TAIF-NK refinery: from naphtha and mazut to Euro 5
Realnoe Vremya continues a series of publications on the formation and stages of development of the oil and gas processing industry in Tatarstan: part two
In 1979, the new primary oil refining plant produced teh first products at the site of Nizhnekamskneftekhim. It, actually consisting of a single unit of ELOU AVT-7, at that time had the main task to supply straight-run gasoline to the ethylene plant. The co-product — mazut — served as fuel for the Nizhnekamsk CHPP. But exactly this moment can be considered the starting point of the formation of oil refining in Tatarstan. About what processes took place in the production over the following four decades, how the transformation of the raw materials shop into one of the leading industrial productions in Russia took place, and what the product range of the refinery is today — one of the components of TAIF-NK complex — read in the material of Realnoe Vremya.
3 branches of one complex
TAIF-NK JSC today is a large modern oil refining complex, one of the leading industrial productions in Russia. The company includes three interrelated plants:
- Oil Refinery with a design capacity of 7,3 million tonnes of refined oil a year;
- Gasoline Plant with the gasoline production unit based on catalytic cracking with a design capacity of 1 million tonnes of raw materials a year and the natural gas liquids processing unit with a design capacity of 1 million tonnes of raw materials a year;
- Heavy Residue Convertion Complex (HRCC) with a design capacity of 3,6 million tonnes for processing tar and vacuum gas oil.
We will tell you in detail about what the Gasoline Plant is today and what is the uniqueness of the only HRCC in the world at the moment, working on Veba Combi Cracking (VCC) technology, in the following parts of the series. This one will be devoted to the stages of formation and products produced by the refinery.
Extensive work has been done
We have already written about the reasons for creating own oil and gas processing in Tatarstan and the initial stage of the development of the industry in the republic. In 1997, when TAIF leased ELOU AVT-7 from Nizhnekamskneftekhim, the unit, which was worn out by that time, was not loaded even half of the design capacity: 2,5 million tonnes of oil a year instead of the possible 6 million tonnes. After only a year, the unit was already working at maximum load, and TAIF set new tasks for the young company TAIF-NK.
“The management decided to create a full cycle of the oil and gas processing plant. Initially, all these sites and production facilities were not designed for further modernisation. They were built as part of the single chemical plant complex. The designers had to do their best to ensure that the unit was overgrown with a complex of related, complementary and deepening productions: hydrotreating of middle distillates, visbreaking.
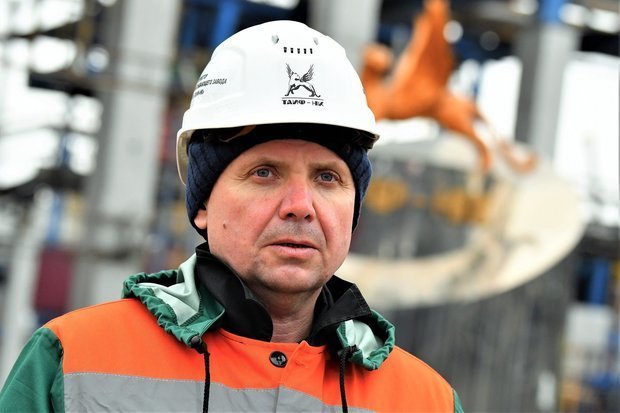
In parallel, the Bitumen Plant was built, commodity storages were expanded. An extensive work was carried out to make a huge plant from one shop with today's assortment of manufactured petroleum products, said Vladimir Lakhomov, the director of TAIF-NK JSC refinery.
Vladimir Lakhomov joined the company in August 2000 and began his career as an operator of waste heat boilers of the ELOU AVT unit. Most of the innovations took place either before his eyes or with his direct participation.
Maksim Novikov, the director general of the complex, also got a job at TAIF-NK a year earlier. Moreover, also at the refinery.
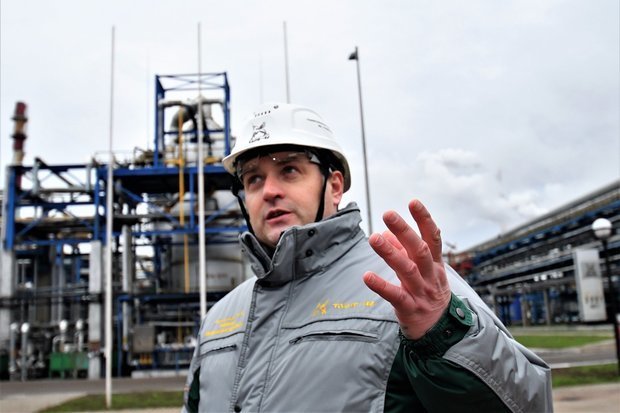
“In principle, my entire formation took place at the TAIF-NK oil refinery. Here I learned what operation is, and what reconstruction, modernisation, technical re-equipment and so on are. My path at the refinery began as a process unit operator in 1999. I came here as an operator of waste heat boilers. Then I grew professionally step by step: I worked as a shift supervisor, deputy head of the workshop, deputy chief engineer, 5 years as chief engineer, and then the path led to the management of TAIF-NK," says Maksim Novikov.
In the interests of the republic
As Albert Shigabutdinov, the director general of TAIF UK JSC, repeatedly emphasised in his interviews, multibillion-dollar investments in the development of Tatarstan's oil refining pursued not only the commercial interest of the company itself but were also designed to give a new impetus to the economy of Tatarstan.
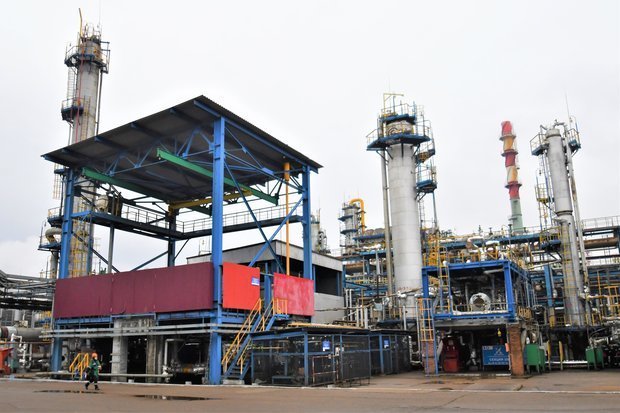
The company started large-scale construction from the first days of its activity. In 1999, the visbreaking unit was put into operation, which allowed to start the processing of tar, a co-product of ELOU-AVT-7. In 2002, the kerosene and diesel fuel production plant was put into operation. In January 2003 — the unit of sulphur extraction Klaus with a granulation unit.
If in 1995 the convertion rate of oil refining at the refinery barely exceeded 36%, by 2005 it had increased to almost 68%. Meanwhile, TAIF-NK have been closely engaged in further modernisation and development of the refinery. These processes have not stopped for a day to this day.
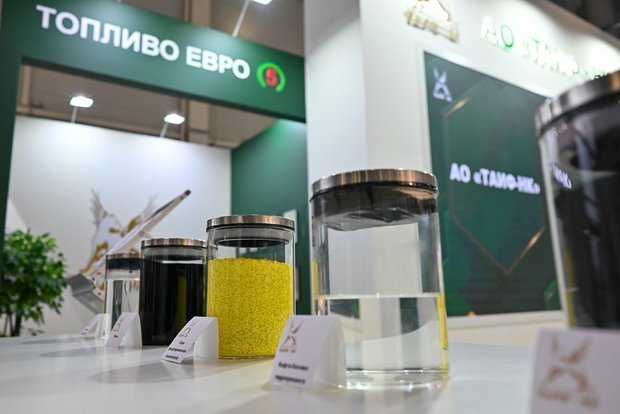
In 2007-2009, during the reconstruction and modernisation of the unit, the efficiency of the ELOU AVT-7 furnaces was increased and the thermal exchange circuit was changed. Besides, the replacement of mazut burned in the furnaces with gas was provided, which significantly increased the environmental friendliness of the unit. The reconstruction of the refinery's middle distillate hydrotreating plant, carried out in 2008 jointly with Criterion Catalyst Co Ltd (UK), made it possible to increase the volume of hydrotreating catalyst by 10% and completely replace the catalytic system. After that, TAIF-NK had the opportunity to produce diesel fuel of Euro 4 standard.
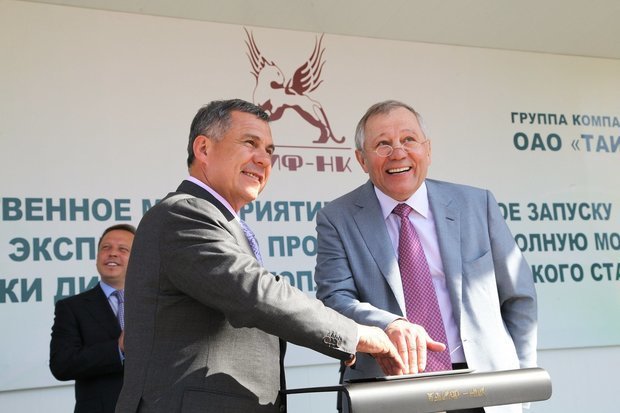
Almost immediately, but with the joint efforts of Shell Global Solutions International B.V. (the Netherlands) and Criterion Catalyst Co Ltd (Great Britain), further modernisation of the plant began to increase its raw material capacity by another third and switch to the production of Euro 5 diesel fuel. In June 2012, it was put into operation. TAIF-NK was the first in Russia to completely switch its production facilities to the production of diesel fuel that meets the most stringent international standards.
In August 2012, then Russian Energy Minister Alexander Novak visited Nizhnekamsk, accompanied by Tatarstan President Rustam Minnikhanov and the leadership of TAIF Group. One of the first productions he visited was the oil refinery of TAIF-NK JSC.
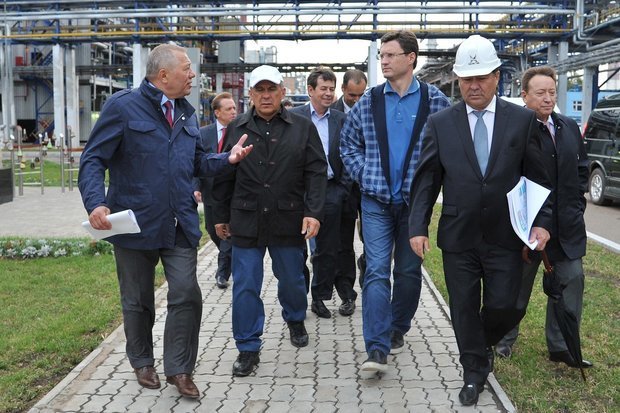
By 2013, the refinery stopped producing high-sulphur marine low-viscosity fuel. The released volumes of middle distillates were redirected for processing into high-quality light oil products.
In 2015, the refinery obtained all necessary permits for the start of commercial production of the new brand of fuel for jet aircraft engines TS-1, intended for civil aircraft.
In the same 2015 year, the unit for the production of polymer-bitumen binders with the inclusion of high-quality thermoplastics of domestic production was commissioned at TAIF-NK. The capacity of the unit is 17 tonnes of products an hour. Polymer-bitumen binders can significantly improve the quality and durability of the roadway due to that they reliably bind inert materials, maintaining elasticity both at significant plus temperatures on the street and in winter frosts, preventing the destruction of highways under the influence of natural cycles.
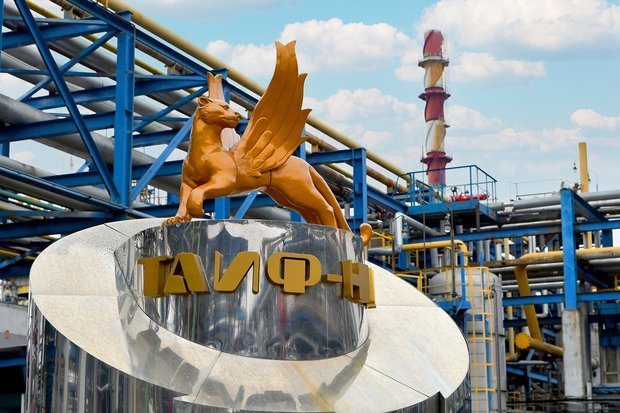
In 2016, ahead of the deadlines set at the state level, the company established the production of road bitumen that meets the requirements of GOST of the Russian Federation and the standards of the member countries of the Eurasian Customs Union. It is important that the improvement of the quality of existing and the organisation of production of new brands of road bitumen at TAIF-NK is in close cooperation with the development of the road transport complex of the Republic of Tatarstan.
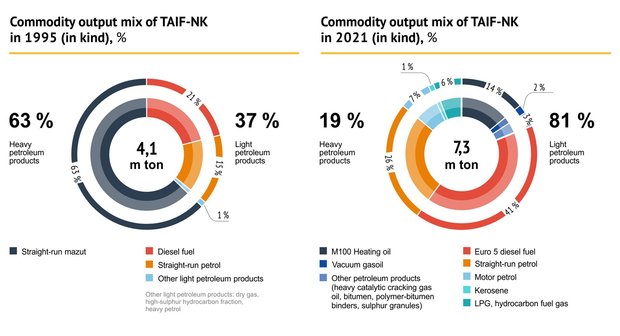
To date, the range of products produced by the productions of TAIF-NK JSC exceeds 50 items. From 1997, when the only oil refining unit at that time, ELOU AVT-7, was leased, which became the centre and basis for the development of the future refinery, the production volumes of TAIF-NK JSC of marketable products almost doubled, and the proportions of production of heavy and high-quality light oil products changed dramatically. If in 1995 2/3 of the raw materials were converted into heating oil, today 81% become popular and high-margin products — diesel fuel and Euro 5 standard petrol, straight-run petrol, kerosene, aviation fuel, LPG and hydrocarbon fuel gas. This was made possible, among other things, thanks to the launch of the HRCC into pilot operation, but we will tell about the uniqueness of the HRCC in one of the next parts of the series.
Quality assurance
In 2002, the Central Laboratory of the refinery was organised at the TAIF-NK refinery. The company does not spare money for constant objective quality control of a wide range of products manufactured by the complex: the laboratory is equipped with the latest technology, and its specialists constantly improve their qualifications and master new advanced methods and technologies for conducting analyses.
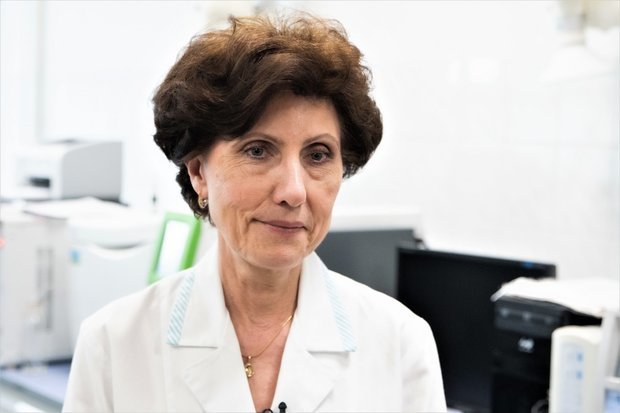
“The laboratory conducts monthly more than 22 thousand tests of petroleum products produced by the complex: diesel fuel, aviation kerosene, bitumen, polymer bitumen binders, granulated sulphur, vacuum gas oil, straight-run petrol, etc. on a whole range of parameters and performance characteristics, confirming their high quality," Margarita Urmanova, the head of the refinery laboratory, explained to the journalist.
The analysis covers all stages of production — from the quality of incoming raw materials (indicators are important for the organisation of technological process — editor's note) to testing the finished product before it is shipped to consumers.
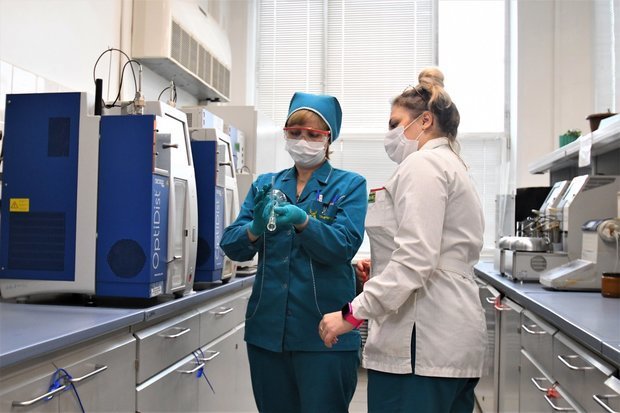
Confirmation of the high quality of the products produced by the refinery is that since 2010 (when the company first took part in the contests "100 Best Goods of Tatarstan” and "100 Best Goods of Russia — editor's note). The products of TAIF-NK are always among the winners of these prestigious competitions.
In 2021, two more awards were added to the gallery of fame of the complex: Euro 6 inter-season diesel fuel became the winner of the All-Russian competition, and PBV-60 polymer-bitumen road binder was awarded the title of diploma winner of the competition "100 Best Goods of Russia” in the nomination “Products of Industrial and Technical Significance”.
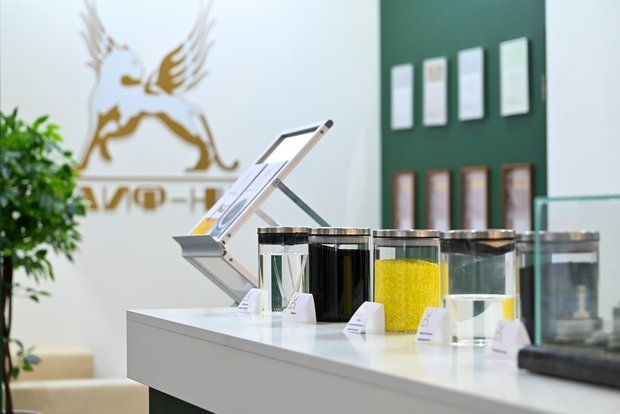
The team and management of TAIF-NK are deservedly proud of their achievements and the entire gallery of awards is presented on the company's website.
To be continued.
Подписывайтесь на телеграм-канал, группу «ВКонтакте» и страницу в «Одноклассниках» «Реального времени». Ежедневные видео на Rutube и «Дзене».