Turnaround maintenance ends at TAIF-NK
More than 500 invited specialists and thousands o its own employees have put key plants of TAIF-NK oil refinery in order in three weeks
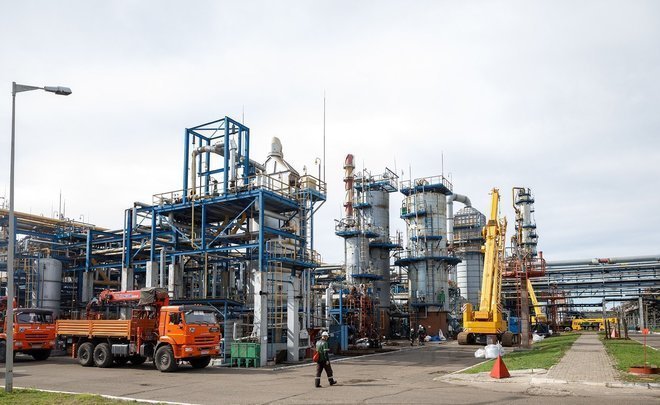
Three plants. More than a thousand pieces of equipment. Just 20 days are given to open, obtain expert evaluation and prepare the huge infrastructure of TAIF-NK JSC into accident-free operation during the next period between the repairs. The job is done both day and night. Now the turnaround maintenance at TAIF-NK oil refinery is almost over. Realnoe Vremya’s journalist saw the final touches are added.
Five expert organisations involved
It is up to experts to understand the state of equipment, evaluate the wear level and the character of repair and restoration works or in general the necessity of replacing entire units right now or next during the same turnaround maintenance.
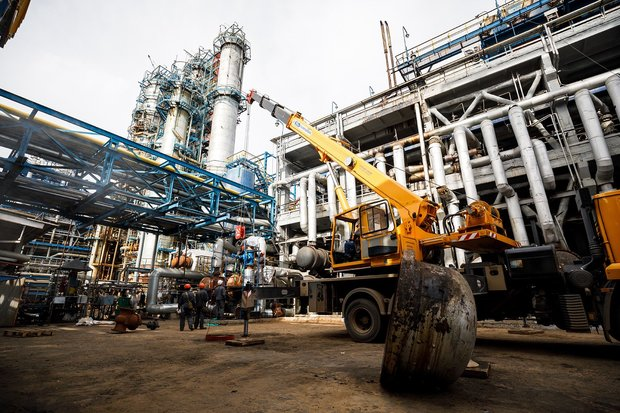
“About five expert organisations from different regions are working here. From Kazan, Ufa, Moscow... It is top specialists. During scheduled work on the inspection of process safety and defining the residual lifetime, technical examinations, they detect deviations and defects that are quickly eliminated,” chief mechanic of TAIF-NK JSC Rustam Bagaviyev explained to the journalist.
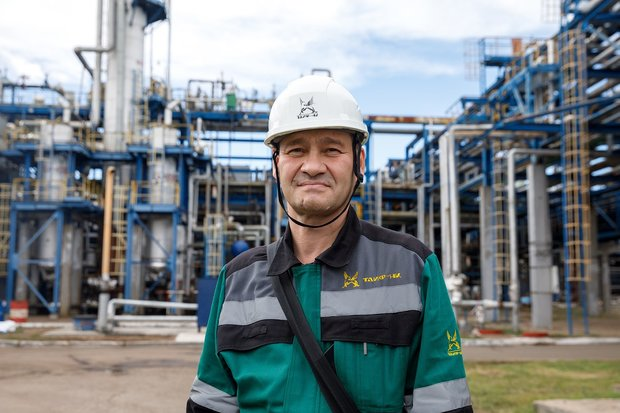
Realnoe Vremya’s journalist caught a representative of one of the expert organisations, engineer and non-destructive testing inspector of the Kazan Engineering Centre for Inspection and Diagnostics Rustam Zaripov examining huge containers in the oil refinery.
“We have been collaborating with TAIF-NK for more than 10 years now. We participate in the inspection of process safety every year. Our task is to examine the equipment, find defects and deliver the information to the management of the factory. And they eliminate them. If defects are found, they are quickly eliminated. Seven people from our organisation are working here now. It is two experts, the rest are non-destructive testing inspectors,” explained Rustam Zaripov.
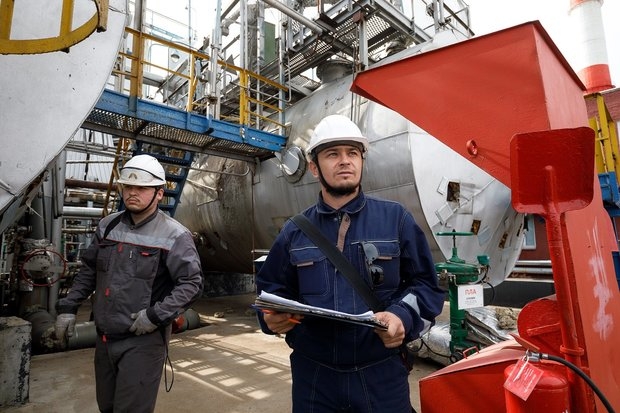
The scale of works in such a short time is surprising: the plants shut down in an established order. And the “countdown timer” is on since then.
“We open about 1,000 pieces of manufacturing equipment in three plants. To open, clean, replace a part of devices, repair is indeed quite a large-scale job. It is done with contractors that amount to up to 500 people,” chief mechanic Rustam Bagaviyev noted.
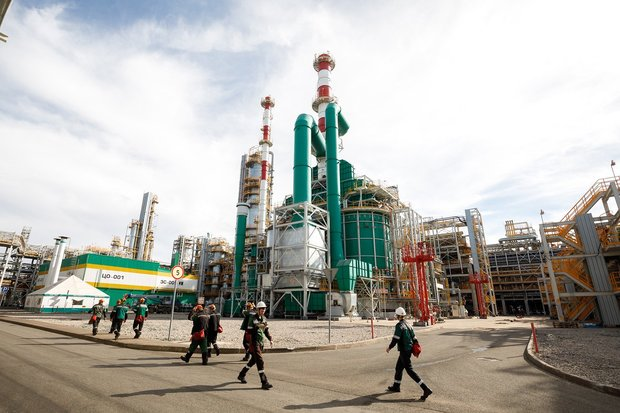
At the same time, information about the equipment wear is collected and tasks for the next maintenance period are set. During the period between the repairs, applications are created and the list of future contractors for specific tasks during the next major repairs is created. This needs to be in advance.
“The case is that September is the most active period in this respect: it is the time of major repairs. A lot of contractors are invited in different plants at the same time. And this includes certain difficulties. But we take advantage of the possibilities of the electronic commerce platform, invite the companies that submit applications. Also, when we are interested in a contractor, we go to the site with him, get acquainted with the equipment, the number of staff... That’s to say, we understand if this organisation can do the tasks it can be trusted within the agreement,” said the chief mechanic of TAIF-NK JSC.
Only treatment facilities didn’t stop in the oil refinery during the repairs
“We have almost completed everything. We are finishing the remaining work. The major repairs always cover full dismantlement, repair and cleaning of almost all the equipment of the main production site. It is the shops No. 1, 2, 3 and 5. Plus, some reservoirs of Shop No. 8, according to the maintenance schedule. Plus, reservoirs of Shop No. 7. Only Shop No. 9 is operating where there is no maintenance, everything is done during the operation. It is treatment facilities. All the other equipment — columns, containers, heat exchangers — everything is dismantled, repaired, cleaned, examined by experts and assembled,” Director of the Oil Refinery of TAIF-NK JSC Vladimir Lakhomov told Realnoe Vremya in an interview.
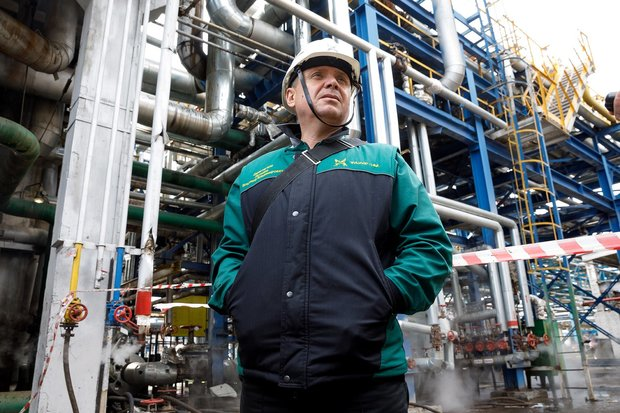
Nowadays we can say only some minor improvements and small clean-up are left. After the major repair is over, quite a lot of “waste” needs to be taken away or, more precisely, recyclable materials. For instance, a nozzle responsible for dividing oil into target fractions was replaced in one of the columns of the first plant of the oil refinery.
“Now the column K-10 is already completed. The nozzle — the part where the mass exchange processes take place — was replaced. If other columns have “dishes,” here there is a nozzle, a net. Liquid goes down, steam goes up. The nozzle is replaced depending on the state. Now we have replaced the second nozzle that was added to the major repair plan last year. We ordered and purchased the nozzle during the period between the repairs. We will replace the third nozzle next year,” the director of the oil refinery explained.
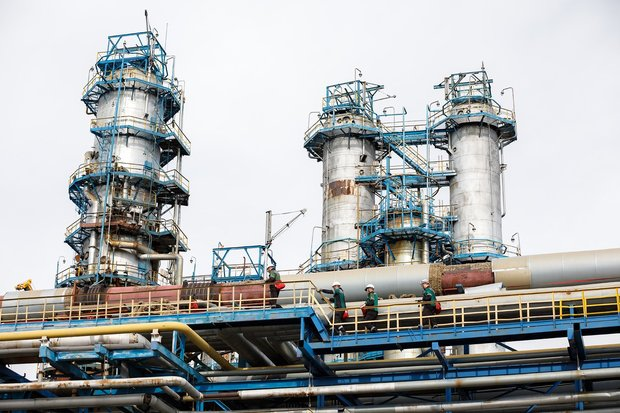
Net residuals will go to special organisations for recycling according to an agreement. Old parts of heat exchangers of air cooling and new elements of the general system for oil and anti-freeze compressors that were replaced, obsolete pieces and other ironworks will also be recycled.
The possibilities of import substitution in repairs, restoration and replacement of equipment are evaluated at the same time with the main major repair works. It is an important issue for Russian enterprises in all the sectors.
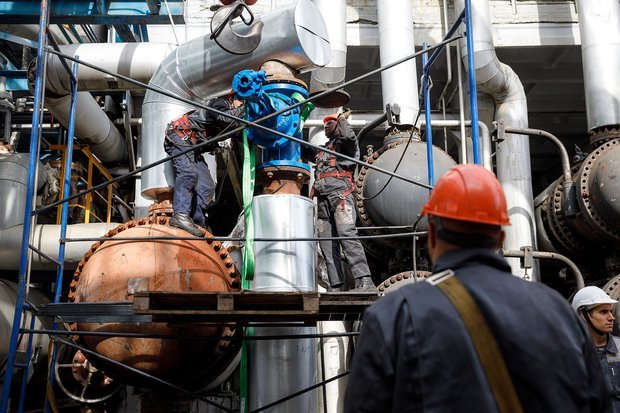
“This year the industry turned out to be in tough conditions: there is a lot of foreign equipment, and nobody has brought original spare parts. Foreign companies from unfriendly countries denied supplies. Moreover, even those spare parts that had already been made and were ready to be shipped. Consequence, we are working with Russian producers. One of the solutions is that the detail that we haven’t been brought but needs to be replaced is designed in a 3D printer. This can be done here, in a neighbouring organisation. They make a draft in a 3D printer, then the spare part can be made according to the draft and installed into the equipment. Also, not all the equipment is iron. Some of its parts — stuffing boxes, elastic ribbons, packing rings — can be made in Russia. We are meeting, drawing, talking. A job is done, the situation is under control,” Vladimir Lakhomov calmed the journalist down.
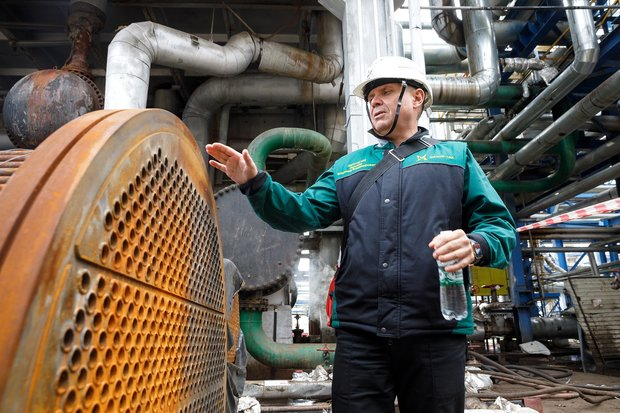
There are more important and difficult issues. For instance, the search for the same contractors for expert and repair works for TAIF-NK.
“The most complicated thing is to become our contractor to do works. There are people who want to, and their number is not small. But our production has the first category of danger, anybody cannot be brought here even for usual works. The territory has a double fence, this speaks volumes. Before signing an agreement, our security service very actively examines contractors,” explained Director of the oil refinery Vladimir Lakhomov.
Specialists of the Centre for Fire Safety from Almetyevsk are one of those who went through the selection. The services the company provides are specific enough: it cleans huge reservoirs designed for feedstock.
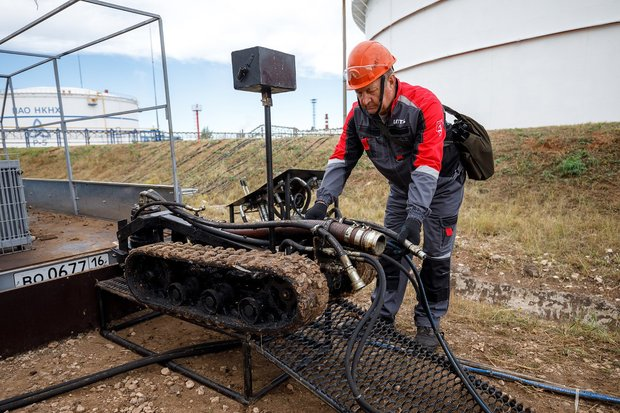
“The oil reservoirs are huge, 67 metres in diameter, 50,000 cubic metres in volume. The heaviest substance goes down and is accumulated during the year. People used to clean the reservoirs: a person in a gas mask with a shovel used to get into the reservoir and other people waited for him at the exit — with wheelbarrows. This is how heavy sediment used to be removed. Everything was primitive. Or the sediment was pumped out. Now a machine does it — a robot that drives inside the reservoir with the help of hydraulics. It has a pump that collects everything from the bottom — water, paraffin deposits, mechanic additives,” Vladimir Lakhomov said.
The collected additives and sediment are pumped into neighbouring reservoirs and then also go to recycling.
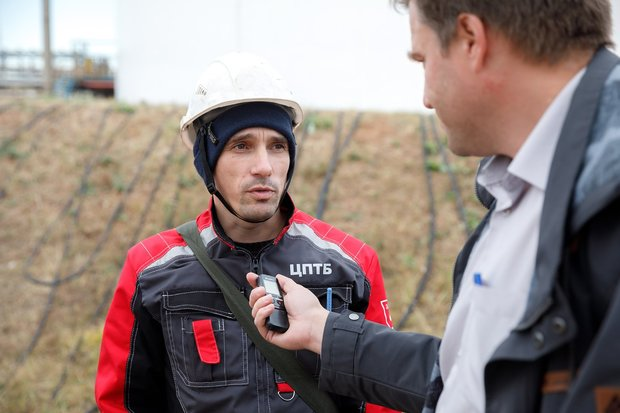
“We created the robot to do works in a confined space, to clean vertical stock tanks. We have been doing this work for a long time. And developments have been made for a long time. Now the samples are mass produced. The tasks and conditions are different: now our robots work with oil companies, in Kazakhstan, in northern regions and here in Tatarstan. And we can create a specific robot for every task. For instance, here a robot created precisely for cleaning the reservoir 50,000 cubic metres in volume worked,” foreman of the contractor Pavel Ryakhov explained. According to the specialist, his company has been fulfilling orders of TAIF-NK for the second year now and intends to develop the cooperation.
First large-scale maintenance
The Oil Pyrolysis Heavy Residues High Conversion Facility has had several major repairs. It had repairs in test mode first, then the equipment had to be stopped, opened, examined, adjusted, replaced during the test mode — since the technology is new enough, and the environment one has to work with is aggressive, and the technology required being improved in real. This is why what was before cannot be named a large-scale major repair. Now things are different.
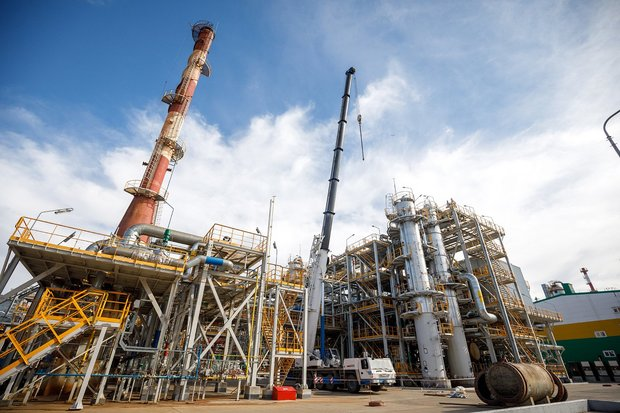
“Indeed, it is our first repair when we stop after a long time of operation according to schedule. Consequently, a lot of experts are involved who are inspecting all the equipment within both state control and our own additional examination,” explained chief engineer of the Oil Pyrolysis Heavy Residues High Conversion Facility Artur Urazaykin.
In general the character of the works doesn’t differ from those done in other plants of the oil refinery: an inspection of heat exchangers, rotating equipment, evaluation of the state and wear level. But there is a difference too, moreover, it is significant.”
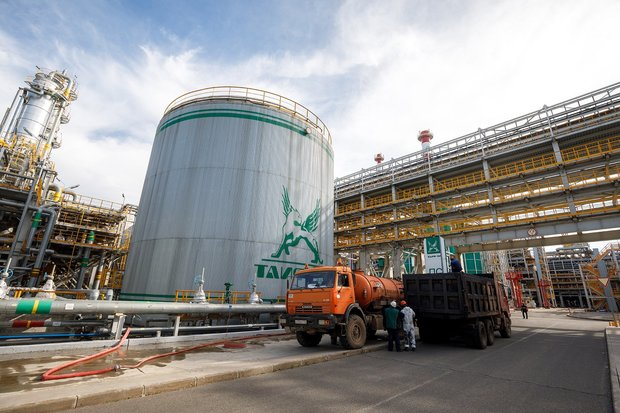
“The technology of all production processes here itself is unique. The environment that appears during the production process and the environment in the equipment and devices, consequently, the approaches required during the examination are unique too. It must be an all encompassing, multi-faceted but non-destructive inspection of all the equipment. Since the technology is new, many things are new for the experts too. Some new methods in the work have to be invented depending on the tasks we set for them. We bought a lot of unique equipment ourselves that allows examining internal parts of devices to see what is happening to the equipment after some time of use. Such equipment is rarely used in our sector.”
Isotope devices belonging to Rosatom are used. In fact, it is an X-ray for equipment that allows seeing what is happening inside. Ordinary measurement devices don’t work in our environment,” Artur Urazaykin told Realnoe Vremya’s journalist.
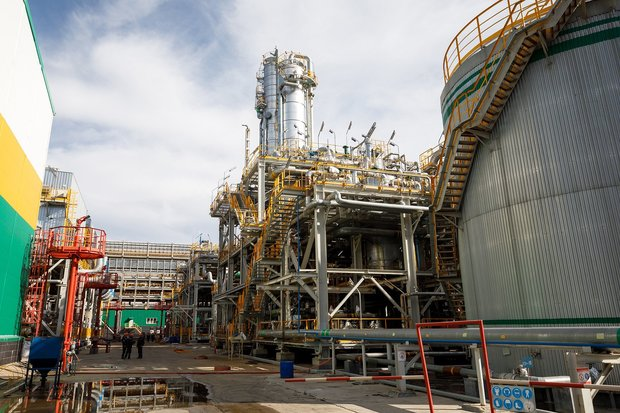
The main VVC reactor was also stopped for maintenance when Realnoe Vremya arrived. This happens twice a year — to clean the equipment and targeted repair of the interior protective surface. Here it is simply impossible to do without human eyes and hands.
“Deliberately trained people in suits with a big visor are working in these devices now, air is delivered via armoured hoses. It goes down till the bottom of these three devices, examine literally every centimetre of the interior surface where it is necessary they clean, do repair works. It is the heart of our processes and we carefully keep an eye on its state,” said the chief engineer of the plant.
One of the main results of almost a year of work of the facility with a serious workload, besides the more than 90% recovery of high-quality light oil products per tonne of oil feedstock and production ramp-up at TAIF-NK is the examination of those innovations introduced during the construction of the facility.
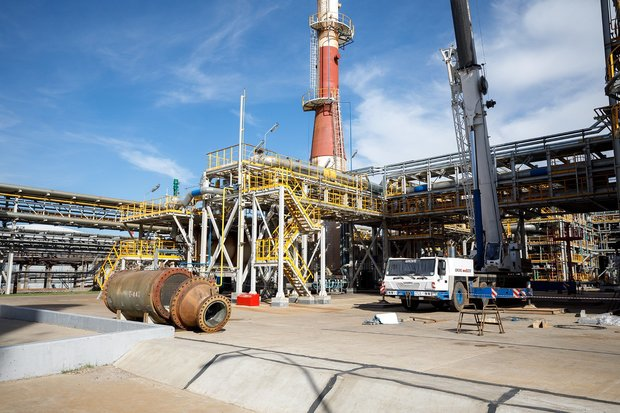
“During this period, we have accumulated a report on every device and those points we predict will have problem in the future, and we pay great attention to these points. We spend time and resources to make sure we will work with the same workload and without shutdowns next year. All that we are investing in expertise and surveys today is investments in trouble-free operation in the future. There were nodes and units to which we had questions. We have applied technical solutions and now, opening the equipment, we see that almost all the difficult moments are eliminated or completely leveled," Artur Urazaykin shared with undisguised pride.
Overhaul began with closed steaming
Andrey Minenkov, the chief mechanic of the production, became the guide of the Realnoe Vremya group on the territory of the TAIF-NK Gasoline Plant. According to him, before starting inspecting the equipment, the containers were completely freed from raw materials and intermediates. This is a mandatory part of the procedure for any oil refining production.
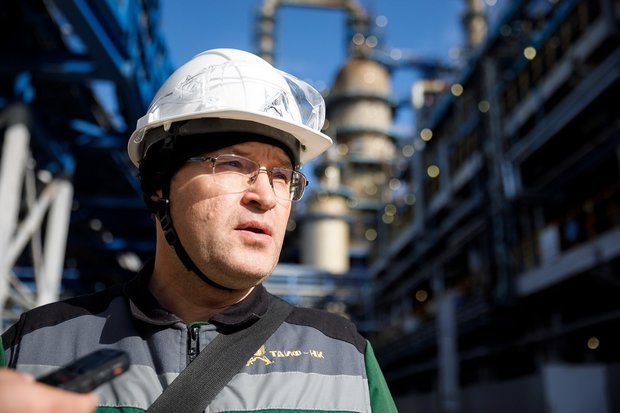
“We started with closed steaming using special reagents. During this procedure, special chemical agents are fed into the steam, which remove the smell, minimise the impact on both the environment and humans. The additives completely stop any harmful fumes," said Andrey Minenkov.
As at other production facilities of the complex, experts conducted a thorough thickness measurement of pipelines and equipment at the Gasoline Plant. In total, during the overhaul 2022, more than 200 pieces of equipment underwent the industrial safety expertise and technical diagnostics. A part was subjected not only to repair, but also to some improvement.
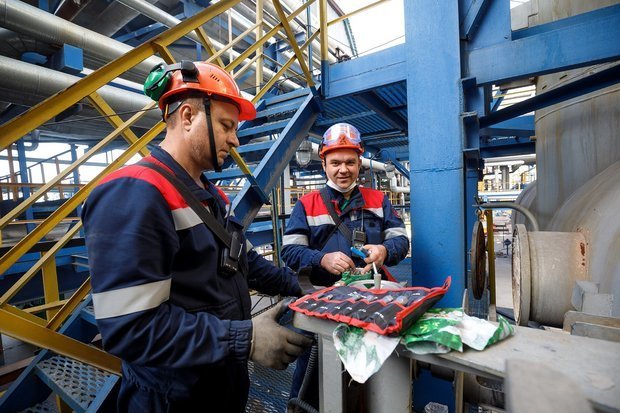
“According to the project of Avtotekhproekt, an organisation in Moscow, this year the next stage of replacing the lining with a more modern one has been performed on the regenerator. Lining is a layer of specialised concrete that prevents the impact of an aggressive environment on the metal body of the device. The old lining layer was dismantled, the wire mesh, with subsequent surface preparation, welding anchors and applying a lining mixture. This lining will reduce the number of repairs during operation," the chief mechanic of the Gasoline Plant explained to the journalist. He also added that single-layer protection is already available on part of the equipment, and it has proved to be much more reliable than multi-layer one. Besides, it has several times higher maintainability.
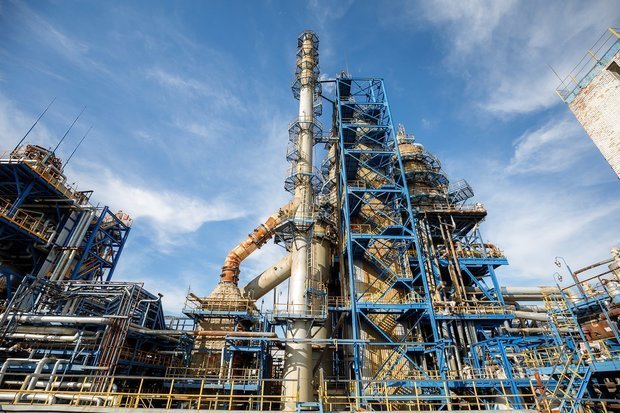
Also, during the repair, the economiser of the waste-heat boiler was replaced. The old one will soon be sent for recycling, and the new one will be ready for launch after being coated with an insulation layer. To dismantle the used equipment and install a new one in place, we had to order a special 400-tonne crane.
A slightly smaller crane, but also inspiring respect, is located in front of a row of column equipment.
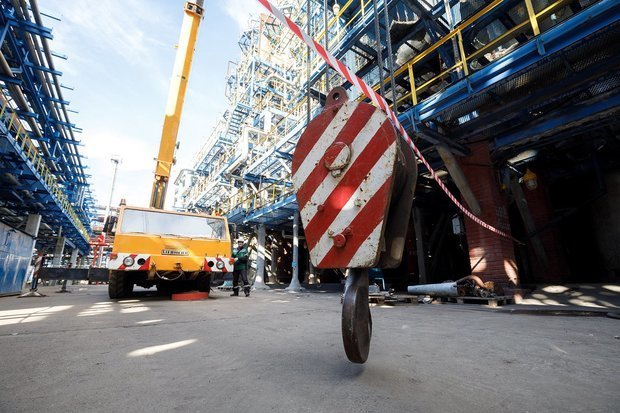
“Behind this equipment, there is a platform on which it is necessary to install safety valves that have been audited. They are quite heavy, and the location of the equipment is such that it can be done only with the help of special equipment and only from certain points. Moreover, not every crane will be able to cope with this," Andrey Minenkov told about what is happening.
Work is underway to check all systems, crimping of already repaired equipment is being carried out, insulation repairs are being carried out. The works on the replacement of the cooling tower are being completed. In parallel, a set of import substitution tasks is being solved.
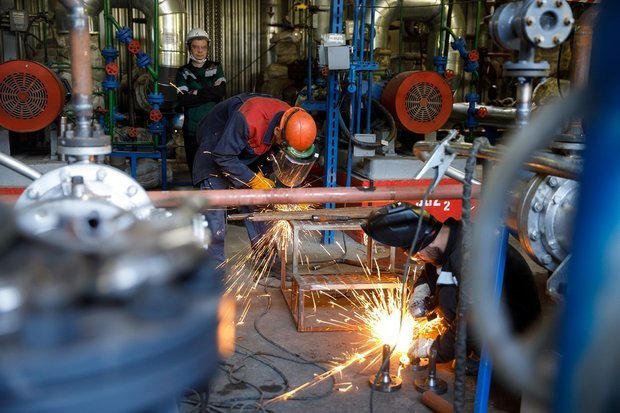
“At the moment, we are doing a lot of work on preparing the Siemens compressor for its modernisation. A contractor is working, carrying out the necessary measurements and calculations, and next year work will be carried out on modernisation — replacing the bundle and other elements with Russian production. Measures are also being taken to take measurements, determine the composition of seals of pumping and compressor equipment, which will later be manufactured as part of import substitution," said the chief mechanic of the Gasoline Plant.
Currently, active negotiations are underway with possible Russian contractors and other orders for the manufacture of parts, assemblies and equipment for the needs of the Gasoline Plant of TAIF-NK JSC.
Main mechanics of Russian production have united
The issue of import substitution is quite acute for the vast majority of Russian industries today. Rustam Bagaviev, the chief mechanic of TAIF-NK JSC, told the Realnoe Vremya journalist about this. The main mechanics of the country's enterprises decided to work together to solve the problem.
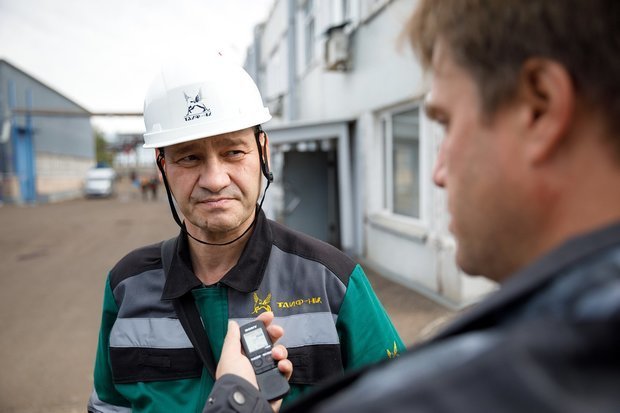
“We have organised the scientific and technical centre under the Council of Chief Mechanics, where the chief mechanics of Russia's leading industries work together to form a common base of service providers, manufacturers of materials, parts, spare parts, etc. for imported equipment. We have also created our own database of possible implementing companies. As part of this work, we inspect organisations, get acquainted with personnel, equipment, availability of laboratories, design departments, technical control. After each such inspection trip, our specialists create a report with a description of what we saw, a list of services that they can provide to us. Later, when choosing contractors, we use this database," Rustam Bagaviev shared.
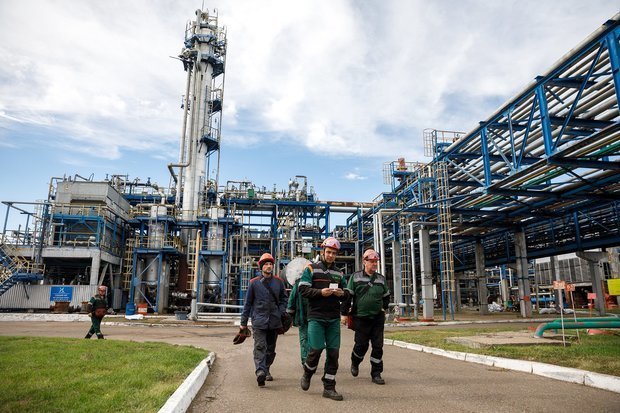
He also emphasised that, no matter how difficult the tasks faced by the staff of TAIF-NK JSC and the contractors involved in the complex are, the deadlines set aside for capital repairs are strictly maintained. The start of production facilities will be exactly on schedule.
Подписывайтесь на телеграм-канал, группу «ВКонтакте» и страницу в «Одноклассниках» «Реального времени». Ежедневные видео на Rutube и «Дзене».