Alexander Shadrikov: ‘Over 6 years, Tatarstan enterprises have invested 35.6bn rubles in the environment’
What is the money being spent on and what real results have been achieved — on the example of one of the leaders of Russian oil refining
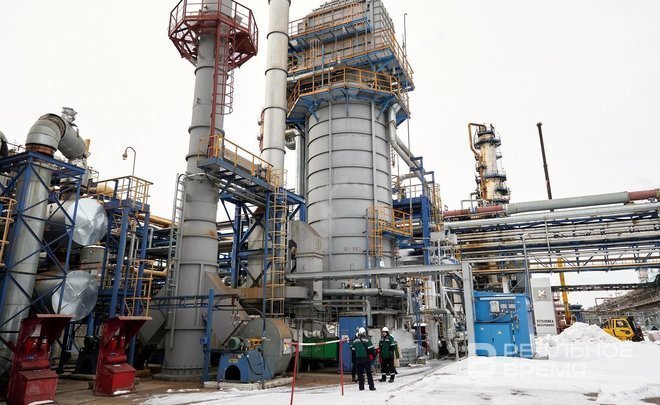
Minister of Ecology and Natural Resources of Tatarstan Alexander Shadrikov has recently visited the online studio of Realnoe Vremya. According to him, over the past 30 years, the gross regional product of the republic has grown almost 3 times. At the same time, the volume of negative emissions has decreased by a quarter. The volume of greenhouse gases entering the atmosphere has decreased by almost 13%, and their absorption has increased by more than 14%. The industrial enterprises of the region are active participants in the processes to reduce the negative impact on the environment: over the past 6 years alone, they have invested more than 35 billion rubles in environmental programmes. A Realnoe Vremya journalist visited the production sites of TAIF-NK JSC to personally see and hear from their example, thereby reducing the burden on nature.
Decarbonisation
In early December 2023, in Tatarstan, the issue of climate agenda and plans for decarbonisation of the Republic of Tatarstan was discussed in the format of a meeting of the interdepartmental working group.
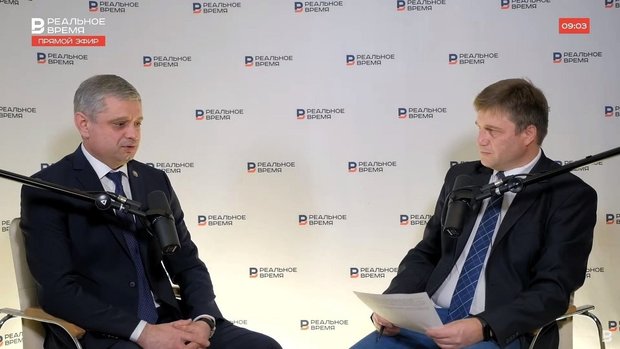
As Alexander Shadrikov, Minister of Ecology and Natural Resources of Tatarstan, noted in the online broadcast of Realnoe Vremya, considerable attention is paid to monitoring the state of atmospheric air:
“Sixteen of our stations are operating, and nine more monitoring stations are opening enterprises for us.
The first such station on the territory of the oil refining company was launched in 2021.
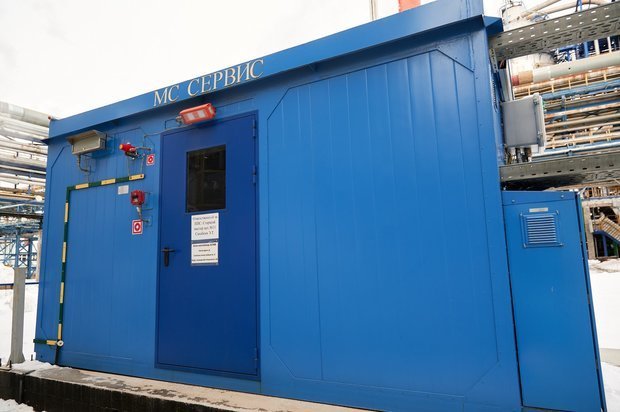
“We have installed an automated emission monitoring system — it is a comprehensive system. It is installed on the chimney of the process furnace. So far, this is the only such system for the entire enterprise, however, full coverage of production is planned in the foreseeable future. We have developed a plan, and the design documentation for all technological furnaces is ready. In 2024, we plan to equip two furnaces at once at the HRCC and then, within a few years, we will equip the rest of the production facilities. The cost of one post is around 45 million rubles, and only nine are needed," Anton Nikolaev, the deputy chief engineer of TAIF-NK JSC, explained to the journalist.
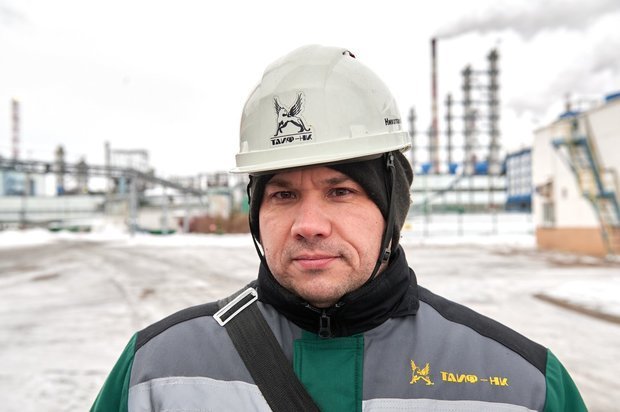
The same gases that enter the chimney are supplied through special pipes to the sensors and controllers of the monitoring station. Emissions, in full compliance with the requirements of federal legislation, are monitored and analysed online, which makes it possible to respond promptly to any deviations.
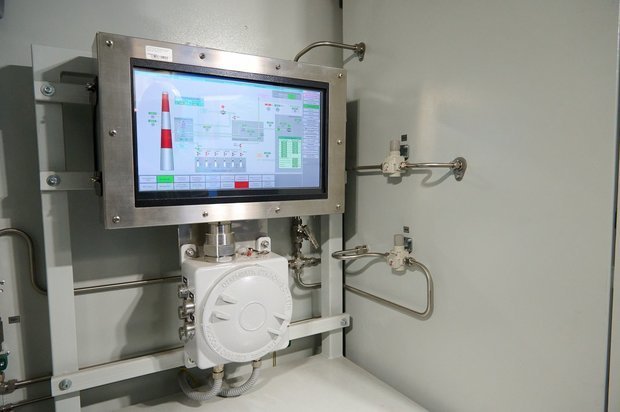
Soon, the measurement data will go directly to the Ministry of Ecology of the republic, to Rosprirodnadzor, and will be available on their websites to everyone. At the same time, there is already a significant reduction in the content of harmful substances.
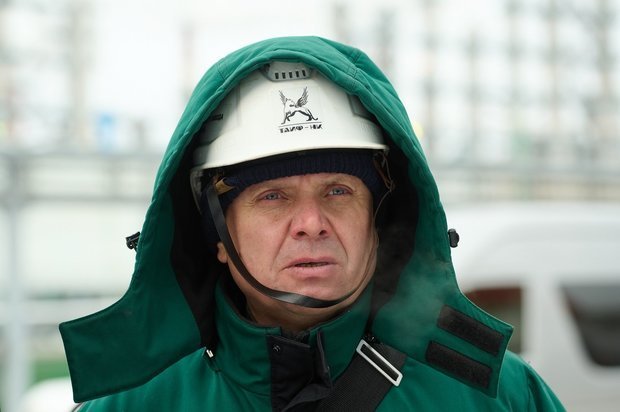
“In general, according to the initial design, the combined burners on our furnaces were designed to run on fuel oil and natural gas. We abandoned the burning of fuel oil about 15 years ago and switched only to natural gas. However, during the production process at our gasoline plant, our own so-called waste dry gases are formed, which were burned on flares. This was a problem, complaints were received from the population, and we started this gas in the furnace. Not so long ago, hydrogen-containing gas was also sent to our burners from the HRCC. As a result, we do not use fuel oil at all, natural gas is mainly used only for kindling and in much smaller volumes than before, and dry gas from production, instead of burning on flares, brings benefit by heating the product. These furnaces “grind” everything, and judging by that only steam comes out of the pipe, they “grind” well. This is both ecology and economy," explained Vladimir Lakhomov, the director of the Refinery.
More about gases
Gas for furnaces is supplied from the HRCC to the Refinery, and acid gas is supplied in the opposite direction and through another system. The very hydrogen sulphide from which sulphur is then extracted.
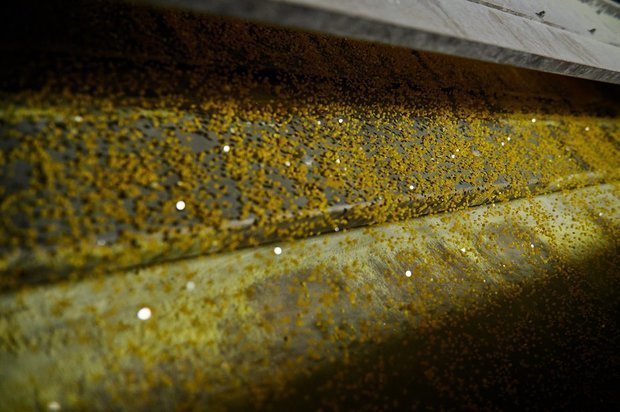
“A unit with a large margin of capacity and processing has been built there. Therefore, in the future, it is planned to preserve the installation of the refinery workshop No. 05 and convert it to the production of another type of product. That is, we also plan to expand the nomenclature," Anton Nikolaev told the journalist.
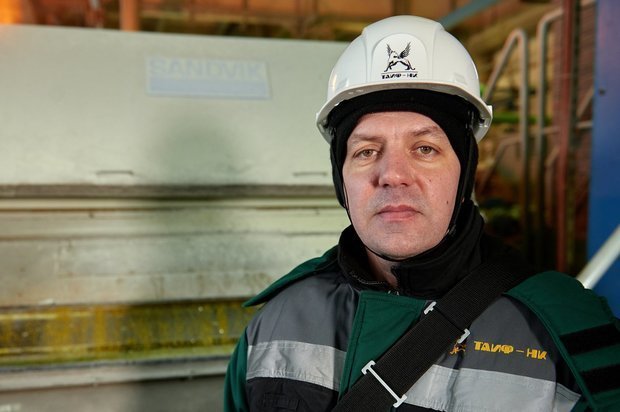
In fact, there is a choice of technology for even deeper processing of the obtained raw materials, explained Andrey Moiseev, the head of the workshop for the production of elemental sulphur.
“Where any product is hydrotreated: gasoline, kerosene, diesel fuel, hydrogen sulphide is released in large quantities. The hydrotreating plant itself entails the installation of a sulphur production plant nearby. For the flexibility of production, that is, to increase the service interval of the unit, we have redistributed the flows of acid gas. For large-scale production, several identical lines are needed. At the moment, we have three of them: in order to be able to redirect the flow of raw materials without stopping production. The conversion rate of our unit today is 99.5%. All extracted sulphur is becoming a sought-after product that goes to a wide range of consumers: tyre industry, agriculture, including for the creation of fertilisers. We are currently considering the issue of upgrading the unit for the independent production of more marginal products that will be obtained from sulphur," said Andrey Moiseev. The one that is extracted from hydrocarbon raw materials and which, if it remained in the product, would become a serious polluting component of the exhaust of cars, airplanes, and other equipment.
Eliminating the evaporation of hydrocarbons
This is another area that the company is closely involved in. Quite closely, by the way — in the truest sense of the word.
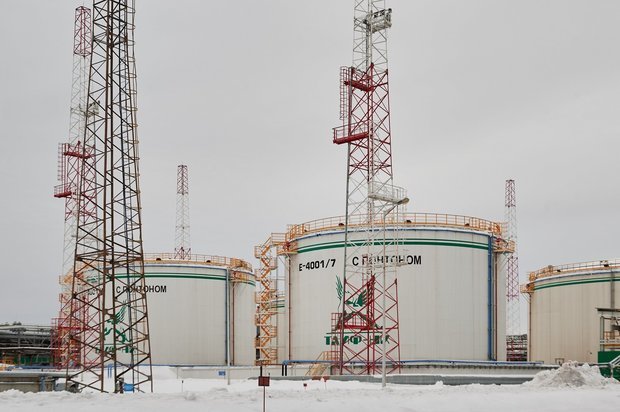
“At the Gasoline Plant, we replaced the pontoons on the tanks. This is necessary to exclude the evaporation of hydrocarbons into the atmosphere through vent valves," the deputy chief engineer of the company said about the work done not so long ago.
The pontoons on the tanks are a roof under the roof. A kind of “piston” that blocks the possibility for vapors to break free.
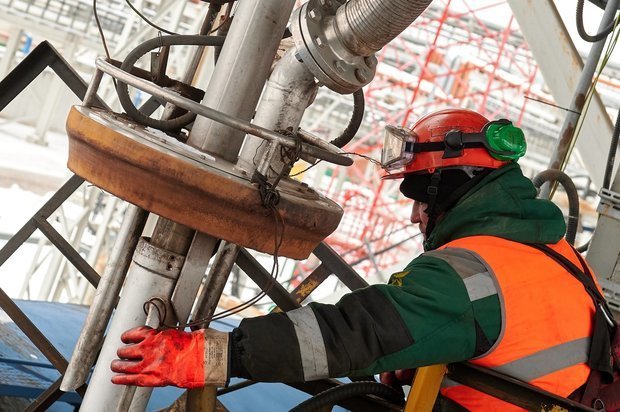
A similar system has been implemented on the loading rack, where light petroleum products (gasoline/naphtha) are shipped.
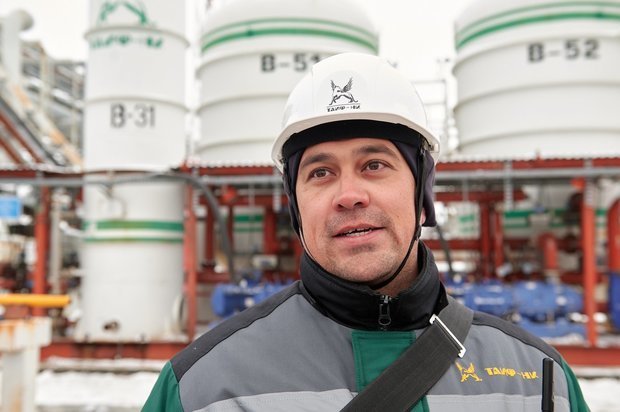
“As part of the technical re-equipment, the loading rack was retrofitted with filling devices with sealed lids, and a steam recovery unit was installed. The product that is shipped to the loading racks is highly volatile, this is due to the high pressure of saturated gasoline/naphtha vapors, and therefore, in order to eliminate emissions into the atmosphere, a sealed filling with vapor removal for recovery has been implemented. The content of the discharged hydrocarbons is 90-95% of the vapor-air mixture, the rest is the air mass. In this unit, the main equipment is adsorbers, which are loaded with activated carbon. Volatile hydrocarbons contained in the vapor-air mixture are trapped on the surface of the coal, which condense and return to the closed system of the tank farm. Regular sampling of the air mass discharged to the candle reflects the actual absence of hydrocarbons, which is an indicator of the effective operation of this unit — Marat Valishin, the head of the seventh workshop of the refinery, proudly spoke about the achievements.
100% water saving
Another reason for the company's pride is the closed circuit of the circulating water supply. According to the company, over 7 years, more than 12 million cubic metres of river water have been saved here.
“Our water resources are almost completely absent from the outside. The water that has entered the sewer enters our treatment facilities, is put in order and is fed back to the water circulation units. The economy of water resources is almost 100%," Ruslan Valiev, the head of the Environmental Protection Department, shared in an interview.
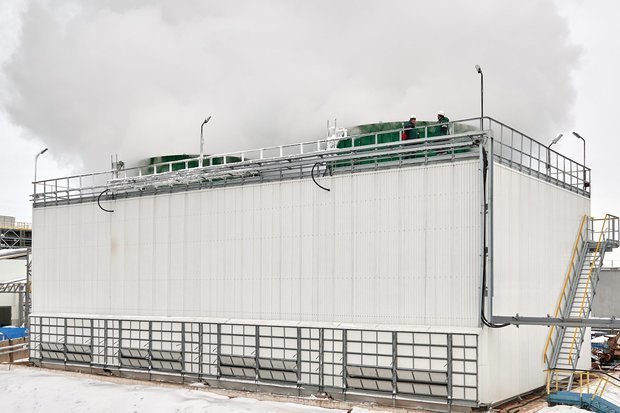
It is this water that is supplied to the brand-new cooling tower, installed in the autumn of this year — during the overhaul maintenance. The cooling tower itself, barely put into operation, already works on the issues of economy and ecology.
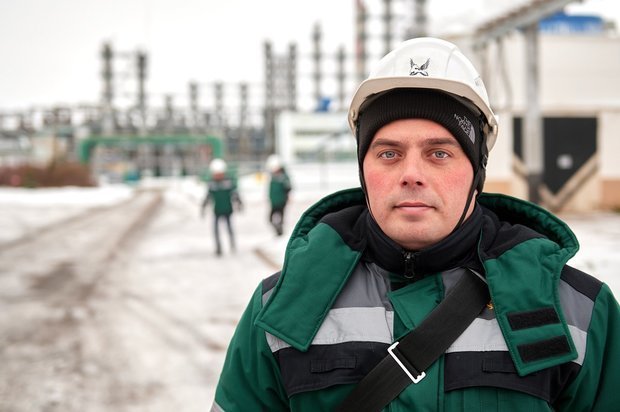
“The unit is completely domestic. Moreover, everything, including metal structures, was made in Tatarstan. When equipping the cooling tower, the drops separators of the irrigation system were also replaced, which reduced the consumption of its own purified water by 10-15%. Plus, the efficiency of our cooling tower has increased," said Ramil Nurullin, the deputy chief power engineer of the company.
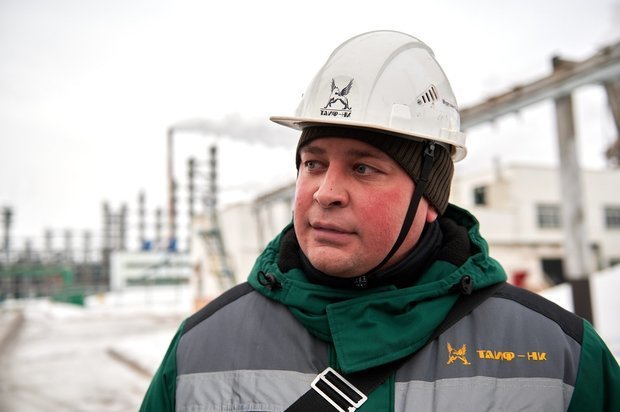
Local wastewater treatment plants are also ultramodern. Commissioned in 2017, they ensure the removal of 99.99% of petroleum products and other pollutants from incoming water. Local sewage plants are fully automated and capable of pumping up to 500 cubic metres of water per hour through a multistage system. In October of this year, the facility received a comprehensive environmental permit (CEP). That is, they fully comply with the environmental requirements of the Russian Federation.
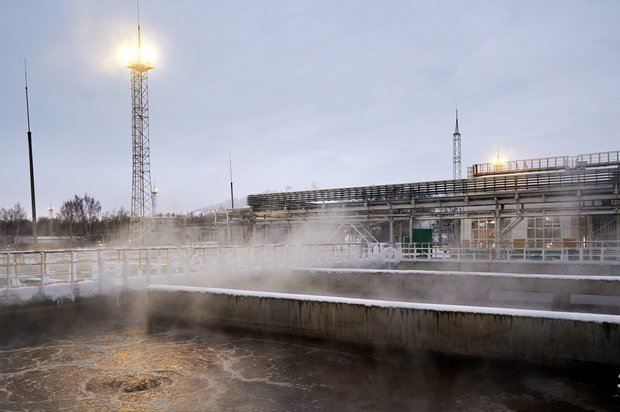
Waste or raw materials?
Tar, fuel oil, vacuum gas oil: all these are dark petroleum products, which are often even cheaper than the oil from which they are obtained. Refiners call them low-margin products, and even problematic from an environmental point of view. It was easier to sell such thing, albeit at a discount, than to solve the issue of recycling.
More precisely, this was the case until recently, when it was not possible to achieve success with the commissioning of the Heavy Residue Conversion Complex.
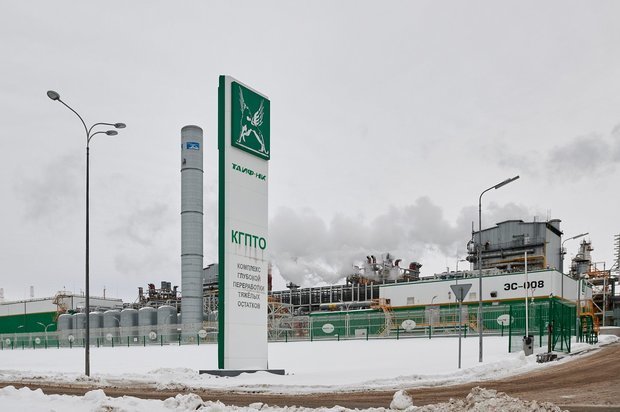
“With the appearance of our complex, we process these residues into valuable light petroleum products. In addition to the economic effect, there is also an environmental effect," Maxim Gritsenko, the deputy director of the HRCC for production, is sure.
As of October 2023, the selection of light petroleum products at the enterprise exceeded 88%, and in some months did not fall below the bar of 90%. The ultimate goal is to achieve 98% extraction of light petroleum products from each ton of oil received for refining.
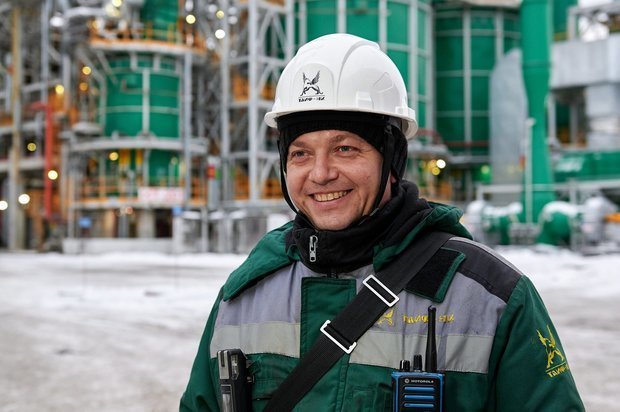
Not so long ago, hydrogen-containing circulating gas burned uselessly from production. After the system was updated, it went straight to the flare. Today, the situation is different.
“We send it to a specialised membrane hydrogen extraction plant. Operating due to the difference in pressure and molecular weight of substances, it separates pure hydrogen with a purity of up to 99% and fuel gas. Hydrogen is returned to the production process, and the fuel gas is sent as fuel to the CHP and to the furnaces," Maxim Gritsenko said about another environmental solution.
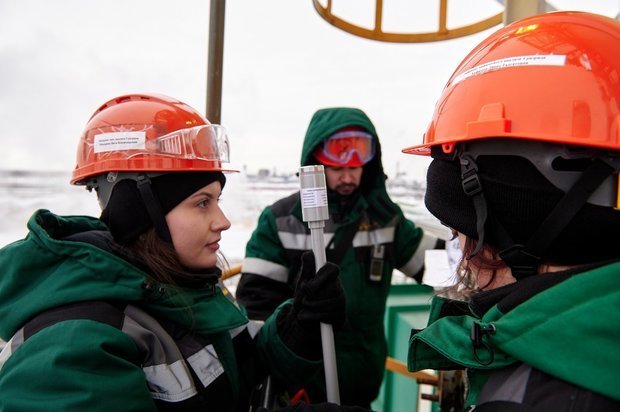
Control over compliance with environmental impact standards at this production facility, as well as at any other within the company, is the strictest:
“Daily measurements of the air environment are carried out from stationary sources of atmospheric pollution, on the border of the sanitary protection zone, in general, on the entire industrial site. Our laboratory is also accredited for the analysis of wastewater entering our local wastewater treatment plants at Nizhnekamskneftekhim BTS. According to a special schedule, laboratory technicians go to the control sites and make measurements. Some of the analyses are processed on-site by express methods, and the part where it is necessary to use a chromatograph and other equipment available to the company goes to the laboratory," Ruslan Valiev explained.
Dozens of measurements are taken daily.
Everything has its place
The saying is also relevant for waste. All workshops at each production facility have their own storage areas for waste of various types and hazard classes. For rags, cardboard, and other non-hazardous waste, closed containers are sufficient. Separate locations are equipped for waste of hazard classes I—II.
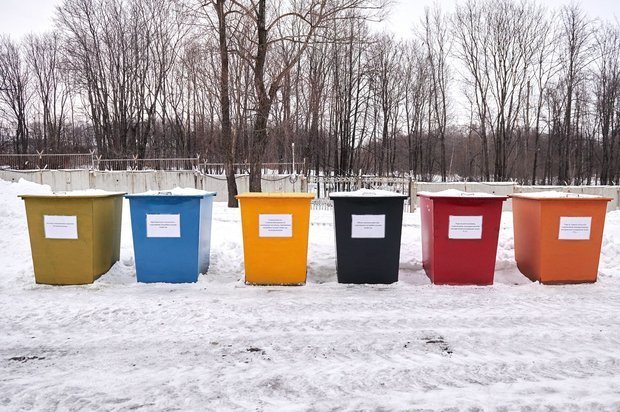
“This is about 27 types of waste, which includes batteries, mercury lamps, thermometers, various acids that are formed in laboratories. For their separate accumulation, we have equipped about 25 places as close as possible to the places where such waste is generated. On March 1, 2022, a new waste management system of hazard classes I—II was launched. From the very first days, we have worked closely with the federal environmental operator — we have registered in the system and signed a contract. As we accumulate waste, we issue an application, and they are taken away for disposal or neutralisation," Alyona Mukharnikova, an environmental protection engineer, conducted a short tour.
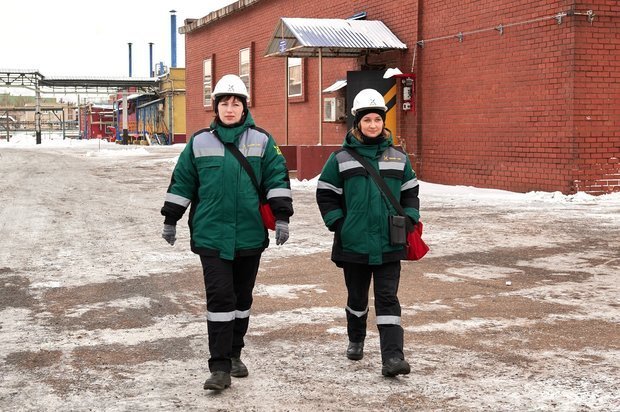
“Waste is mainly transferred to specialised organisations for disposal. Subsequent disposal, or, in other words, waste recycling, gives the opportunity to solve several environmental problems at once: the first is to reduce the share of consumption of natural resources. In some cases, production technologies at the expense of recyclables make it possible to almost completely abandon the use of clean materials. The second is to reduce the proportion of volumes to be placed on landfills. And this helps to reduce the burden on the environment. We have a strict control over the activities of contractors in the field of waste management. Even at the stage of procurement procedures, we check whether they have a license to handle each type of waste. Besides, contractors sign a mandatory annex to the waste transfer agreement, in which they commit to comply with environmental protection requirements," Olga Sashinskaya, a leading environmental engineer, added to her colleague.
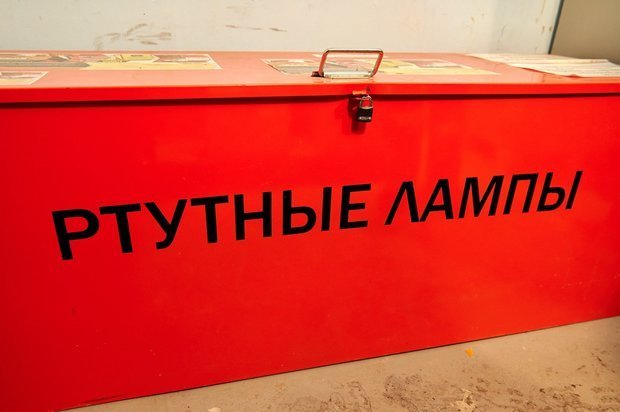
The improvement of implemented solutions and work on new ones to ensure even more careful attitude to the environment, as the company assured, are constant here. Besides, production staff are regular participants in actions to restore order in various territories in Nizhnekamsk, they regularly plant trees and shrubs and also support youth environmental contests.
Подписывайтесь на телеграм-канал, группу «ВКонтакте» и страницу в «Одноклассниках» «Реального времени». Ежедневные видео на Rutube и «Дзене».