculiarities of the technology, is subject to increased erosion due to the impact of a solid coal additive," Alexey Khramov emphasised.
Refinery is already preparing for loading
Just a few more days, and the TAIF-NK Refinery will be ready to load the equipment with raw materials again. In the meantime, work is also being in full swing here. Compensators are being replaced on the flare collector. These devices, with a diameter of 1000 mm, are an integral part, including the protective system of production.
“The old compensators have already been corroded. New ones have been bought, now they are being replaced. This is a huge job. You can see for yourself — what is the diameter of the pipes. It is necessary to replace 8 units of compensators. Four have already been replaced, there are other four left. Eight — this year, and there are 15 compensators in total for the flare collector. We are changing eight this year, the rest — for the next year," said the director of the Refinery, Vladimir Lakhomov. He himself undertook to show and tell the journalist and photographer of Realnoe Vremya the scale of the current overhaul in production.
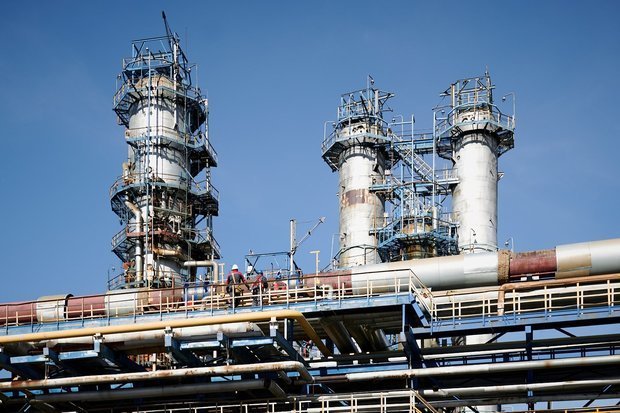
The replacement of compensators — special fragments shaped somewhat like an accordion — takes place once every 10 years. The former ones were made in Penza. The new ones — in the Republic of Belarus.
“The supplier was determined on a tender basis. There is a choice. The price is only different. Now a fragment with a compensator has been cut off, cranes are held on both sides so that the structure does not “break”. For ordinary thin pipes, the system is usually simpler, but here it is just such an “accordion” metal that compensates for temperature differences: if it heats up — it shrinks, if it cools down — it stretches. Thermal expansion is compensated," explained Vladimir Lakhomov, the director of the Refinery.
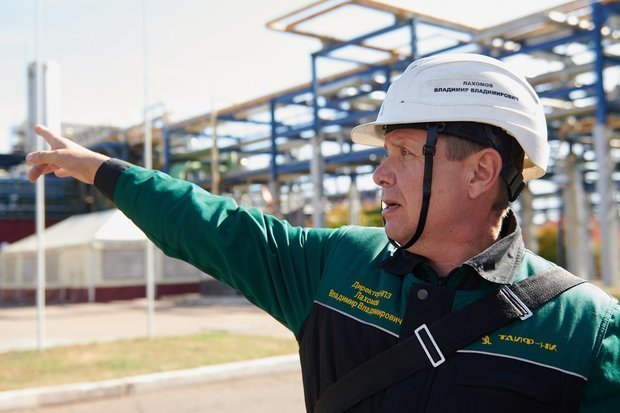
Part of the pipelines is also changed. But if, where everything is in sight, it does not cause any difficulties, then changing the product pipeline hidden in the web of communications is not an easy task.
“The pipelines to be replaced are mainly made of chrome-molybdenum steel. Complex installation, because it is necessary to stretch the replaceable sections in the plexus of existing pipelines. Neither a crane nor other equipment can be put there — everything is on winches, on hands. After welding, the next step is the heat treatment of the seams. The thickness of the pipe metal -14 mm. This is a huge job. In open areas, it is possible to change a kilometre a day. Here — every metre is already an achievement," the director of the plant showed one of the most difficult sections of the overhaul in 2023.
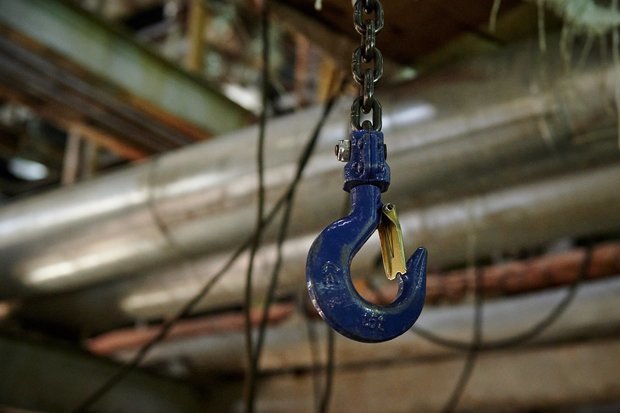
One of the companies involved in the replacement of pipelines is Promtrade PLC. The contractor has been working on the orders of TAIF-NK JSC for several years. And the head of the company's site, Marsel Kashtymov, who was met on the production site, — even more:
“I personally have been here since 2010, probably. However, I used to work in another organisation. Here, probably, all the pipes have already been installed by us (smiles). We are now finishing work in the third workshop and we have come to the rescue in the first one," he shared. To the question: how difficult is the work entrusted to me now, he thought for a while, and then honestly answered: “The work is familiar, and therefore I do not consider it to be very difficult. We will cope exactly on time.”
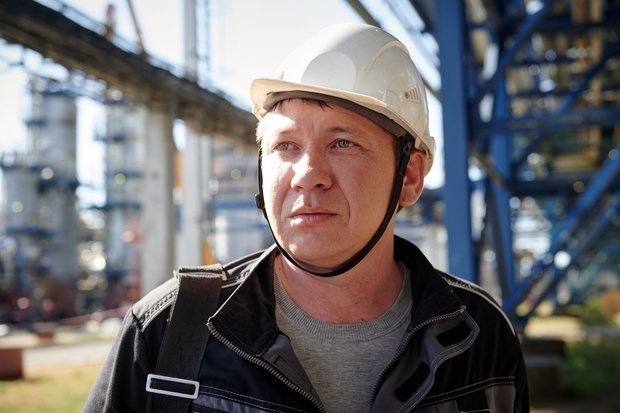
In addition to the traditional disassembly, cleaning, revision of fittings and equipment, opening and cleaning of columns, checking the condition of their internal structure, the overhaul of 2023 has also covered the replacement of one of the four packages of nozzles in the K10 column. Realnoe Vremya did not get to the process itself, but the scope of what was done can be estimated by the volume of filler that has not yet been taken for processing. A pile of corrugated metal plates one and a half times the height of a man is only a quarter of what fills the column.
" We change packages every 3 years. In the K1 and K2 columns, there are bubble-cap plates or trapezoidal plates on which mass exchange occurs, and in this column, there is a regular nozzle that replaces a million plates. It has a special profile — the maximum possible area is placed in a package, which greatly increases the efficiency of processes. The metal is corrugated. It's stainless steel. But over time, it wears out, burning slowly, crumbles and this leads to a deterioration in the result," the director of production explained the essence of the work carried out.
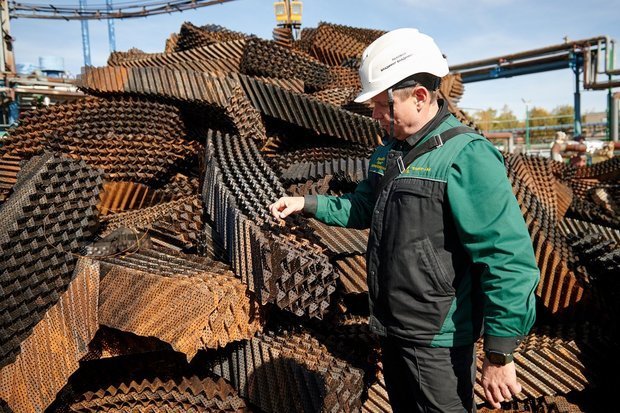
Large-scale transformations have affected the compressor — an integral part of the hydrotreating process. Hydrogen-containing gas circulates through this device. Previously, the device was serviced by foreign specialists. Now — a company from St. Petersburg.
“They disassembled the entire compressor, reviewed, fully measured the flow part with the prospect that NPF Nevintermash JSC (Saint Petersburg) will be able to produce a new flow channel for us. After its installation, it will be possible to say that the compressor is in production, in fact, it is already domestic," Vladimir Lakhomov told about import substitution in practice.
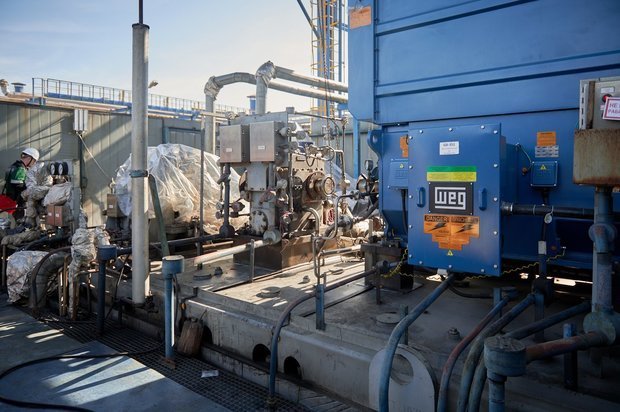
Another reason to be proud is a brand new cooling tower. It ensures the operation of almost all production facilities of the complex. The director of the Refinery showed it to the journalist. It's hard to believe that 2 weeks ago there was a completely different one here — the one from which now only the frame in the background remains.
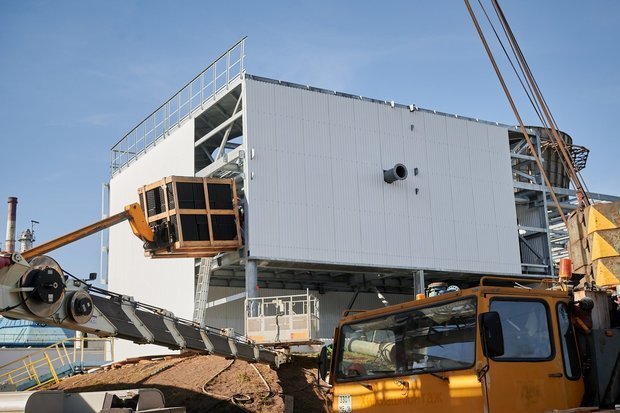
“TMIM company conducts turnkey work. They designed a new cooling tower in our basin. They have packages of attachments — of their own design and manufacture. In terms of electric motor power consumption and area, the old and new cooling towers are comparable, but the new efficiency will be greater due to the uniqueness of nozzles. The company is local — from Tatarstan, and they work all over Russia. They work quickly, clearly. It should be borne in mind that cooling towers can be shut down only after all production is shut down, and they will be the very first to turn on. They managed to disassemble the old one, put a new one, now they are mounting packages of nozzles. By the time the overhaul is completed, they will have time to launch half of the cooling tower, which is enough to ensure the phased commissioning of all production facilities. In the meantime, this will happen — they will assemble and launch the second half," Vladimir Lakhomov explained what is happening.
The overhaul is striking in scale
Around the HRCC, the group of Realnoe Vremya was accompanied by the director of the complex, Andrey Konovnin. When asked by the journalist that there is less lifting equipment on the production site than last year — whether this means that the amount of work is more modest — he just smiled.
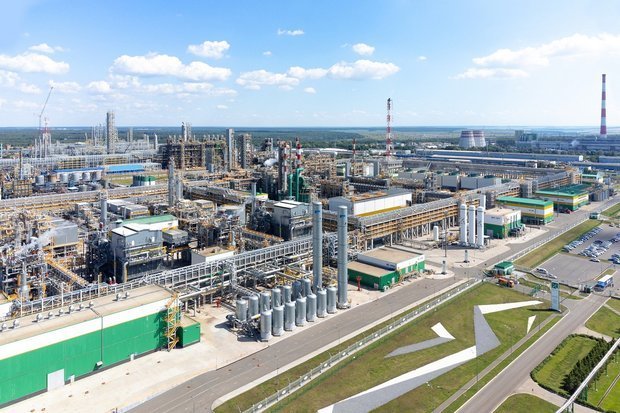
“The current overhaul is much larger than the previous one in terms of the volume of work, since the service life of equipment under high pressure has increased significantly. Therefore, a complete revision is needed. To date, 62 contractors are involved at the site of the complex. This is about 460 people," Andrey Konovnin explained.
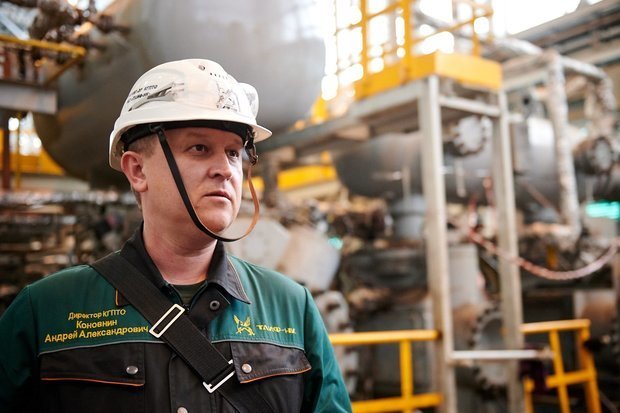
The essential point is that not everything that is happening on the site is in plain sight. In particular, in the reactor unit — the huge “heart” of the complex, right at this moment there is being a thorough examination of the inner surface. The revision of the high-pressure separators has been completed. It remains only to close them again. However, “only” is not appropriate here. The multi-tonne metal “lid” of the separator rises to a huge height with the help of cranes — and this is jewelry work, a slightest mistake can result in tens or even hundreds of millions of rubles of damage. Therefore, here, as at any other production of TAIF-NK JSC, the choice of contractors is taken very seriously.
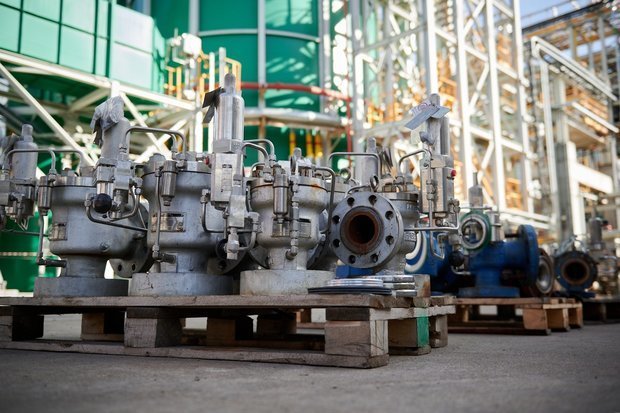
In the compressor room, the work of specialists also looks like real magic:
“The circulation compressor pumps hydrogen-containing gas necessary for the reaction of hydrocracking of tar, and this year for the first time we have completely disassembled it for revision of internal parts. At the moment, we are making measurements of the rotor itself, to have the opportunity to manufacture spare parts. We have a repair kit, but we need to be sure that there will be a stock. The compressor has been operating without complete disassembly since 2016. The survey showed that the main working parts are in perfect order. Consumables — gas seals, etc. — demanded attention, the rest — without comments. The car is reliable," the director of the HRCC commented on what was happening.
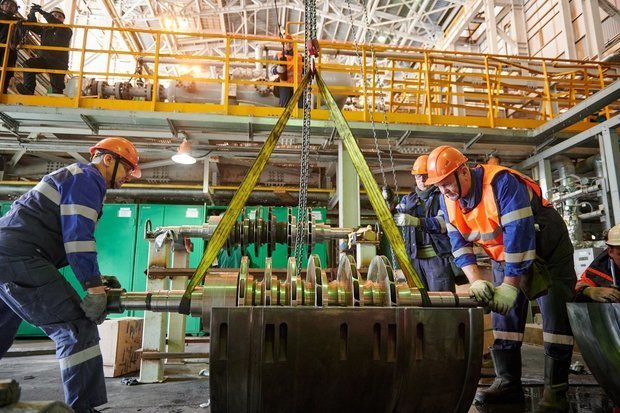
In the future, the compressor maintenance will be fully entrusted to a Russian company. And this is another result of a large-scale import substitution programme.
“Probably, this is such a feature of the current overhaul: the term 'import substitution' from the category of new and fashionable has firmly passed into something self-evident. More and more equipment, parts, catalysts are used by domestic production. Yes, sometimes there are questions about quality, delivery time, but we are sure that these are temporary issues. The main thing is that we see progress here," said Alexey Khramov, the chief engineer of TAIF-NK JSC. He also added: “We are implementing projects to improve the reliability of the technological scheme, the share of domestic instrumentation and control equipment has increased many times. At the moment, TAIF-NK JSC is carrying out reverse engineering of three main centrifugal compressors and 10 reciprocating machines. Including unique ones with a capacity of 15 MW.
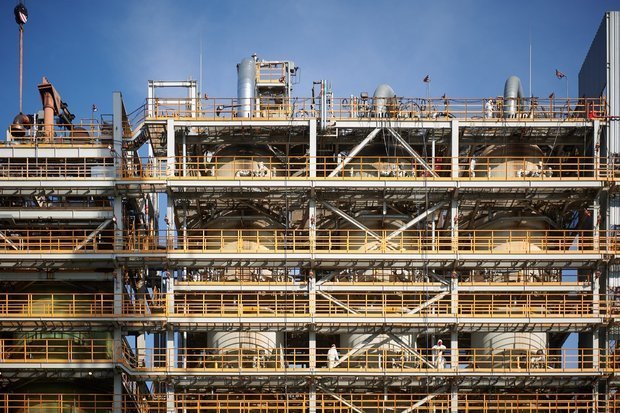
Large-scale work is underway to transfer production to domestic catalysts. Chief Engineer of TAIF-NK JSC Alexey Khramov told about this:
“During the overhaul period of 2023, it is planned to replace part of the catalysts produced by unfriendly countries with catalysts produced on the territory of our country or China. In particular, instead of the steam reforming catalysts previously used by the British firm Johnson Matti, catalysts from the Chinese company SWCHEM will be loaded. TAIF-NK JSC tries to use domestic catalysts as much as possible and only in exceptional cases to purchase Chinese products. So, within two years, we have completely switched to domestic vacuum gas oil cracking catalysts, we use domestic protective layers of hydrotreating catalysts and have begun the partial replacement of the catalyst itself, in the production of sulphur we are also gradually changing foreign catalysts to domestic ones.
If there are claims, then only to ourselves
So the chief engineer of the Gasoline Plant, Nikolay Kharitonov, answered the question of how confident one can be in the quality of the work carried out during the overhaul. He explained that the level of involvement of the production staff in all processes is the highest.
“Our team is also all divided into brigades, and each such brigade has its own areas of responsibility, sections. Yes, contractors for a certain range of tasks were determined in advance, but who knows better than the specialists themselves working on this equipment, on these processes — where and what to pay attention to, so that they can work for a year without difficulties and excesses.
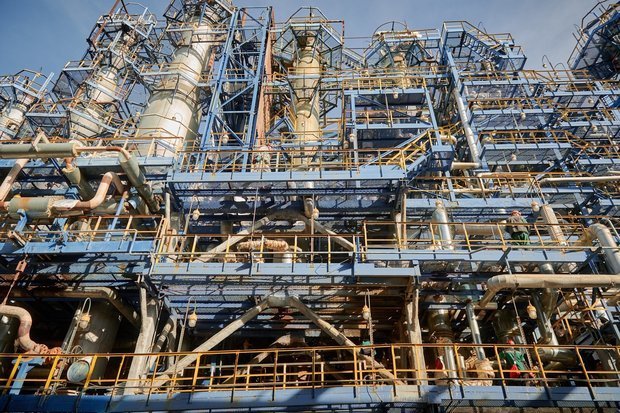
Radik Zakirov — mechanic of shop No. 01 of the Gasoline Plant is a direct confirmation of this. The specialist, hurrying on business, managed to be stopped just for a minute. After all, it's rush period.
“First, we check together with the contractor, we indicate all the defective places. Then, upon completion of the work, we carry out the acceptance of the execution. We control the work of both contractors and our specialists. I myself have been involved in these processes since 2005: first, as a locksmith here, since 2017 as a foreman, then as a senior foreman of the reactor unit, and since last year — as a shop mechanic. Yes, it happens that I have to point out the shortcomings in the work to bring it to mind. There is no other way," he explained.
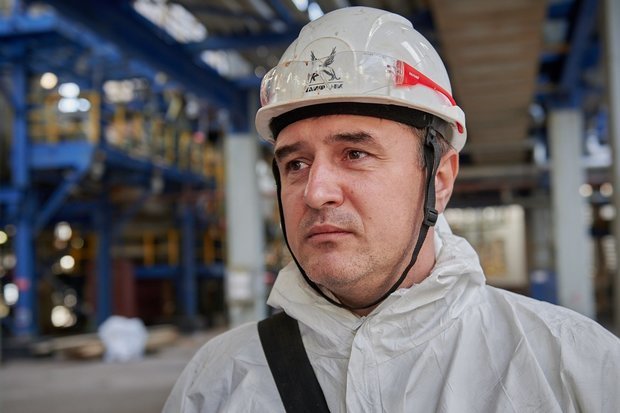
Nikolay Kharitonov was in the control room at the time of the appearance of the Realnoe Vremya group: he was overseeing the implementation of another import substitution process:
“The work is underway to replace the controller with a domestic one. Before that, the controller was Siemens, but since they have now refused to cooperate, it is being replaced with a domestic one," he explained.
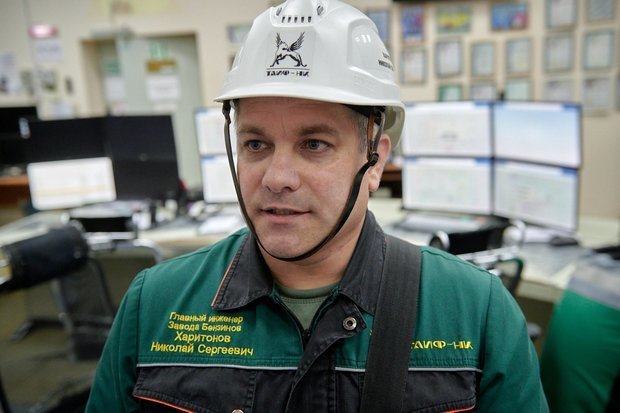
Alexander Morubov, a representative of the Tatarstan company Khimpromproekt, explained that the organisation has been working closely with oil refining, chemical and petrochemical enterprises for 12 years and, therefore, confidently joined the fight for the right to win the tender from TAIF-NK. Now the works are already close to completion:
“There is a task to replace the control system for regulating the compressor's anti-surge protection. The old system worked on Siemens equipment, and we offered the new one entirely on a Russian controller (manufactured in Yekaterinburg) and Russian software. To realise the task, we had to fully study the software operating in production, adapt it to Russian, run it on stands, and now the cabinet is assembled, the software is written, and installation is being completed at the enterprise. More precisely, commissioning works are already underway," the specialist noted.
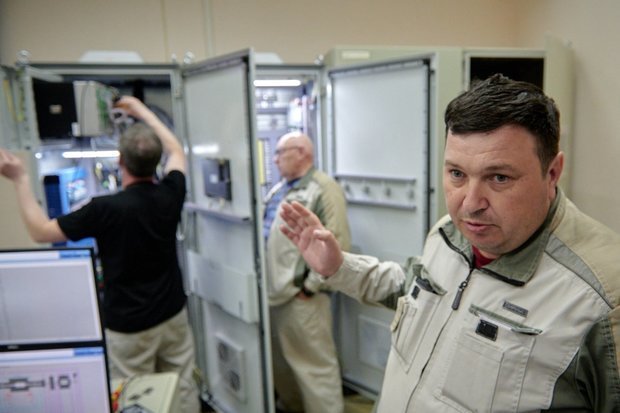
A large-scale upgrade with the replacement of domestic components and parts is carried out on the compressor equipment of the production. A new engine has already been installed this year, and it is planned to update the flow part in 2024. It is now manufactured by a company from St. Petersburg.
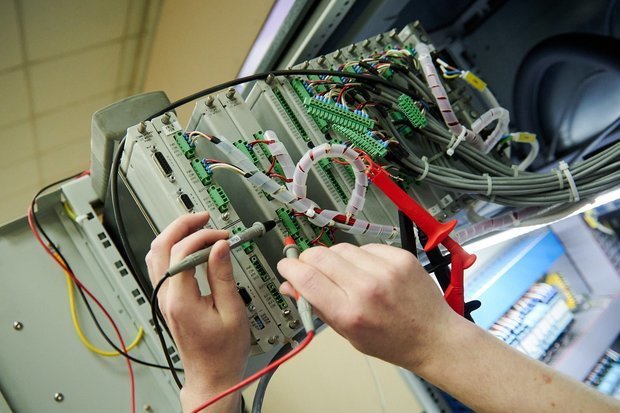
At various sites, the equipment received from the verification is installed in its place. The works on the gas fractionating column is almost completed:
“The mines were completely disassembled here, plates were removed, these devices were cleaned, diagnostics, inspection, and then assembly," the chief engineer of the Gasoline Plant continued the tour.
Two packages of attachments that have served their time have been replaced. Other technological equipment has also been opened, checked, and cleaned. They do not see any obstacles to launch production exactly in the allocated time — at the Gasoline Plant.
The main task: to ensure trouble-free operation
Alexey Khramov, the chief engineer of the complex, does not get tired of talking about this:
“At the same time, not counting their own personnel, more than 1,000 representatives of contracting organisations, large-sized equipment, ultra-high pressure apparatuses, work with the use of fire, gas-hazardous work and even in the environment of nitrogen, which is deadly to humans, work at the production facilities. These are thousands of people doing dangerous and responsible work. After the repair work is completed, it is required to be pressed qualitatively and to enter the trouble-free mode," he emphasises.
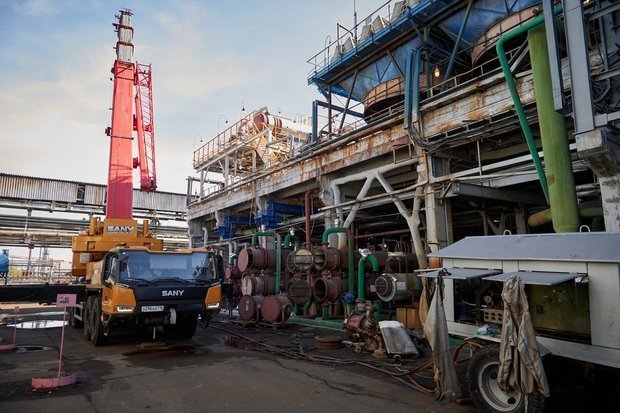
No less important is the fact that during major repairs not only the condition of the equipment is evaluated, but also its effectiveness. As reported to Realnoe Vremya, according to the units that have exhausted their capabilities, a decision is made either to modernise or to replace them with new, more advanced, efficient and environmentally friendly ones.
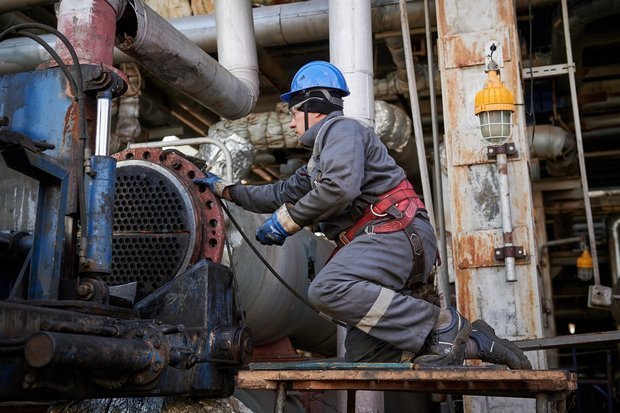
By the way, about ecology:
“Increasing the efficiency and reliability of production, the company does not forget about environmental protection. So, in 2023, the practice of closed steaming of equipment on a torch with the use of special expensive reagents that reduce the anthropogenic impact on the environment has been continued. Cleaning of oil tanks was carried out using a modern mobile tank cleaning complex MKO-10000 with the minimum possible presence of personnel inside the tank," Alexey Khramov emphasised. He also added: “The work is also planned to reduce the discharge of process gases to the torch at the HRCC and the Gasoline Plant. After the implementation of all measures, we expect additional significant savings in natural gas.
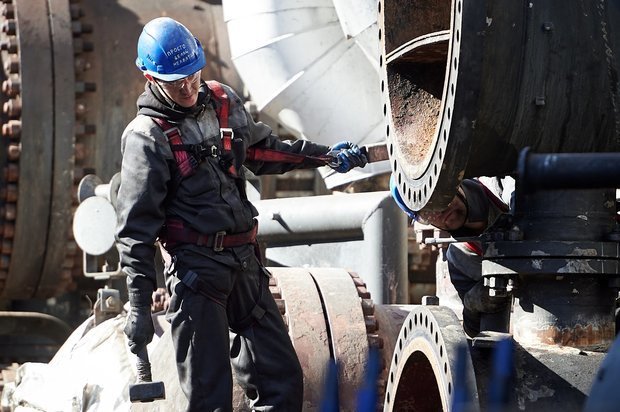
As the chief engineer of TAIF-NK JSC noted, now the entire team of the company is working for one goal: to complete the entire complex of tasks planned as part of the overhaul on time. People work on additional schedules, go to the sites and on weekends. It is important not only to have time to do everything, but also to make sure that each of the tasks is completed as accurately and efficiently as possible. This is the only way to ensure trouble-free and non-stop operation of the entire oil refining complex in the next inter-repair period.
Подписывайтесь на телеграм-канал, группу «ВКонтакте» и страницу в «Одноклассниках» «Реального времени». Ежедневные видео на Rutube и «Дзене».