HRCC — unique project in the world oil refining
The start-up of the Heavy Residue Conversion Complex allowed TAIF-NK to achieve the highest values of extraction of light oil products among Russian refineries

In November 2021, the Heavy Residue Conversion Complex received all the necessary permits and was officially put into pilot operation. Today, the share of extraction of light oil products at the production facilities of TAIF-NK JSC from each tonne of raw materials, and oil of not the best quality, has exceeded 90%. No oil refining company in the world is able to process oil so economically and completely. What is the uniqueness of the production, what difficulties TAIF-NK and TAIF specialists faced during the implementation of the project, and how much the initial configuration of the Complex had changed by the time of launch — read in the first part of Realnoe Vremya's material.
No other such complexes in the world
September, 2022. The site of Kazan Expo International Exhibition Centre. TatOilExpo is one of the country's largest forums in the field of oil, gas, oil refining and petrochemistry. Immediately after the official start of the event, officials — Tatarstan President Rustam Minnikhanov and forum guests —visited the exhibition, where more than 200 companies from 25 regions from all over Russia and four foreign countries presented their achievements.
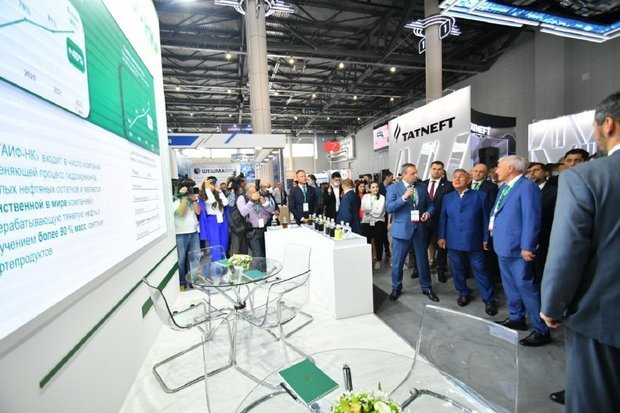
One of the most notable exhibitors, traditionally — TAIF-NK JSC. TAIF-NK CEO Maksim Novikov always has something to tell: the company is one of the most technically and technologically advanced in the country. This time, the main emphasis was placed on the achievements associated with the commissioning of the Heavy Residue Convertion Complex into pilot operation. In November 2021, the unique production, after obtaining all necessary permits, was launched in the pilot-industrial mode of deep processing of tar and vacuum gas oil.
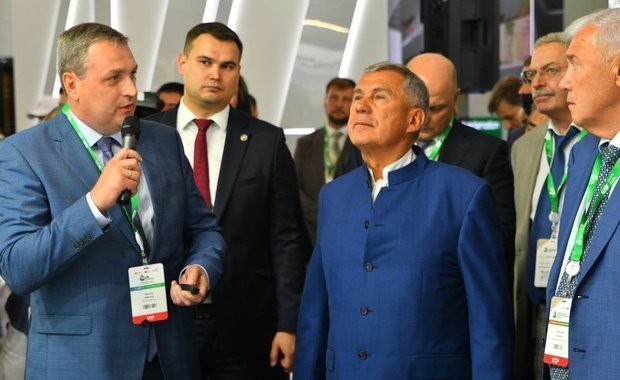
“The main goal of TAIF-NK is the development of truly advanced oil refining, the maximum increase in the selection of light oil products. The company has achieved an average result of more than 90% over the year, in August — this figure was 93,5%. This is the highest indicator in the world. In principle, there are no such units anywhere where heavy oil is processed and light oil products are obtained in such a volume," Maksim Novikov cited the figures.
More precisely, technologies that solve similar problems are created in the world, and there are not so few of them — already in October, directly at the production site, Aleksey Khramov, the chief engineer of TAIF-NK JSC, shared with the journalist.
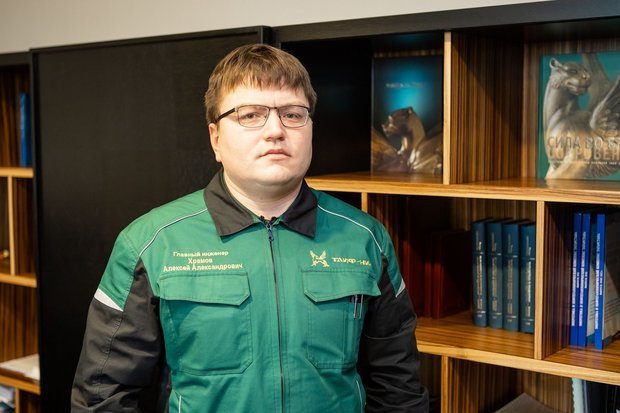
“Among the processes that are close in efficiency to VCC technology, it should be noted: H-Oil process (Axens — France), LC-Fining (Chevron-Lummus — USA), Eni-slurry (ENI — Italy), Uniflex (UOP USA), hydroconversion of the V. A. Topchiev Institute of Petrochemical Synthesis of the Russian Academy of Sciences. The conversion of tar into light oil products in these processes, according to various sources, reaches no more than 70%. Industrially developed processes that allow efficient processing of tar of high-sulphur oil into high-quality light oil products with a conversion rate of 90% to 95%, except for VCC, do not really exist at present," he said.
Pinnacle of oil refining technological development
“Blood of the earth”, “oleum terrae” — they called it in the centuries-old history. The more technologically advanced humanity developed, the greater the hopes and plans it has built for the processing of priceless raw materials.
It all started with primary distillation: to get lighting kerosene, and later diesel fuel and gasoline, people learned to heat oil to 380° C, extracting the most easily recoverable fractions. The next step was the processes of thermal cracking and delayed coking, where the processes of breaking carbon C-C bonds already take place at temperatures of about 500° C, but without catalysts. The processing rate has increased — light unsaturated fractions are sent for hydroskimming. The by-product is a carbon-enriched coke residue. The worse the raw material, the more of this coke.
The next stage in the evolution of oil refining is catalytic cracking in a fluidized bed. Even higher temperatures, a complex circulation system of a constantly regenerating catalyst. Later, the hydrocracking process became a breakthrough technology, where vacuum distillates are processed into a wide range of high-quality light petroleum products on stationary catalysts in a hydrogen environment, under high (about 160 atmospheres) pressure. But truly advanced oil refining was out of the question here. An attempt to recycle heavy residues at a hydrocracking plant would inevitably lead to the catalyst coking and stopping.
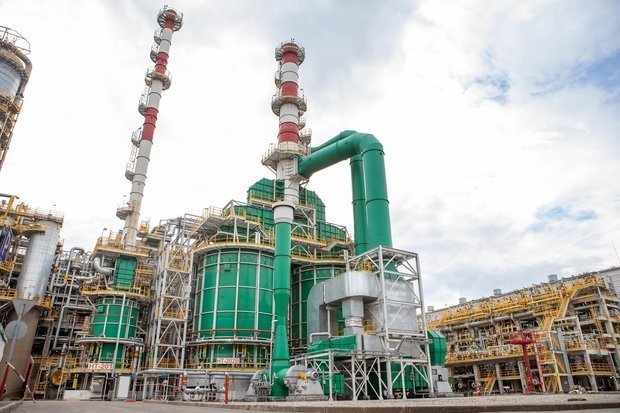
“The process of combined thermal and hydrocracking of tar (VCC, or Veba Combi Cracking), implemented at the HRCC, is the pinnacle of technological development of ultra-advanced oil refining processes in the world," Aleksey Khramov, the chief engineer of JSC TAIF-NK, is sure. “This process combines all technical solutions of the processes described above. At the first stage, tar is processed in suspension reactors at a temperature of more than 450° C and a hydrogen pressure of up to 200 atmospheres. For the adsorption of metals and coking components of raw materials, a specialised additive is used — activated lignite, and the process itself takes place in a suspension, constantly moving medium. The conversion of tar into light, high-quality and ready-to-use petroleum products is from 90%, and this is a unique result. Then the products of suspension reactors, on licensed separators, are separated from the coal additive that adsorbed metals, and the precursors of coke, which are catalytic poisons. The reaction products are mixed with heated vacuum gas oil and enter the second stage of classical hydrocracking with a stationary catalyst layer. This combination of thermo- and hydrocracking makes it possible to remove catalytic poisons before feeding the raw material to the second stage catalyst layer. This way we eliminate the disadvantage of hydrocracking process with its stationary catalyst layers. At the output, we get a conversion rate of more than 95%," Aleksey Khramov told the journalist about the technology.
They shouted “it's impossible!”
A thoughtful, balanced, in some ways, perhaps, even a leisurely approach to solving the most difficult tasks is one of the important qualities of TAIF Group. But after all, the tasks solved are non-trivial. Something is being done for the first time in Russia, in the world, in the industry. TAIF JSC started to seek a technology that would allow efficient and maximally advanced convertion of heavy oil distillation residues at the end of the last century — in 1998-1999. The study of the possibilities of all solutions, including those that at that time were actually more of a theory, at best supported by a mock test.
Of course, large-scale projects are not implemented from scratch, at first they arise in the minds of extraordinary personalities, leaders with a steel rod, with strong will and determination.
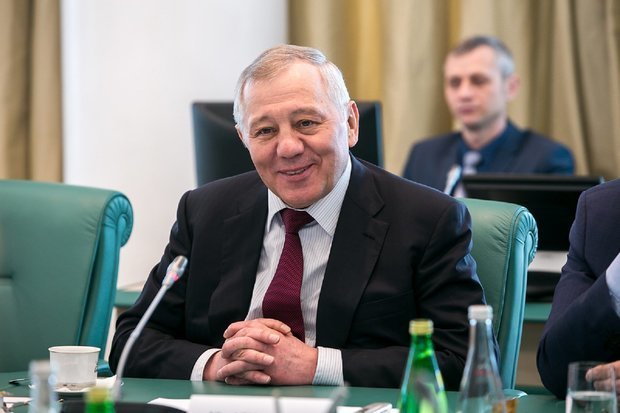
The bold decision to build and launch the unique HRCC in Nizhnekamsk for the whole world belongs to Director General of TAIF JSC Albert Shigabutdinov and his Deputy for Petrochemistry and Oil Refining Vladimir Presnyakov. Despite doubts about the success of such an ambitious project expressed by some colleagues from the field of oil refining, Shigabutdinov's team stubbornly implemented the large-scale project step by step.
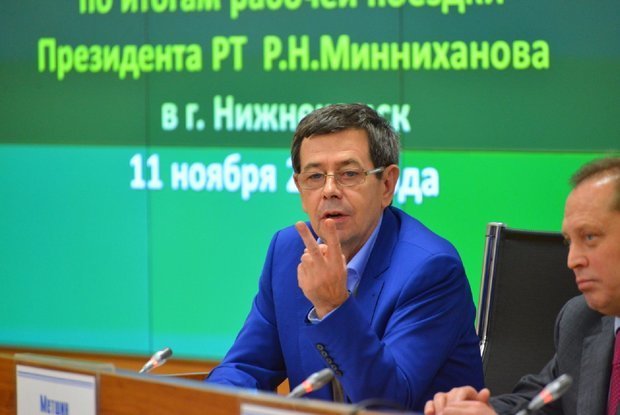
“This technology has been implemented on such a scale for the first time in the world. This led to a lot of questions related to the design of units, equipment and the composition of the metals from which they are made. They had to go very deep into hydrodynamics, thermodynamics, design activities, materials science, metal science," he explained in the interview with Vedomosti newspaper in 2019. Albert Shigabutdinov.
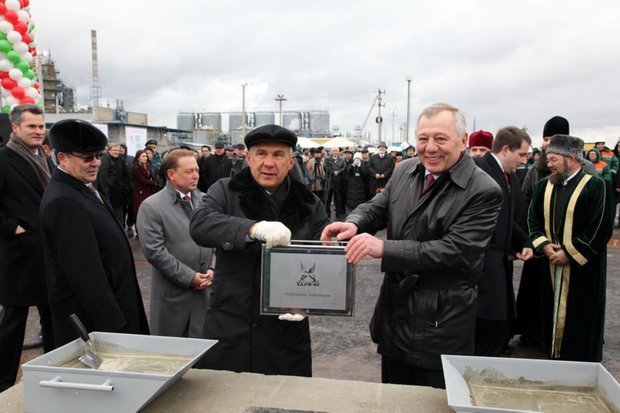
“This is impossible," such words are heard quite often when TAIF announces the launch of another large-scale project. Skeptics claim that it is impossible to achieve great results with less investment, that it is unrealistic to implement projects so efficiently and quickly, or they say that the chosen technology “will definitely not work” simply because no one has implemented it on such a scale before.
The choice was made in 2011, when an agreement was signed with the license holder for VCC technology. In February 2012, with the support of the shareholders of TAIF JSC, TAIF-NK started implementing one of its most ambitious projects — the construction of the Heavy Residue Convertion Complex residues (HRCC). The foundation stone of the new production was laid on November 9, 2012. The ceremony was attended by Tatarstan President Rustam Minnikhanov, Director General of TAIF JSC Albert Shigabutdinov, Deputy Director General of TAIF JSC Vladimir Presnyakov (the ideological mastermind of the project, who scrupulously studied the subtleties and possibilities of technology for more than 10 years before), representatives of the licensor company and other officials.
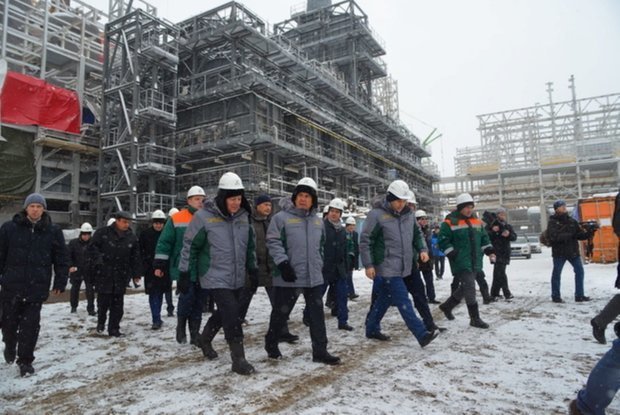
For about 10 years, from the moment of construction to the commissioning of the HRCC, Albert Shigabutdinov took part in meetings almost daily non-stop. The difficulties that arose during the implementation of the complex were solved in close conjunction by the staff of TAIF, TAIF-NK and Russian scientists.
A serious support for the company was the fact that the leadership of Tatarstan did not share the skepticism of many. In 2015, Tatarstan President Rustam Minnikhanov, who visited the site of the actively under construction complex, once again stressed the republic's interest in the success of the megaproject.
Before TAIF, no one had ever implemented VCC technology on such a scale. And absolutely no one has tried to process heavy, high-sulphur, metal-saturated tar using this technology. This explains the caution of the Group of Companies in carrying out commissioning and comprehensive testing.
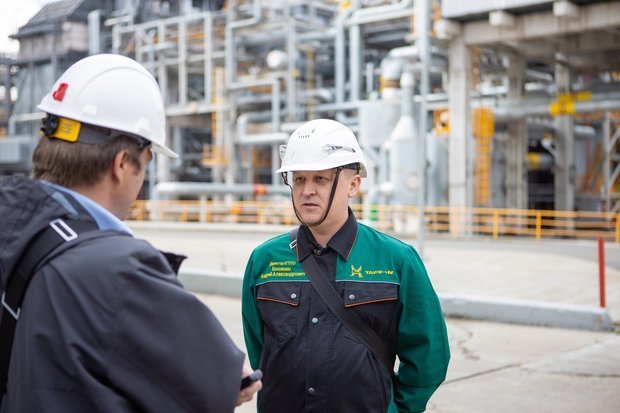
“To be honest, we had to refine a lot. I will not go into details, I will say this: at every stage of production, we faced all sorts of questions. We coped with this thanks to the well-coordinated work of the team. Sometimes, it was necessary to take risks in solving problems, but without going beyond industrial safety and labour protection. In some cases, it was necessary to step back in decisions altogether in order to win at certain stages and moments, processes of work in the future. An integrated and systematic approach to solving emerging issues, the initiative of the staff, the interaction of all the services of TAIF-NK JSC — these are the key elements that contributed to the success of the commissioning of the HRCC," Director of the HRCC Andrey Konovnin noted in an interview with the journalist of Realnoe Vremya.
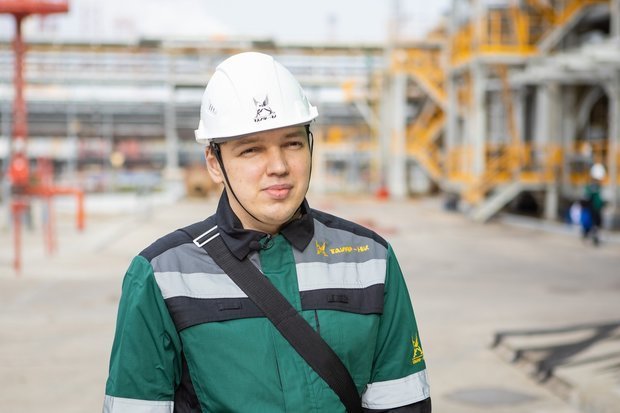
“The most difficult thing here was the unknown. This is a completely new direction, a new technology. A lot of things were unknown to us who came here during the construction and commissioning of equipment. What is it? How? The equipment used here is not the most unique. And its combination with the process modes and with the environment in which the process takes place is unique. Very often, the solutions that were originally intended did not fit, and they had to be improved, step by step to solve the tasks assigned to us. And I think that we have successfully succeeded in this — Artur Urazaykin, the chief engineer of the HRCC, told about the stage of formation of the Complex.
Skeptics saw the delays as a support for their negativity, and TAIF-NK and TAIF specialists saw opportunities to improve this technology in order to make it even more effective and, last but not least, safe.
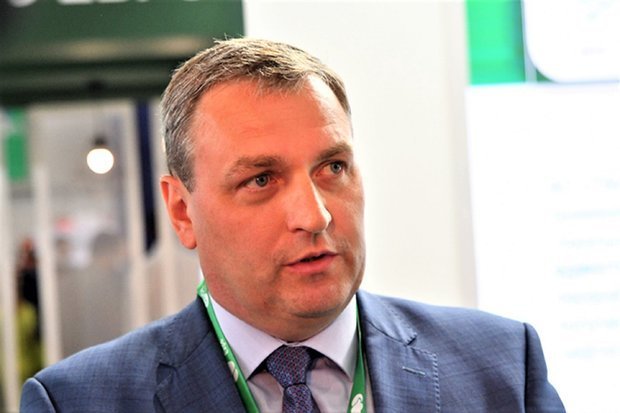
“Yes, there was enough negativity, of course. But the most important thing was to believe in the team. Our team is coherent and everyone believed in the achievability of the goal. Together with TAIF, this task was successfully implemented. Of course, many points were finalised by TAIF and TAIF-NK specialists," Maksim Novikov, the company's CEO, said in the conversation with the journalist of Realnoe Vremya.
Team's titanic work has yielded results
The titanic work of the team gave its results already in the first half of 2018, thanks to the work of the HRCC in the testing mode on vacuum gas oil, the selection of light fractions was significantly increased, today the entire volume of tar and vacuum gas oil produced is processed into TAIF-NK, turning into light petroleum products — diesel fuel, naphtha, kerosene, LPG.
Without exaggeration, the whole of Tatarstan was waiting for the commissioning of the HRCC. At one of the meetings, President of the Republic of Tatarstan Rustam Minnikhanov noted that the launch of the new production would significantly affect the economic potential of the enterprise and the republic as a whole.
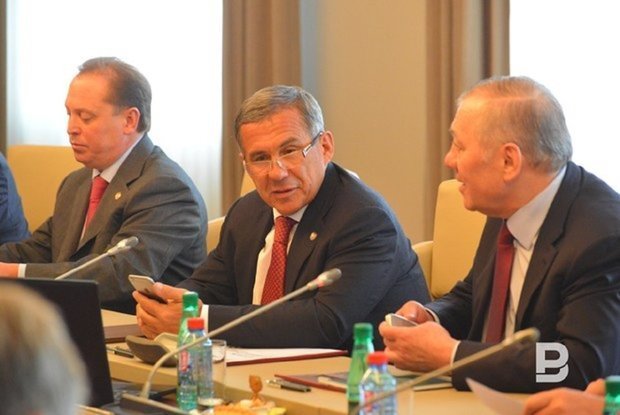
“This is a very complex, but very promising project. To the extent that it is implemented at TAIF-NK, it can be a revolution in the processing of heavy residues," he stressed.
The revolution in the field of oil refining was accomplished thanks to the high professionalism of Albert Shigabutdinov's team, his unshakable faith in a successful result.
First stopping major repair showed the correctness of the decisions made
“According to the data published on the results of the activities of the Russian oil refining complex in 2021 in the directory 'Info TEK — Consult' 'Oil refining, gas processing and petrochemistry in the Russian Federation', TAIF-NK JSC ranks first among all Russian refineries in terms of 'Output of light petroleum products', with a figure of 80,7%. For the period from January to August 2022 inclusive, this indicator reached 90%, and according to the results of work directly in August — more than 93%. For comparison: the average output of light oil products in the Russian Federation is slightly more than 62%. Believe me, every percentage in this rating is a huge effort. In the same directory, our company ranks second in terms of the complexity of the technological scheme, according to the Nelson index. This indicator is equal to 11,32 with an average value in the Russian Federation of less than six. In terms of technological efficiency of oil refining, we are leaders not only in Russia, but also, without false modesty, in the world. These results have been achieved thanks to the decision taken in 2011 by the management and shareholders of JSC TAIF on the construction of the VCC unit and its further modernisation in the conditions of TAIF-NK JSC. Processes like ours are the future of oil refining," Aleksey Khramov is sure.
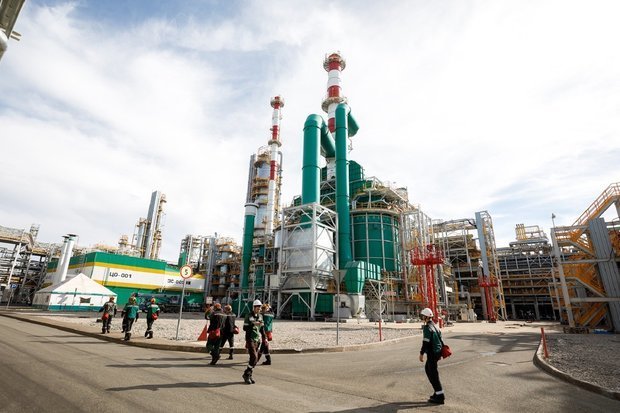
At the same time, the company notes that the complexity and uniqueness of the technology imposes a special responsibility in making decisions about the choice of components and parts, protective anti-erosion coatings of the main and auxiliary equipment and many other tasks that come down to a single denominator: ensuring the safety of operation. The first full-scale stopping major repair has been completed at the complex. For the HRCC specialists, these are not only tasks for routine inspection and repair of production equipment, but also a great opportunity to carefully go through all the points of the huge Complex and evaluate the effectiveness of previously made decisions.
“For us, such a big, full stopping major repair is the first when we try to assess how everything worked. There are separate production facilities, such as the hydrogen plant, sulphur production plant, fractionation, where technologies have been tested for a long time, and experienced people who had previously worked at similar units were recruited for these units. There we know where to look, what to check, where to move. And for the main production — VCC, really a lot of unknown was there. Some of the issues require our slightly closer attention in the future: increasing the number of inspections, revisions. This is mainly due to the environment in which we work: there is a fairly aggressive environment that can cause damage to equipment, pipelines, and it is these points that we need to pay attention to in the future. Currently, we have not found anything so supercritical — everything works as it should," said Artur Urazaykin, the chief engineer of the HRCC.
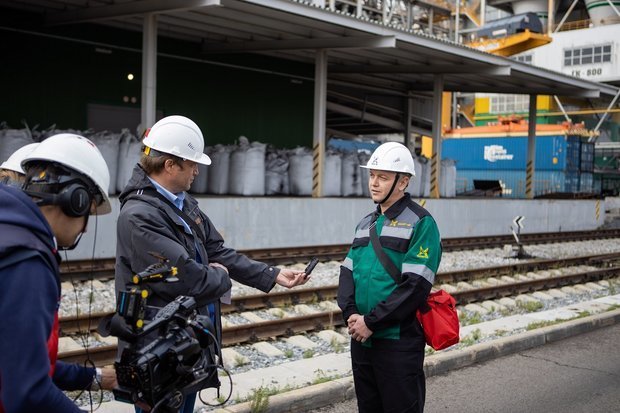
“It can be concluded that all the main technological equipment performs its function provided for in the technological chain and is also in good technological condition and suitable for further operation," Maksim Gritsenko, the deputy director of the HRCC for production, said in the interview with Realnoe Vremya. Behind the dry statement of fact — confirmation: all those modernisations, improvements, developments that were implemented here during the entire period of the formation of production are true. The most difficult, hard work of scientists, their own specialists, companies and organisations involved, innovations and solutions implemented in production are justified.
Improvement processes are endless
Everyone at TAIF-NK is sure of this. Even the young production such as the Heavy Residue Convertion Complex continues its development. Including in the direction of import substitution in a whole range of directions:
“We have big Russia and we have resources. We just need to find the right, competent supplier, work out all the nuances with him, which we do. And we started this work a long time ago. Now the names of the companies are determined, there is someone to work with. Yes, it will take some time to improve the quality. This is in terms of the same additives, catalysts. But there are proposals," Maksim Novikov is sure.
In particular, the same activated lignite used in liquid-phase reactors with a suspended additive.
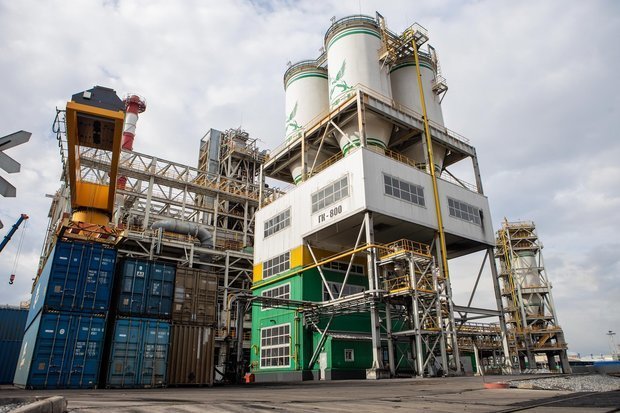
“This suspension layer is created by the special coal additive, which is delivered to us in specialised containers, from which the additive is discharged using a special system and fed into the reactor unit, where thermal cracking occurs at hydrogen pressure and temperature — that is, the splitting of tar into light petroleum products. Previously, its supplies were imported from Germany. Currently, the company's specialists, together with specialists of Russian companies working in the coal mining industry, are selecting the technology to obtain a coal additive of the necessary quality to ensure our production," Maksim Gritsenko, the deputy director of the HRCC for production, shared with the journalist of Realnoe Vremya.
The work on issues of maintenance and repair of equipment, supplies of spare parts, assemblies and parts has also been underway for a long time.
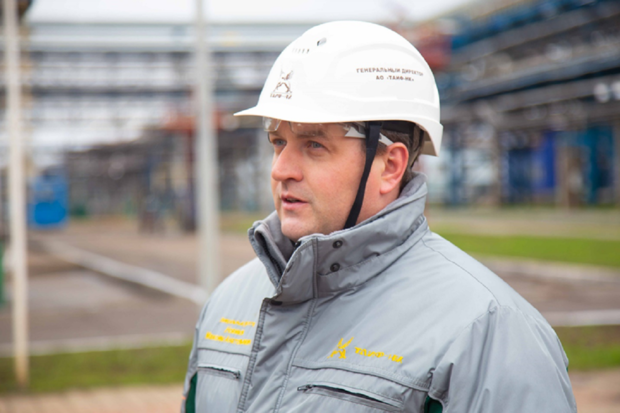
“We understand that imports are always at risk, and the domestic engineering industry is actively developing and is capable of much. We were looking for reliable and qualified performers of the services we needed. The governments of Tatarstan and Russia actively help the domestic industry in this. We are talking, among other things, about signing acts on the admission of the possibility of using analogues to original spare parts and components. And with regard to the supply of compressors, pumps, furnace equipment — there are organisations in Russia that can successfully cope with this task. We know the suppliers, we have built relationships with them, and we work with them. At the same time, clearly realising that the fuel and energy sector requires a special approach to security issues, our approach to finding and choosing analogues is very careful and comprehensively thought out," said the director general of TAIF-NK JSC.
To the journalist's question about when it would be possible to say that both the HRCC and TAIF-NK as a whole achieved all the tasks set and now you can just work “on the thumb”, the CEO of one of the leading oil refining companies in Russia answered briefly:
“Never. The world is moving, new technologies are emerging, new materials are needed. I've been working at the company for 23 years, and I don't remember a single year when it was quiet — in the sense that we did everything we could — launched, adjusted the mode and just watch. Every year is something different from the others: new units, new launches, new products. I think that in the manner typical of TAIF, we will continue to develop for the benefit of the republic and Russia.”
Подписывайтесь на телеграм-канал, группу «ВКонтакте» и страницу в «Одноклассниках» «Реального времени». Ежедневные видео на Rutube и «Дзене».