‘It’s real chemistry here’
Members of the Tatarstan Association of Motor Transport Enterprises visited the production site of Taif Lubricants
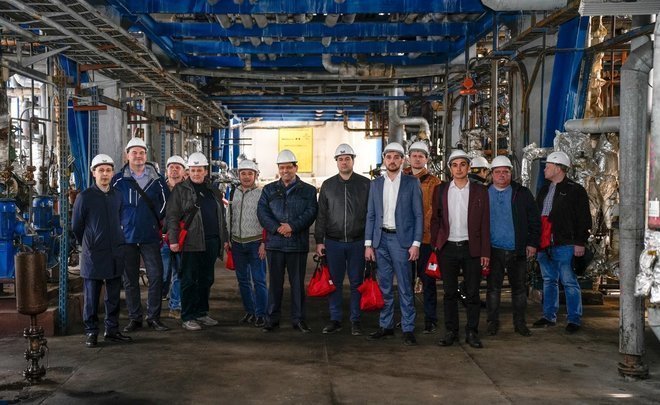
“Taif Lubricants is an innovative enterprise that makes European-quality lubricants. Nowadays there was signed an agreement with one of our transport companies on the distribution of Taif Lubricants in the Republic of Tatarstan,” says President of Logistics and Motor Transportation of Tatarstan non-profit partnership, Director of ATL-Trans company Mikhail Levashov. Together with members of the Tatarstan Association of Motor Transport Enterprises and representatives of Kamatransservice, he visited the production site of TAIF-SM. During the tour, the guests were shown the unique plant producing Group IV polyalphaolefin base oils and commodity oils under the brand of Taif Lubricants. Also, the guests got acquainted with multi-step production control.
208 tonnes of oil a day is the plant’s peak capacity
The production site of TAIF Lubricants had a doors open day. Members of the Tatarstan Association of Motor Transport Enterprises arrived to see the only polyalphaolefin oil (PAO) plant in Russia. Before going to the production site, the guests did mandatorily an introductory safety briefing and received personal protective equipment.
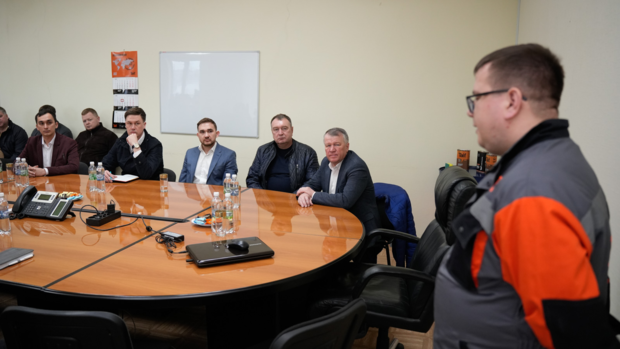
“All workers of third organisations, students who join us must do an introductory process safety briefing. TAIF Lubricants is a highly hazardous plant. Safety rules cannot be neglected,” Yevgeny Zhikharev, vice chief engineer of production control, process safety and environment, addressed the audience. Director General of TAIF-SM Alexey Osipov welcomed the delegation of 32 people on the territory of the enterprise, he personally took them on an excursion, told them about the specifics of work and the company’s history.
“The lubricant production complex was built and launched in Nizhnekamsk in 2003. After large-scale modernisation in 2020, the company started to operate as Russia’s first and unique producer of basic polyalphaolefin oils. Today we made two types of products. It is basic Group IV oils and lubricants under the brand of Taif Lubricants. We produce a total of more than 270 products. The peak capacity of the plant is 208 tonnes of oils a day, which allows making 60,000 tonnes of lubricants and 10,000 tonnes of basic oils a year,” stressed Alexey Osipov.

The director general added that the modernisation affected almost all the plant: new filtration, automation and management systems were installed in polyalphaolefin blending and synthesis shops, there appeared a heating chamber of additives in barrels and on the container packaging line, loading and unloading racks and service tanks were updated. The equipment of leading global and Russian producers were modernised to process linear alphaolefins making polyalphaolefin oils and producing commodity oils based on them.
State-of-the-art equipment
TAIF-SM’s laboratory where multi-step quality control is performed at all production stages became the first point. Modern equipment allows tracking the quality of products around the clock.
The guests were shown one of Russia’s biggest fleet of chromatograph, spectrometer, equipment determining kinematic viscosity, pour and freezing point, ash content, apparent viscosity limit using cold-cranking simulator, corrosive attack on metals, capabilities of petroleum oils and synthetic liquids to separate humidity and much more.

“Our laboratory operates according to analytic control plan. Testing is examined in three stages. The first one tests the readiness. This stage includes a shortened list of indicators, we verify if oil was examined for all process flow log. If everything is correct, we issue an order for authorisation. A more expanded list of analyses is done at the second stage — up to 18 indicators. If they are satisfactory, we issue a quality certificate. After that, the product is packed into barrels or canisters from the reactor. After packaging we check out the quality of products according to a shortened list of testing. If all analyses are fine, we issue a quality certificate,” says head of the laboratory Maria Bitkina.

She noted that the laboratory prefers automated devices thanks to which human factor doesn’t influence the accuracy of results. In case of doubtful results or main equipment repair, laboratory workers do testing in back-up equipment.
“We check the product quality in this lab. Specialists in the Kazan R&D create and do research on lubricants of Taif Lubricants. It is also equipped with special laboratory equipment meeting the latest international requirements. The centre improves the formula considering global trends and consumers’ demand, develop and test new products,” specified Alexey Osipov.
Production of basic PAO base oils
After looking over the laboratory, delegation members went to the polyalphaolefin base oil plant. During the modernisation, new equipment from leading global and Russian brands was installed here to process linear alphaolefins to make polyalphaolefin base oils from them and create high-tech commodity oils on their basis.
The guests visited the operator’s room in Oligomerisation, Proceessing and Dehydration Shop. Shop foreman Ilshat Shakhmayev said that decene — feedstock for Taif Lubricants polyalphaolefin base oils — comes from Nizhnekamskneftekhim. The PAO-based products are considered Group IV synthetic oils. Unlike mineral-based products, they demonstrate stability at a high speed, endurance in the most extreme conditions and dramatic temperature fluctuations.

“First of all, we dry the incoming feedstock decene. Then we send it to the oligomerisation unit where alphaolefin oils turn into polyalphaolefins thanks to a complicated chemical process,” he clarified.
Delegation members saw the oligomerisation unit too. They saw the reactors where simple hydrocarbon molecules create new substances first-hand.
“Our shop is unique. There is no other in Russia. All oils are mineral in our country, while we make synthetic ones. It’s real chemistry here,” Ilshat Shakhmayev says proudly.

Blending commodity oil production
The blending commodity oil production plant became the next stop on the route. The shop includes seven reactors with a total volume of 92 cubic metres, each of which stands on the so-called three needles — strain gauge scales. Operators themselves jokingly call themselves cooks figuratively comparing the huge reactors with hermetic saucepans where commodity oil is cooked. Laboratory workers provide recipes for its production.

“Everything happens here strictly according to the recipe. Every oil is provided a reading sheet where the dose is spelt out. First, we heat base oils to 50-55 degrees, then we add thickener, additives and mix it all. We make the thickener ourselves,” shop foreman Nikolay Degtyar noted and added that the ingredients are added automatically to the reactor to make the commodity oil

The guests were also shown a commodity oil packaging unit. Containers were assembled here during the modernisation in 2019 that allow packing four different types of oils at the same time. Three automated lines can accurately pack products into cans of any capacity — from a barrel to a canister.

The loading and unloading rack was completely re-equipped to pour products. Two combustible liquid (oils) and one highly inflammable liquid loading units are equipped with very precise consumption meters. Nowadays the modernisation doesn’t stop, survey and design works are underway to increase the capacity of the shop, a modern line used to pack oil to small containers by Russia’s Mekhatronika was purchased too.
New leader in premium segment
The excursion to the production shops lasted for about two hours. Delegation members of the Tatarstan Association of Motor Transport Enterprises asked questions, shared experience and their observations. The meeting ended with a round-table talk discussing topical issues.

“It has been a very useful excursion for the enterprise. It broadens one’s mind. When the dialogue is held directly on the production site, you look differently at many things. For us, it has been good exchange of experience. Representatives of different transport companies that have a lot of machinery consuming motor, hydraulic and transmission oils in the fleet have arrived today,” says Director of Synthetic Oil Plant Ruzil Vafin.
President of Logistics and Motor Transportation of Tatarstan non-profit partnership, Director of ATL-Trans company Mikhail Levashov noted that the exit of foreign brands of lubricants brought transport companies to a deadlock first, but after visiting TAIF-SM, seeing the modern production with their own eyes, he finally made sure that Russian polyalphaolefin base oil producers allowed creating products surpassing requirements of global equipment manufacturers.

“Taif Lubricants is an innovative enterprise that makes European-quality lubricants. Nowadays there was signed an agreement with one of our transport companies on the distribution of Taif Lubricants in the Republic of Tatarstan. Now we will do testing in cars in the association’s fleets and we are ready to buy these oils,” he stresses.
Ayrat Kalimullin, director of the Drivers’ Training and Rehabilitation Centre, shared his impression of the excursion too:

“I came to be happy for the homeland. I am proud of having such production, people who do care about their work. A lot of products are made here in Russia that can compete with foreign analogues. Many of my acquaintances didn’t know until recently that Nizhnekamsk had such a unique oil plant. Our people got used to think that everything made abroad is good and what is made in Russia is bad. Stereotypes need to be broken.”
After the excursion, delegation members also agreed that Taif Lubricants would soon become an undoubted leader in the premium segment of Russia’s synthetic oils.
Подписывайтесь на телеграм-канал, группу «ВКонтакте» и страницу в «Одноклассниках» «Реального времени». Ежедневные видео на Rutube, «Дзене» и Youtube.